公司规模
Mid-size Company
地区
- America
国家
- United States
产品
- Plex ERP
- Plex Smart Manufacturing Platform
- QAD
技术栈
- Cloud-based ERP
- Barcode Labeling and Scanning
实施规模
- Enterprise-wide Deployment
影响指标
- Productivity Improvements
- Cost Savings
- Customer Satisfaction
技术
- 功能应用 - 企业资源规划系统 (ERP)
- 功能应用 - 制造执行系统 (MES)
适用行业
- 汽车
适用功能
- 商业运营
- 仓库和库存管理
用例
- 库存管理
- 过程控制与优化
- 补货预测
服务
- 云规划/设计/实施服务
- 系统集成
关于客户
Spring Dynamics, Inc. is a manufacturer of springs primarily for the automotive industry. Headquartered in Almont, Michigan, the company also has a second facility in Harlingen, Texas. The company has been in the manufacturing industry for several years and is known for its high-quality spring products. Spring Dynamics serves a wide range of customers in the automotive sector, providing essential components that contribute to the functionality and safety of vehicles. The company is committed to innovation and efficiency, constantly seeking ways to improve its manufacturing processes and product offerings. With a focus on customer satisfaction and operational excellence, Spring Dynamics has established itself as a reliable partner in the automotive supply chain. The company employs a dedicated team of professionals who are skilled in various aspects of manufacturing and business operations, ensuring that Spring Dynamics remains competitive in the industry.
挑战
For several years, Spring Dynamics had been utilizing an on-premise ERP system that included accounting functions and standard reports on inventory, accounts receivable, and accounts payable. Management wanted a more robust, comprehensive system that would also include shop floor operations, generate management reports, and help maximize overall business performance. After one failed (and costly) attempt to launch a system it felt could meet these requirements, Spring Dynamics feared the disruption and capital investment involved in installing another solution. It approached a second review of potential solutions very cautiously. After a lengthy and intense analysis of possible solutions, management narrowed the search down to two candidates: Plex ERP and QAD. After reviewing demos, talking with existing customers of both products, and meeting with their development and management teams, Spring Dynamics selected Plex. The company preferred Plex to QAD for three reasons: Plex appeared to be a lot more user-friendly than QAD, there was less of an outlay of cash with Plex, and many of Spring Dynamics’ customers had been moving to the Plex Smart Manufacturing Platform, and management saw distinct advantages to using the same system its customers prefer.
解决方案
Plex ERP was launched in both of Spring Dynamics’ facilities simultaneously in just four months. Because Plex combines the capabilities of enterprise resource planning (ERP), manufacturing execution systems (MES), quality management, customer relationship management (CRM), and shop-floor integration, it has ideally served Spring Dynamics’ needs for an all-in-one, shop-floor-to-top-floor solution. It enables the company to more effectively and efficiently manage every aspect of its operations. Also, because it is a cloud-based model, Plex ERP is securely managed and maintained off-premises. Employees access data online and the company does not need to dedicate internal resources to managing the system. Today, employees are able to access and print real-time reports while filtering out data as needed. The integration of data and the use of common processes enable management to have a more accurate view of the operations in both of the company’s plants at all times. Accurate, comprehensive tracking of products as they are manufactured improves inventory management, traceability, and resource forecasting. Before launching Plex, Spring Dynamics needed to invest internal resources to track down missing products on a weekly basis. Now, the company uses barcode labeling and scanning processes to identify and track all products. Everything runs much more smoothly. Inventory is tracked at virtually 100 percent accuracy.
运营影响
数量效益
Case Study missing?
Start adding your own!
Register with your work email and create a new case study profile for your business.
相关案例.
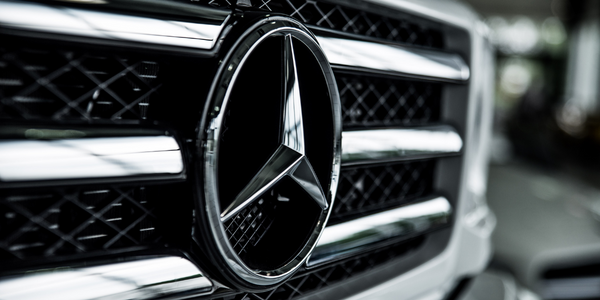
Case Study
Integral Plant Maintenance
Mercedes-Benz and his partner GAZ chose Siemens to be its maintenance partner at a new engine plant in Yaroslavl, Russia. The new plant offers a capacity to manufacture diesel engines for the Russian market, for locally produced Sprinter Classic. In addition to engines for the local market, the Yaroslavl plant will also produce spare parts. Mercedes-Benz Russia and his partner needed a service partner in order to ensure the operation of these lines in a maintenance partnership arrangement. The challenges included coordinating the entire maintenance management operation, in particular inspections, corrective and predictive maintenance activities, and the optimizing spare parts management. Siemens developed a customized maintenance solution that includes all electronic and mechanical maintenance activities (Integral Plant Maintenance).
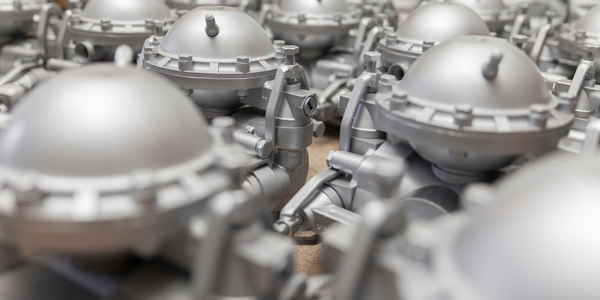
Case Study
Monitoring of Pressure Pumps in Automotive Industry
A large German/American producer of auto parts uses high-pressure pumps to deburr machined parts as a part of its production and quality check process. They decided to monitor these pumps to make sure they work properly and that they can see any indications leading to a potential failure before it affects their process.