公司规模
Mid-size Company
地区
- America
- Pacific
国家
- United States
- Australia
产品
- Documoto
- Rig>ID
技术栈
- SaaS
- Digital Publishing Platform
- Interactive Content Management System
实施规模
- Enterprise-wide Deployment
影响指标
- Productivity Improvements
- Customer Satisfaction
技术
- 平台即服务 (PaaS) - 数据管理平台
适用行业
- 石油和天然气
- 矿业
- 建筑与基础设施
适用功能
- 产品研发
- 质量保证
用例
- 供应链可见性(SCV)
- 库存管理
服务
- 云规划/设计/实施服务
- 软件设计与工程服务
关于客户
Schramm is a US and Australian manufacturer and global supplier to the hydraulic drilling industry. They focus on land-based applications and specialize in mobile, top-head hydraulic rotary drilling drills. Schramm services companies in the mineral exploration, grade control, water well, geothermal, construction, and oil and gas sectors worldwide. Founded in 1900, the company began by manufacturing engine-driven machinery and portable air compressors. Over the years, Schramm has pioneered air flush drilling and engineered and manufactured top-head drive mobile drilling equipment. In 1994, they formalized their relationship with AirDrill, making it the sole distributor for Schramm’s drilling rigs in the Australian and international RC markets. This partnership benefited the global gas, mineral, water well, and oilfield drilling industries. In 2013, Schramm acquired AirDrill and established Schramm Australia. Today, Schramm is a new business focused on growing its product portfolio of reliable drilling rigs to include Hammers and Bits, rig parts, and support and service capabilities.
挑战
Schramm, a manufacturer and global supplier to the hydraulic drilling industry, was facing challenges with their parts book processes. The company was producing generic parts books that were not customized to the customers' rigs. The process of creating these books was lengthy and time-consuming. Some illustrations were hand-drawn, out of date, or incorrect. If there were any engineering changes, they could not be easily added to the parts books in the field. This led to inefficiencies and difficulties in providing accurate and up-to-date information to their customers. The company needed a solution that could improve their publishing process, automate parts book publishing, and provide secure online access to parts information for their global network of customers and dealers.
解决方案
Schramm decided to implement Documoto's solution to address their parts book challenges. The Documoto Professional Services team worked with Schramm's publishing staff to guide the implementation process. After the company's cloud environment was configured and the publishing staff attended Documoto training, they began migrating parts data and illustrations into the new system. With the help of the Documoto Professional Services staff, Schramm's Documoto portal, which they call 'Rig Instant Documentation (Rig>ID)', was rolled out to a select group of customers for initial testing. Today, Schramm's Rig>ID portal users rely heavily on the portal for accurate parts information. The implementation of Documoto's solution has helped Schramm improve their publishing processes and release timeframes, enhance customer support, and provide a way to connect with their Australian counterparts.
运营影响
数量效益
Case Study missing?
Start adding your own!
Register with your work email and create a new case study profile for your business.
相关案例.
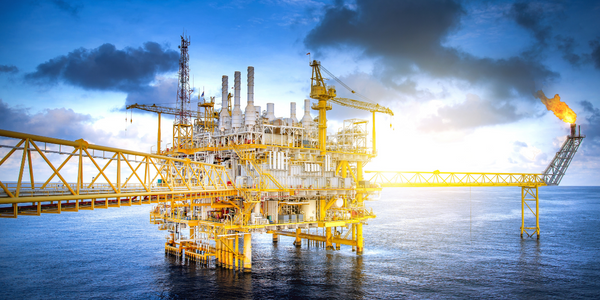
Case Study
Taking Oil and Gas Exploration to the Next Level
DownUnder GeoSolutions (DUG) wanted to increase computing performance by 5 to 10 times to improve seismic processing. The solution must build on current architecture software investments without sacrificing existing software and scale computing without scaling IT infrastructure costs.
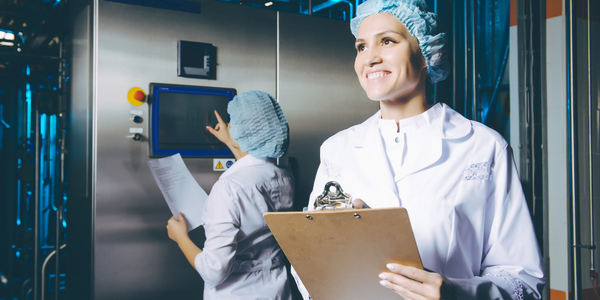
Case Study
Remote Wellhead Monitoring
Each wellhead was equipped with various sensors and meters that needed to be monitored and controlled from a central HMI, often miles away from the assets in the field. Redundant solar and wind generators were installed at each wellhead to support the electrical needs of the pumpstations, temperature meters, cameras, and cellular modules. In addition to asset management and remote control capabilities, data logging for remote surveillance and alarm notifications was a key demand from the customer. Terra Ferma’s solution needed to be power efficient, reliable, and capable of supporting high-bandwidth data-feeds. They needed a multi-link cellular connection to a central server that sustained reliable and redundant monitoring and control of flow meters, temperature sensors, power supply, and event-logging; including video and image files. This open-standard network needed to interface with the existing SCADA and proprietary network management software.
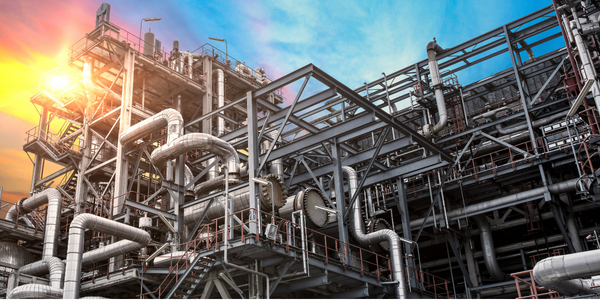
Case Study
Refinery Saves Over $700,000 with Smart Wireless
One of the largest petroleum refineries in the world is equipped to refine various types of crude oil and manufacture various grades of fuel from motor gasoline to Aviation Turbine Fuel. Due to wear and tear, eight hydrogen valves in each refinery were leaking, and each cost $1800 per ton of hydrogen vented. The plant also had leakage on nearly 30 flare control hydrocarbon valves. The refinery wanted a continuous, online monitoring system that could catch leaks early, minimize hydrogen and hydrocarbon production losses, and improve safety for maintenance.
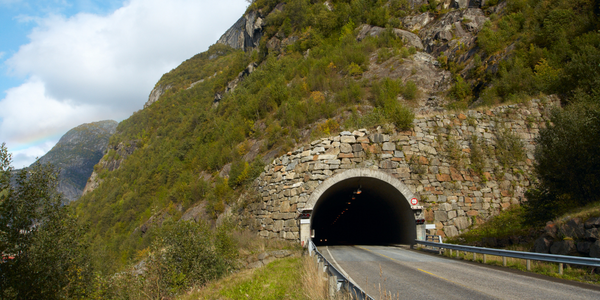
Case Study
IoT System for Tunnel Construction
The Zenitaka Corporation ('Zenitaka') has two major business areas: its architectural business focuses on structures such as government buildings, office buildings, and commercial facilities, while its civil engineering business is targeted at structures such as tunnels, bridges and dams. Within these areas, there presented two issues that have always persisted in regard to the construction of mountain tunnels. These issues are 'improving safety" and "reducing energy consumption". Mountain tunnels construction requires a massive amount of electricity. This is because there are many kinds of electrical equipment being used day and night, including construction machinery, construction lighting, and ventilating fan. Despite this, the amount of power consumption is generally not tightly managed. In many cases, the exact amount of power consumption is only ascertained when the bill from the power company becomes available. Sometimes, corporations install demand-monitoring equipment to help curb the maximum power demanded. However, even in these cases, the devices only allow the total volume of power consumption to be ascertained, or they may issue warnings to prevent the contracted volume of power from being exceeded. In order to tackle the issue of reducing power consumption, it was first necessary to obtain an accurate breakdown of how much power was being used in each particular area. In other words, we needed to be able to visualize the amount of power being consumed. Safety, was also not being managed very rigorously. Even now, tunnel construction sites often use a 'name label' system for managing entry into the work site. Specifically, red labels with white reverse sides that bear the workers' names on both sides are displayed at the tunnel work site entrance. The workers themselves then flip the name label to the appropriate side when entering or exiting from the work site to indicate whether or not they are working inside the tunnel at any given time. If a worker forgets to flip his or her name label when entering or exiting from the tunnel, management cannot be performed effectively. In order to tackle the challenges mentioned above, Zenitaka decided to build a system that could improve the safety of tunnel construction as well as reduce the amount of power consumed. In other words, this new system would facilitate a clear picture of which workers were working in each location at the mountain tunnel construction site, as well as which processes were being carried out at those respective locations at any given time. The system would maintain the safety of all workers while also carefully controlling the electrical equipment to reduce unnecessary power consumption. Having decided on the concept, our next concern was whether there existed any kind of robust hardware that would not break down at the construction work site, that could move freely in response to changes in the working environment, and that could accurately detect workers and vehicles using radio frequency identification (RFID). Given that this system would involve many components that were new to Zenitaka, we decided to enlist the cooperation of E.I.Sol Co., Ltd. ('E.I.Sol') as our joint development partner, as they had provided us with a highly practical proposal.