公司规模
Large Corporate
地区
- Pacific
国家
- Australia
产品
- Measurabl
技术栈
- GRESB Debrief
- Automated utility collection
实施规模
- Enterprise-wide Deployment
影响指标
- Environmental Impact Reduction
- Brand Awareness
- Customer Satisfaction
技术
- 平台即服务 (PaaS) - 数据管理平台
适用功能
- 设施管理
用例
- 建筑能源管理
- 能源管理系统
服务
- 数据科学服务
关于客户
Pro-invest Group is an asset manager and investment firm founded in 2010. The company specializes in private equity real estate asset management and has become one of the largest hotel investment platforms in Australasia. With assets under management close to AUD 2bn, Pro-invest operates as a locally established, integrated private equity real estate business. The company combines active asset management, development, and operational capabilities to provide its investors with above-industry risk-adjusted returns in the hospitality, development, and retail spaces. Pro-invest has more than 30 sector-specific specialists based in its Sydney office.
挑战
Pro-invest Group, a member of INREV and builder of Australia’s first 5-star NABERS hotel, initially lacked a dedicated ESG team. When they decided to report to GRESB for the first time, the task was handled by the Fund Manager and Group Chief Financial Officer. The process involved a detailed 90+ page survey that required an in-depth look into the ESG efforts at both the company and asset level. Despite the challenges, reporting to GRESB provided transparency that assured investors of Pro-invest’s commitment to ESG and aligned internal stakeholders with a common goal. After their second year of reporting, with dedicated sustainability resources and a full-time in-house ESG Coordinator, Pro-invest was able to more than double their score, but they knew they could do even better.
解决方案
Pro-invest Group decided to use Measurabl’s GRESB Debrief to improve their GRESB results. Measurabl reviewed Pro-invest’s survey to provide insight into strengths and opportunities for improvement. Pro-invest was able to compare their findings with the Debrief to validate and shed light on areas they could advance. As the relationship with Measurabl progressed during the Debrief, Pro-invest realized that features such as automated utility collection and alignment with other frameworks like GRI could drastically reduce the time-consuming aspects of disclosure. They signed on to become a Measurabl customer in 2018 to push for a record-breaking 2019.
运营影响
数量效益
Case Study missing?
Start adding your own!
Register with your work email and create a new case study profile for your business.
相关案例.
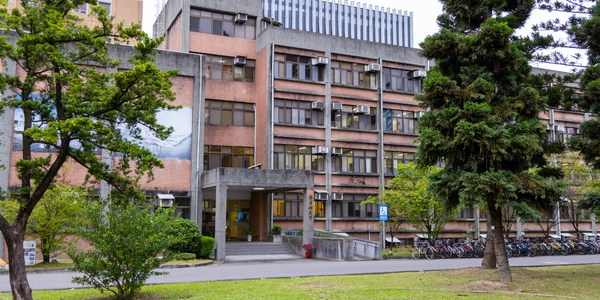
Case Study
Energy Saving & Power Monitoring System
Recently a university in Taiwan was experiencing dramatic power usage increases due to its growing number of campus buildings and students. Aiming to analyze their power consumption and increase their power efficiency across 52 buildings, the university wanted to build a power management system utilizing web-based hardware and software. With these goals in mind, they contacted Advantech to help them develop their system and provide them with the means to save energy in the years to come.
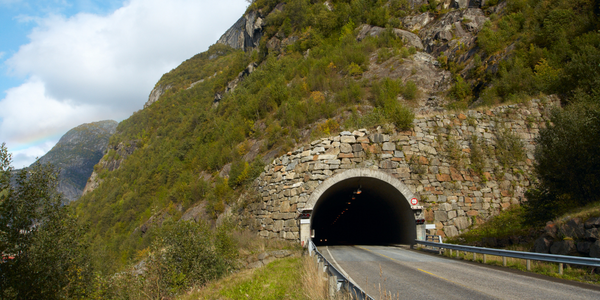
Case Study
IoT System for Tunnel Construction
The Zenitaka Corporation ('Zenitaka') has two major business areas: its architectural business focuses on structures such as government buildings, office buildings, and commercial facilities, while its civil engineering business is targeted at structures such as tunnels, bridges and dams. Within these areas, there presented two issues that have always persisted in regard to the construction of mountain tunnels. These issues are 'improving safety" and "reducing energy consumption". Mountain tunnels construction requires a massive amount of electricity. This is because there are many kinds of electrical equipment being used day and night, including construction machinery, construction lighting, and ventilating fan. Despite this, the amount of power consumption is generally not tightly managed. In many cases, the exact amount of power consumption is only ascertained when the bill from the power company becomes available. Sometimes, corporations install demand-monitoring equipment to help curb the maximum power demanded. However, even in these cases, the devices only allow the total volume of power consumption to be ascertained, or they may issue warnings to prevent the contracted volume of power from being exceeded. In order to tackle the issue of reducing power consumption, it was first necessary to obtain an accurate breakdown of how much power was being used in each particular area. In other words, we needed to be able to visualize the amount of power being consumed. Safety, was also not being managed very rigorously. Even now, tunnel construction sites often use a 'name label' system for managing entry into the work site. Specifically, red labels with white reverse sides that bear the workers' names on both sides are displayed at the tunnel work site entrance. The workers themselves then flip the name label to the appropriate side when entering or exiting from the work site to indicate whether or not they are working inside the tunnel at any given time. If a worker forgets to flip his or her name label when entering or exiting from the tunnel, management cannot be performed effectively. In order to tackle the challenges mentioned above, Zenitaka decided to build a system that could improve the safety of tunnel construction as well as reduce the amount of power consumed. In other words, this new system would facilitate a clear picture of which workers were working in each location at the mountain tunnel construction site, as well as which processes were being carried out at those respective locations at any given time. The system would maintain the safety of all workers while also carefully controlling the electrical equipment to reduce unnecessary power consumption. Having decided on the concept, our next concern was whether there existed any kind of robust hardware that would not break down at the construction work site, that could move freely in response to changes in the working environment, and that could accurately detect workers and vehicles using radio frequency identification (RFID). Given that this system would involve many components that were new to Zenitaka, we decided to enlist the cooperation of E.I.Sol Co., Ltd. ('E.I.Sol') as our joint development partner, as they had provided us with a highly practical proposal.
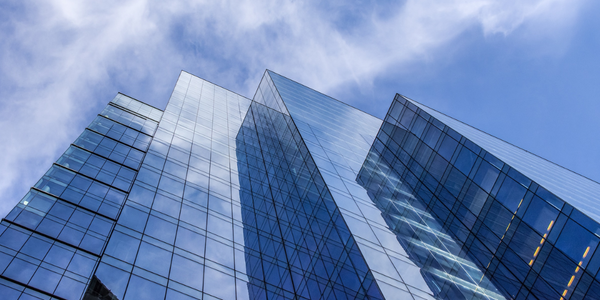
Case Study
Intelligent Building Automation System and Energy Saving Solution
One of the most difficult problems facing the world is conserving energy in buildings. However, it is not easy to have a cost-effective solution to reduce energy usage in a building. One solution for saving energy is to implement an intelligent building automation system (BAS) which can be controlled according to its schedule. In Indonesia a large university with a five floor building and 22 classrooms wanted to save the amount of energy being used.
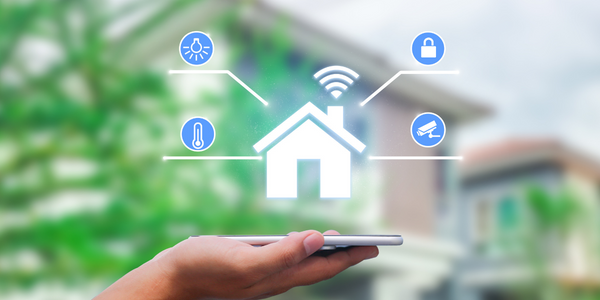
Case Study
Powering Smart Home Automation solutions with IoT for Energy conservation
Many industry leaders that offer Smart Energy Management products & solutions face challenges including:How to build a scalable platform that can automatically scale-up to on-board ‘n’ number of Smart home devicesData security, solution availability, and reliability are the other critical factors to deal withHow to create a robust common IoT platform that handles any kind of smart devicesHow to enable data management capabilities that would help in intelligent decision-making
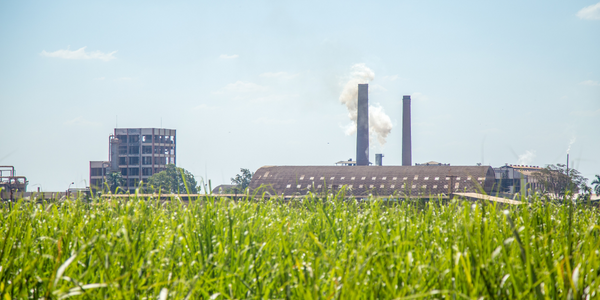
Case Study
Energy Management System at Sugar Industry
The company wanted to use the information from the system to claim under the renewable energy certificate scheme. The benefit to the company under the renewable energy certificates is Rs 75 million a year. To enable the above, an end-to-end solution for load monitoring, consumption monitoring, online data monitoring, automatic meter data acquisition which can be exported to SAP and other applications is required.
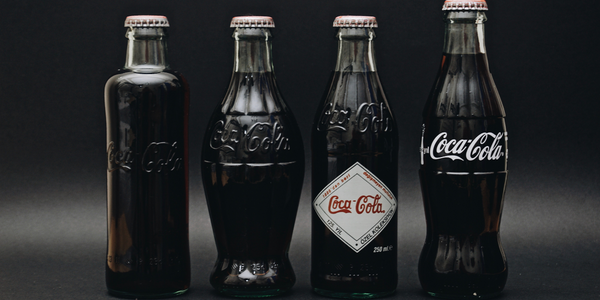
Case Study
Coca Cola Swaziland Conco Case Study
Coco Cola Swaziland, South Africa would like to find a solution that would enable the following results: - Reduce energy consumption by 20% in one year. - Formulate a series of strategic initiatives that would enlist the commitment of corporate management and create employee awareness while helping meet departmental targets and investing in tools that assist with energy management. - Formulate a series of tactical initiatives that would optimize energy usage on the shop floor. These would include charging forklifts and running cold rooms only during off-peak periods, running the dust extractors only during working hours and basing lights and air-conditioning on someone’s presence. - Increase visibility into the factory and other processes. - Enable limited, non-intrusive control functions for certain processes.