公司规模
Large Corporate
地区
- America
国家
- United States
产品
- 3Gtms Transportation Management System
技术栈
- Database Management
- Customization Processes
实施规模
- Enterprise-wide Deployment
影响指标
- Productivity Improvements
- Customer Satisfaction
技术
- 功能应用 - 运输管理系统 (TMS)
适用功能
- 物流运输
用例
- 交通模拟
- 供应链可见性(SCV)
服务
- 软件设计与工程服务
关于客户
ODW Logistics, Inc. is a full-service 3PL provider of supply chain solutions for mid-sized and large companies. The company was established in 1971 and has more than 1,000 employees. ODW Logistics provides technology, infrastructure, and services to support businesses in a range of industries, including health and beauty, food and beverage, manufacturing, and consumer packaged goods. The company's transportation service began as an asset-based solution in the 1980s. Over the last decade, ODW’s non-asset based transportation execution has seen phenomenal growth. However, the company’s transportation management system (TMS) was not able to support its goals to acquire new business and offer differentiated services.
挑战
ODW Logistics, a full-service 3PL provider, was facing challenges with its transportation management system (TMS) which was built in the 1990s for a truckload business. The TMS was not able to support the company's goals to acquire new business and offer differentiated services, especially in the less-than-truckload (LTL) and brokerage environment. The company needed a TMS that could support the non-asset sides of the business and leverage its in-house database and development expertise. It was also important for the new TMS to support and strengthen the company's competitive advantage of delivering fast, customized services that allowed customers to adjust to changing market demands.
解决方案
ODW Logistics chose 3Gtms, a Tier 1 transportation management system with rich functionality, flexibility, and modern technology to drive efficiency and automation throughout the entire order-to-settlement lifecycle. Unlike other offerings that were built decades ago, 3Gtms technology addresses today’s market needs and complexities. Built on one scalable platform that leverages the same data throughout the application, 3Gtms helps ODW expand and grow its non-asset line of business. 3Gtms’ deep industry and software knowledge also impressed ODW. The company was confident that 3Gtms understood their needs and knew how to address them quickly with the best approach. While some TMS vendors had a lower cost-per-transaction in the short term, 3Gtms was a better long-term investment because of ODW’s ability to customize processes itself and react quickly to market changes.
运营影响
Case Study missing?
Start adding your own!
Register with your work email and create a new case study profile for your business.
相关案例.
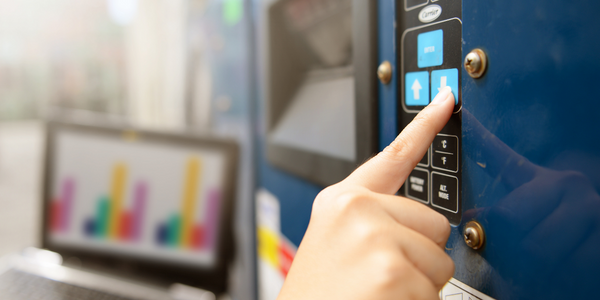
Case Study
Remote Temperature Monitoring of Perishable Goods Saves Money
RMONI was facing temperature monitoring challenges in a cold chain business. A cold chain must be established and maintained to ensure goods have been properly refrigerated during every step of the process, making temperature monitoring a critical business function. Manual registration practice can be very costly, labor intensive and prone to mistakes.
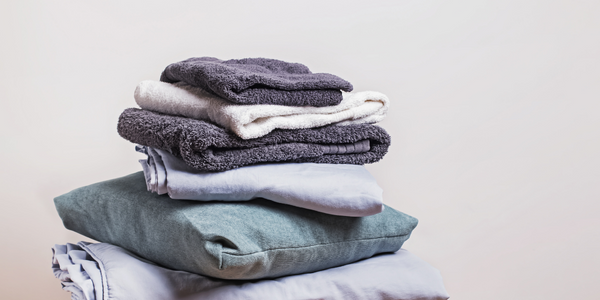
Case Study
Retail Uses RFID to Enable Cold Chain Monitoring
Like most grocery retailers, Hy-Vee is faced with the challenge of providing the highest quality products to its shoppers. Shoppers want the longest possible shelf life from perishable products and expect a consistent product experience each time they shop. Controlling the quality of products sold leads to shopper loyalty, which is of paramount importance to the success of Hy-Vee. Before products arrive in stores, Hy-Vee's distribution centers (DCs) handle items including dairy products, fresh meats, seafood, deli items, produce and frozen goods, all of which have different temperature needs and sensitivities. During transit from suppliers to DCs, Hy-Vee has limited visibility and temperature management abilities due to large amount of supplier managed transportation. For instance, during a week-long transit, a supplier's carrier equipment may malfunction, causing an item to thaw and then refreeze once repairs are made. Hy-Vee sought help from TempTRIP, an RFID solution provider that focuses on shipping, storage, receiving, and temperature control. TempTRIP's EPC RFID tags use Impinj chips to monitor and report temperature readings throughout the shipping and receiving process. The tags can also be re-configured and re-used, a unique feature within the current market of temperature monitoring devices.
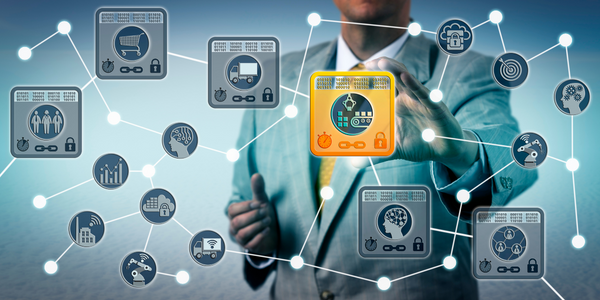
Case Study
Covisint Improves Mitsubishi's Collaboration With Its Supply Chain
Mitsubishi sought to improve supplier relationships on a global basis and to offer an easy-to-use solution to interact with them. In August 2004, Mitsubishi selected Covisint’s platform to help improve sharing of information and collaborative business processes with its global suppliers. Covisint enabled Mitsubishi to provide its suppliers with immediate access to information and applications to obtain more collaborative working relationships