公司规模
Large Corporate
地区
- Europe
国家
- Czech Republic
- Germany
产品
- MES HYDRA
- Microsoft Dynamics AX
技术栈
- Manufacturing Execution System (MES)
- ERP System
实施规模
- Enterprise-wide Deployment
影响指标
- Energy Saving
- Productivity Improvements
技术
- 功能应用 - 制造执行系统 (MES)
- 功能应用 - 企业资源规划系统 (ERP)
适用行业
- 汽车
- 消费品
适用功能
- 流程制造
- 质量保证
用例
- 机器状态监测
- 预测性维护
- 能源管理系统
服务
- 系统集成
- 软件设计与工程服务
关于客户
RUCH NOVAPLAST GmbH + Co. KG is a leading European specialist in the development and production of foamed pieces made from expanded polystyrene (EPS) and expanded polypropylene (EPP). The company positions itself as a systems supplier and development partner for various industries. With an in-house team of engineers, RUCH NOVAPLAST creates innovative solutions for packaging, load carriers, automotive parts, protective padding, robot trays, insulation, and molded parts for the leisure industry. The company has a strong focus on innovation and efficiency, having recognized early on the benefits of collecting shop floor and machine data. This forward-thinking approach has positioned RUCH NOVAPLAST as a leader in its field, continually seeking to enhance its operational capabilities through advanced technology solutions.
挑战
In 2009, RUCH NOVAPLAST GmbH + Co. KG sought an integrated Manufacturing Execution System (MES) to address multiple operational needs. The company required a system capable of shop floor and machine data collection, batch tracing, quality data collection, and recording of working hours and access control. Additionally, the system needed to integrate seamlessly with their existing ERP system, Microsoft Dynamics AX, and ensure investment reliability. The challenge was to find a solution that could meet these diverse requirements while also being accepted by all departments involved.
解决方案
After an extensive selection process, RUCH NOVAPLAST chose MPDV's MES HYDRA to meet their operational needs. The system was selected for its ability to cover all required evaluations in its standard version. MES HYDRA allows every staff member to view the current machine status at all times, with a 46” display in the production halls showing individual machine statuses. This visibility enables prompt countermeasures if critical machines are not working. The HYDRA module for Material & Production Logistics documents traceability, and quality inspections are carried out from goods-in to goods-out. Future plans include the use of electronic control charts. Additionally, HYDRA Energy Management is used to analyze energy consumption related to orders, allowing for specific optimization measures. In 2012, the old system for collecting working hours and time management was replaced by HYDRA modules for Time & Attendance, Personnel Time Management, and Access Control. By 2013, the system was successfully rolled out to the site in the Czech Republic, MORAplast s.r.o.
运营影响
数量效益
Case Study missing?
Start adding your own!
Register with your work email and create a new case study profile for your business.
相关案例.
.png)
Case Study
Improving Vending Machine Profitability with the Internet of Things (IoT)
The vending industry is undergoing a sea change, taking advantage of new technologies to go beyond just delivering snacks to creating a new retail location. Intelligent vending machines can be found in many public locations as well as company facilities, selling different types of goods and services, including even computer accessories, gold bars, tickets, and office supplies. With increasing sophistication, they may also provide time- and location-based data pertaining to sales, inventory, and customer preferences. But at the end of the day, vending machine operators know greater profitability is driven by higher sales and lower operating costs.
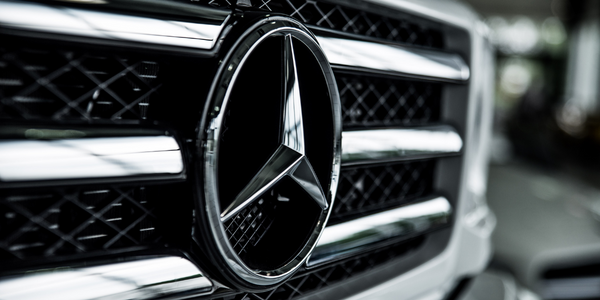
Case Study
Integral Plant Maintenance
Mercedes-Benz and his partner GAZ chose Siemens to be its maintenance partner at a new engine plant in Yaroslavl, Russia. The new plant offers a capacity to manufacture diesel engines for the Russian market, for locally produced Sprinter Classic. In addition to engines for the local market, the Yaroslavl plant will also produce spare parts. Mercedes-Benz Russia and his partner needed a service partner in order to ensure the operation of these lines in a maintenance partnership arrangement. The challenges included coordinating the entire maintenance management operation, in particular inspections, corrective and predictive maintenance activities, and the optimizing spare parts management. Siemens developed a customized maintenance solution that includes all electronic and mechanical maintenance activities (Integral Plant Maintenance).