公司规模
Large Corporate
地区
- America
- Europe
国家
- United States
- Germany
产品
- Plex Manufacturing Cloud ERP
技术栈
- Cloud ERP
实施规模
- Enterprise-wide Deployment
影响指标
- Productivity Improvements
- Cost Savings
- Customer Satisfaction
技术
- 功能应用 - 企业资源规划系统 (ERP)
适用行业
- 汽车
用例
- 库存管理
- 过程控制与优化
服务
- 系统集成
关于客户
Wolverine Advanced Materials is a supplier of vibration damping and sealing materials. The company experienced a significant increase in sales, growing by 10 to 13 percent over a two-year period. This growth overwhelmed their existing manual systems for managing raw material orders, inventories, shipping, and scheduling. Wolverine operates manufacturing facilities in Virginia, Florida, and Germany, and sought to implement a manufacturing-based ERP system to support their operations. The company aimed to transition to lean, demand-driven manufacturing to improve competitiveness, particularly against offshore competitors targeting their high-margin parts. Wolverine's complex operations involve a seven- to eight-layer bill of material with multiple processes and exit points, requiring careful sequencing of orders to optimize production.
挑战
Wolverine Advanced Materials faced significant challenges as their sales grew by 10 to 13 percent over a two-year period. Their existing manual systems for managing raw material orders, inventories, shipping, and scheduling could not keep up with the increased demand, leading to extended lead times of up to 10 weeks. The company needed to transition to a lean, demand-driven manufacturing model to remain competitive, especially against offshore competitors targeting their high-margin parts. Previous attempts to implement ERP systems had failed, partly due to resistance from mature employees unfamiliar with computers. The company required a solution that could streamline operations, improve inventory accuracy, and reduce lead times.
解决方案
Wolverine Advanced Materials implemented the Plex Manufacturing Cloud ERP system to address their operational challenges. The ERP system was deployed across their manufacturing facilities in Virginia, Florida, and Germany. The implementation began with the Purchasing function, focusing on raw material ordering and inventory management to ensure the right materials were available at the right time. This was followed by the Production Control and Scheduling functions. The Plex system provided real-time data entry at all workcenters on the shop floor, eliminating paper handling and improving efficiency. Employees, initially resistant to change, embraced the user-friendly Plex screens, facilitating a smoother transition. The ERP system enabled Wolverine to achieve accurate perpetual inventory, reduce lead times to five weeks, and double their aftermarket business. The system also allowed for efficient grouping of customer orders by material, improving productivity and reducing costs. The packaging process was customized to ensure accurate piece counts, reducing overages and allowing for the redeployment of staff.
运营影响
数量效益
Case Study missing?
Start adding your own!
Register with your work email and create a new case study profile for your business.
相关案例.
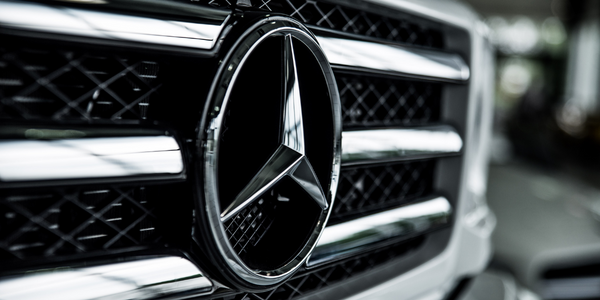
Case Study
Integral Plant Maintenance
Mercedes-Benz and his partner GAZ chose Siemens to be its maintenance partner at a new engine plant in Yaroslavl, Russia. The new plant offers a capacity to manufacture diesel engines for the Russian market, for locally produced Sprinter Classic. In addition to engines for the local market, the Yaroslavl plant will also produce spare parts. Mercedes-Benz Russia and his partner needed a service partner in order to ensure the operation of these lines in a maintenance partnership arrangement. The challenges included coordinating the entire maintenance management operation, in particular inspections, corrective and predictive maintenance activities, and the optimizing spare parts management. Siemens developed a customized maintenance solution that includes all electronic and mechanical maintenance activities (Integral Plant Maintenance).
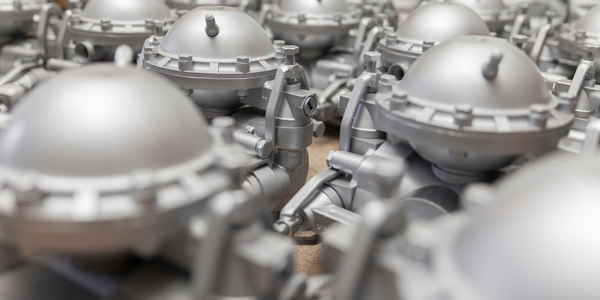
Case Study
Monitoring of Pressure Pumps in Automotive Industry
A large German/American producer of auto parts uses high-pressure pumps to deburr machined parts as a part of its production and quality check process. They decided to monitor these pumps to make sure they work properly and that they can see any indications leading to a potential failure before it affects their process.