公司规模
Large Corporate
地区
- America
国家
- United States
产品
- Plex Cloud ERP
- Plex Manufacturing Cloud
技术栈
- Cloud Computing
- Real-time MRP/ERP System
实施规模
- Enterprise-wide Deployment
影响指标
- Productivity Improvements
- Cost Savings
- Customer Satisfaction
技术
- 功能应用 - 企业资源规划系统 (ERP)
- 平台即服务 (PaaS) - 数据管理平台
适用行业
- 汽车
适用功能
- 商业运营
- 质量保证
用例
- 库存管理
- 过程控制与优化
- 预测性维护
服务
- 系统集成
- 软件设计与工程服务
关于客户
CAMACO is a leading provider of seating systems solutions and is recognized as the largest independent supplier of engineered seat frames to the North American automotive market. The company operates multiple facilities, including Columbus (Nebraska) Manufacturing, Lorain (Ohio) Manufacturing, and Lorain County (Ohio) Automotive Systems. CAMACO has been facing significant challenges in terms of productivity and cost-cutting requirements from its customers. The company was dealing with an outdated and unmanageable batch-process MRP system, which was causing frequent failures and data loss across its facilities. The existing system relied on a dial-up connection and was mapped to an MRP system driven from a PC, which often resulted in system mapping failures, unreliable PC performance, and modem connectivity issues. Additionally, the EDI software was outdated, and software support was no longer available. CAMACO needed a modern, integrated system to address these issues and reduce high maintenance costs and expensive hardware and software upgrades. The company sought a comprehensive solution that would eliminate the need for hiring additional staff or third-party developers for custom support.
挑战
CAMACO, a leading seating systems solutions provider, needed to replace its outdated, unmanageable batch-process MRP system with a completely integrated system. As the largest independent supplier of engineered seat frames to the North American automotive market, the company had been facing extreme productivity and cost-cutting requirements from its customers. CAMACO’s aged EDI system was experiencing frequent failures and lost data in all three of its facility locations: Columbus (Nebraska) Manufacturing; Lorain (Ohio) Manufacturing; and Lorain County (Ohio) Automotive Systems. The existing system used a dial-up connection, was mapped to an MRP system, was driven from a PC, and relied upon a modem to send and receive data. Sometimes the system mapping failed, the unreliable PC stopped working, or the modem would not dial out to the value-added network (VAN). Since the EDI software was also out of date, software support was no longer available. The company needed an up-to-date systems solution that would address its network issues while reducing its existing burden of high maintenance costs and expensive hardware and software upgrades. With an eye toward the future, CAMACO wanted more than just a base MRP/ERP system. It wanted an all-encompassing solution so it would not have to hire a database administrator or a third-party developer/consultant to design additional functions or provide custom support.
解决方案
After evaluating several MRP/ERP systems, CAMACO selected Plex Systems' Manufacturing Cloud ERP solution, which met all of its requirements. The solution provided CAMACO with a completely integrated, real-time MRP/ERP system at an acceptable cost. Plex's on-demand model and exceptional service allowed CAMACO to manage the new system without hiring additional staff. CAMACO launched Plex and found that the system provided more benefits than anticipated. Plex enabled CAMACO to improve its inventory management, traceability, productivity, and production planning, helping the company thrive despite industry economic challenges. CAMACO's Vice President of Operations, David Smith, first learned about Plex Systems at a technical seminar and viewed a Plex Cloud ERP demo. When faced with replacing its outdated MRP system, Smith recalled the system's capabilities and approached Plex Systems for a proposal. Plex Systems won the business, and CAMACO launched all core Plex functions at all of its locations. CAMACO was pleased to find it did not have to devote significant resources to the Plex launch. CAMACO-Columbus, one of the company's largest plants, assigned one person to the implementation. CAMACO-Lorain established a team of two dedicated staff. During implementation, the company brought in other employees from specific departments to assist as needed to prevent any disruption of daily business. Management found this was a great opportunity to train team members and foster improved communication among them. That familiarity has led to an added benefit today, as members of this informal Plex user group typically consult with each other to resolve issues, relay information, and share best practices.
运营影响
数量效益
Case Study missing?
Start adding your own!
Register with your work email and create a new case study profile for your business.
相关案例.
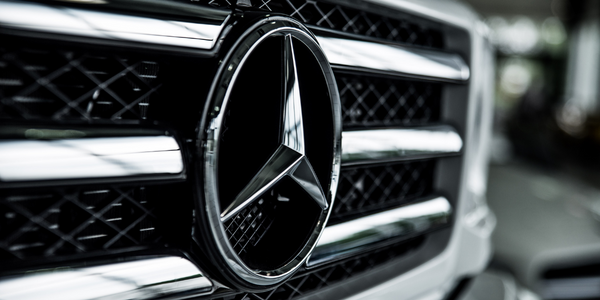
Case Study
Integral Plant Maintenance
Mercedes-Benz and his partner GAZ chose Siemens to be its maintenance partner at a new engine plant in Yaroslavl, Russia. The new plant offers a capacity to manufacture diesel engines for the Russian market, for locally produced Sprinter Classic. In addition to engines for the local market, the Yaroslavl plant will also produce spare parts. Mercedes-Benz Russia and his partner needed a service partner in order to ensure the operation of these lines in a maintenance partnership arrangement. The challenges included coordinating the entire maintenance management operation, in particular inspections, corrective and predictive maintenance activities, and the optimizing spare parts management. Siemens developed a customized maintenance solution that includes all electronic and mechanical maintenance activities (Integral Plant Maintenance).
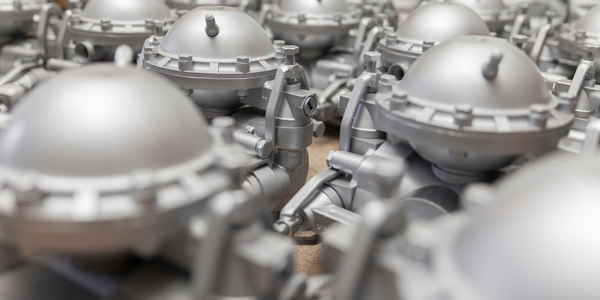
Case Study
Monitoring of Pressure Pumps in Automotive Industry
A large German/American producer of auto parts uses high-pressure pumps to deburr machined parts as a part of its production and quality check process. They decided to monitor these pumps to make sure they work properly and that they can see any indications leading to a potential failure before it affects their process.