公司规模
Large Corporate
地区
- Europe
- Asia
- Middle East
国家
- Germany
- Czech Republic
- Malaysia
- Saudi Arabia
- Spain
- United Kingdom
产品
- HYDRA by MPDV
- HYDRA Time & Attendance
- HYDRA Access Control
- HYDRA Shop Floor Scheduling
- HYDRA CAQ module
技术栈
- Windows Server
- MS-SQL database
- SAP HR & PP interfaces
实施规模
- Enterprise-wide Deployment
影响指标
- Digital Expertise
- Productivity Improvements
技术
- 功能应用 - 制造执行系统 (MES)
- 应用基础设施与中间件 - API 集成与管理
适用行业
- 化学品
- 金属
适用功能
- 流程制造
- 质量保证
服务
- 软件设计与工程服务
- 系统集成
关于客户
Schmidt + Clemens GmbH & Co. KG is a family-owned business established in 1879, specializing in the production of high-alloy stainless steel. Their products are widely used in the chemical and petrochemical industries, as well as in separating technology and turbine construction. The company is renowned for its expertise in vertical and horizontal centrifugal casting. With over 1,000 employees, Schmidt + Clemens operates in multiple locations, including Germany, Spain, Great Britain, the Czech Republic, Malaysia, and Saudi Arabia. The company is recognized globally for its superior stainless steel products and exceptional services, with 'Made by S+C' being synonymous with quality and reliability.
挑战
In the summer of 2007, Schmidt + Clemens faced the challenge of replacing their outdated systems for time and attendance and access control. They required a new system that could integrate seamlessly with SAP for various functions such as maintenance, shop floor scheduling, production control, DNC operation, and machine data collection. The company sought a modular and powerful MES solution from a reputable supplier with extensive SAP expertise and a certified SAP interface. The goal was to enhance their operational efficiency and ensure smooth data flow between different systems.
解决方案
After an extensive search, Schmidt + Clemens decided to implement the HYDRA MES system by MPDV in December 2007. The system was chosen for its modular structure, adherence to VDI 5600 guidelines, and the supplier's vast SAP knowledge. The implementation began with the HYDRA modules for Time & Attendance and Access Control, which were successfully introduced in February 2008. These modules allowed S+C to efficiently manage clock-in and clock-out times, break times, and secure access to sites and offices. The data collected was seamlessly transmitted to SAP HR via the certified HR-PDC interface. Subsequently, additional HYDRA modules were deployed, including Shop Floor and Machine Data Collection, DNC operation, and Shop Floor Scheduling. These modules facilitated detailed planning and automatic machine parameter uploads and downloads. Later, the Material & Production Logistics and Tracking & Tracing modules were implemented, enabling comprehensive documentation of production processes and the generation of manufacturer certificates.
运营影响
数量效益
Case Study missing?
Start adding your own!
Register with your work email and create a new case study profile for your business.
相关案例.
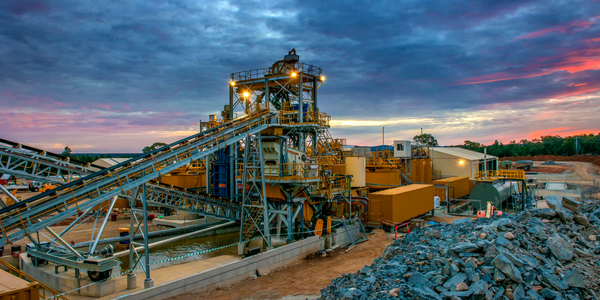
Case Study
Goldcorp: Internet of Things Enables the Mine of the Future
Goldcorp is committed to responsible mining practices and maintaining maximum safety for its workers. At the same time, the firm is constantly exploring ways to improve the efficiency of its operations, extend the life of its assets, and control costs. Goldcorp needed technology that can maximize production efficiency by tracking all mining operations, keep employees safe with remote operations and monitoring of hazardous work areas and control production costs through better asset and site management.
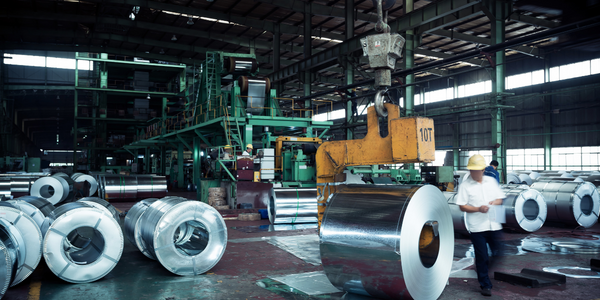
Case Study
KSP Steel Decentralized Control Room
While on-site in Pavlodar, Kazakhstan, the DAQRI team of Business Development and Solutions Architecture personnel worked closely with KSP Steel’s production leadership to understand the steel production process, operational challenges, and worker pain points.
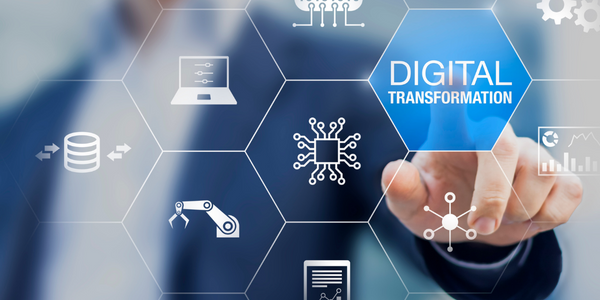
Case Study
Bluescope Steel on Path to Digitally Transform Operations and IT
Increasing competition and fluctuations in the construction market prompted BlueScope Steel to look toward digital transformation of its four businesses, including modern core applications and IT infrastructure. BlueScope needed to modernize its infrastructure and adopt new technologies to improve operations and supply chain efficiency while maintaining and updating an aging application portfolio.
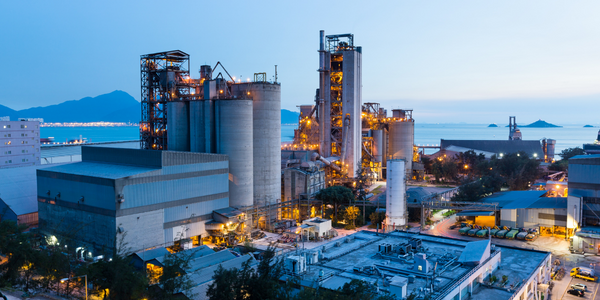
Case Study
Honeywell - Tata Chemicals Improves Data Accessibility with OneWireless
Tata was facing data accessibility challenges in the cement plant control room tapping signals from remote process control areas and other distant locations, including the gas scrubber. Tata needed a wireless solution to extend its control network securely to remote locations that would also provide seamless communication with existing control applications.
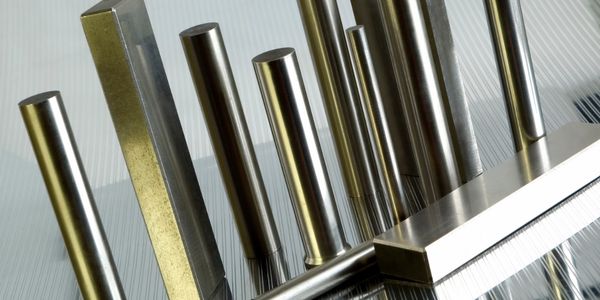
Case Study
RobotStudio Case Study: Benteler Automobiltechnik
Benteler has a small pipe business area for which they produce fuel lines and coolant lines made of aluminum for Porsche and other car manufacturers. One of the problems in production was that when Benteler added new products, production had too much downtime.

Case Study
Advanced Elastomer Systems Upgrades Production
In order to maintain its share of the international market for thermoplastic elastomers AES recently expanded its Florida plant by adding a new production line. While the existing lines were operating satisfactorily using a PROVOX distributed control system with traditional analog I/O, AES wanted advanced technology on the new line for greater economy, efficiency, and reliability. AES officials were anxious to get this line into production to meet incoming orders, but two hurricanes slowed construction.