公司规模
Large Corporate
地区
- Europe
国家
- Germany
产品
- Sphera’s Sustainability Consulting services
技术栈
- Life Cycle Assessment (LCA) models
实施规模
- Enterprise-wide Deployment
影响指标
- Environmental Impact Reduction
- Brand Awareness
技术
- 分析与建模 - 过程分析
适用行业
- 汽车
适用功能
- 物流运输
- 采购
用例
- 供应链可见性(SCV)
- 能源管理系统
关于客户
Mercedes-Benz is a globally recognized automotive company founded in 1926 and headquartered in Stuttgart, Germany. The company has a significant presence with over 173,000 employees and 40 production sites spread across four continents. In 2019, the company sold nearly 2.4 million cars and more than 438,000 vans. As part of their commitment to environmental sustainability, Mercedes-Benz has set an ambitious goal, Ambition 2039, to become a carbon-neutral company by 2039. This commitment extends beyond the emissions produced by their vehicles to include those that occur during the production process, a significant proportion of which occur within its supply chain.
挑战
Mercedes-Benz, as part of their Ambition 2039, committed to becoming a carbon-neutral company by 2039 across their entire value chain. This includes not only the emissions produced by their vehicles but also those that occur during the production process. A significant proportion of these emissions occur not at Mercedes-Benz locations, but within its supply chain. To develop a realistic yet ambitious decarbonization strategy, it was crucial to gain transparency about emissions hotspots in the supply chain and quantify possible reduction measures. However, the company faced challenges such as missing emissions transparency in the supply chain, lack of reliable, detailed emissions inventories for steel, aluminum, and plastics, lack of knowledge about the influence of renewable energy and recycled or bio-based materials and their impacts on supply chain emissions, and lack of CO2 reductions potentials for target setting.
解决方案
To address these challenges, Mercedes-Benz decided to use Sphera’s consulting services and their detailed life cycle assessment (LCA) models and supply chain knowledge. Sphera’s consultants conducted a detailed CO2-modelling of the supply chains for steel, aluminum, and plastics and derived and quantified possible reduction measures. This involved alternative production routes for steel, including steel via direct reduced iron, renewable energy used in the supply chain of aluminum and plastics, and the use of secondary and bio-based materials. Additional environmental impacts, such as acidification, water consumption, etc., were considered wherever needed and relevant. Sphera’s Sustainability Consulting services enable companies to build business value from sustainability, gain new investments, and future-proof their businesses by providing insight into the concepts behind decarbonization and net zero, helping organizations to assess their status quo, and developing a decarbonization roadmap suitable for a specific business model.
运营影响
Case Study missing?
Start adding your own!
Register with your work email and create a new case study profile for your business.
相关案例.
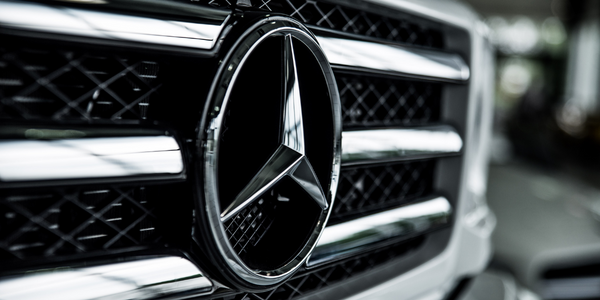
Case Study
Integral Plant Maintenance
Mercedes-Benz and his partner GAZ chose Siemens to be its maintenance partner at a new engine plant in Yaroslavl, Russia. The new plant offers a capacity to manufacture diesel engines for the Russian market, for locally produced Sprinter Classic. In addition to engines for the local market, the Yaroslavl plant will also produce spare parts. Mercedes-Benz Russia and his partner needed a service partner in order to ensure the operation of these lines in a maintenance partnership arrangement. The challenges included coordinating the entire maintenance management operation, in particular inspections, corrective and predictive maintenance activities, and the optimizing spare parts management. Siemens developed a customized maintenance solution that includes all electronic and mechanical maintenance activities (Integral Plant Maintenance).
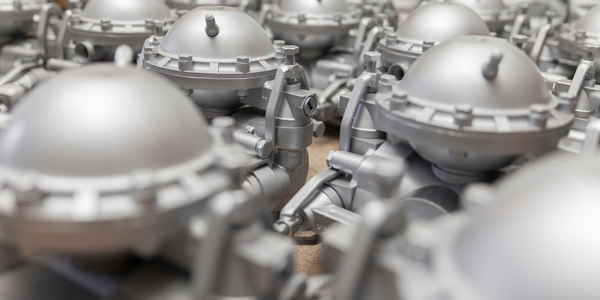
Case Study
Monitoring of Pressure Pumps in Automotive Industry
A large German/American producer of auto parts uses high-pressure pumps to deburr machined parts as a part of its production and quality check process. They decided to monitor these pumps to make sure they work properly and that they can see any indications leading to a potential failure before it affects their process.