公司规模
Large Corporate
地区
- Europe
国家
- Germany
产品
- Brocade NetIron CES 2000 Series switches
- Brocade NetIron CER 2000 Series routers
- Brocade MLXe Series routers
技术栈
- Multiprotocol Label Switching (MPLS)
- Voice over IP (VoIP)
- Access control systems
实施规模
- Enterprise-wide Deployment
影响指标
- Cost Savings
- Productivity Improvements
技术
- 网络与连接 - 以太网
- 网络与连接 - 网络管理和分析软件
适用行业
- 化学品
- 药品
适用功能
- 物流运输
- 设施管理
用例
- 校园网
- 能源管理系统
- 基础设施检查
服务
- 系统集成
- 云规划/设计/实施服务
关于客户
Infraserv GmbH & Co. Höchst KG (Infraserv Höchst) is the owner and operator of Industriepark Höchst, a prominent industrial park in Germany. The park, which celebrated its 150th anniversary, is a vital research and development site for over 90 companies from the pharmaceutical, chemical, biotechnology, and crop science industries. It houses more than 22,000 employees within a 460-hectare facility west of Frankfurt. Industriepark Höchst provides all of the services that research and production companies need—from raw materials and waste disposal to logistics and IT services—in an integrated end-to-end solution. Infraserv Höchst acts both as a site operator and provider, offering its own network to resident businesses at Industriepark Höchst.
挑战
Infraserv Höchst, the owner and operator of Industriepark Höchst, a large industrial park in Germany, faced the challenge of building a highly available, multitenant campus network capable of delivering essential services to tenants. The park is a vital research and development site for over 90 companies from the pharmaceutical, chemical, biotechnology, and crop science industries. The legacy IT environment of Infraserv Höchst was complex and cumbersome, consisting of 50 separate networks belonging to onsite customers and several Infraserv Höchst environments that provided telephony and data network management services. The company needed to invest in the modernization and standardization of its IT environment.
解决方案
Infraserv Höchst chose to deploy Brocade MLXe Core Routers and Brocade NetIron CES 2000 Series switches. The company built an MPLS network that provides Layer 2/3 functionality for Infraserv Höchst and its onsite customers. This enabled affordable pricing of essential services for onsite customers and helped ensure compliance with security requirements mandated by the pharmaceutical industry. The MPLS network allows Infraserv Höchst to offer differentiated services to customers simultaneously, so that these customers view the Layer 2 or Layer 3 networks as their own. The company also reduced energy consumption by approximately 25 to 30 percent with the Brocade environment.
运营影响
数量效益
Case Study missing?
Start adding your own!
Register with your work email and create a new case study profile for your business.
相关案例.
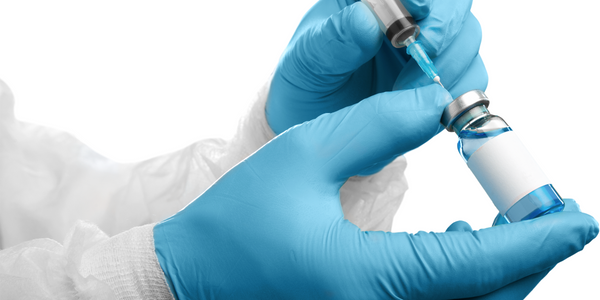
Case Study
Case Study: Pfizer
Pfizer’s high-performance computing software and systems for worldwide research and development support large-scale data analysis, research projects, clinical analytics, and modeling. Pfizer’s computing services are used across the spectrum of research and development efforts, from the deep biological understanding of disease to the design of safe, efficacious therapeutic agents.
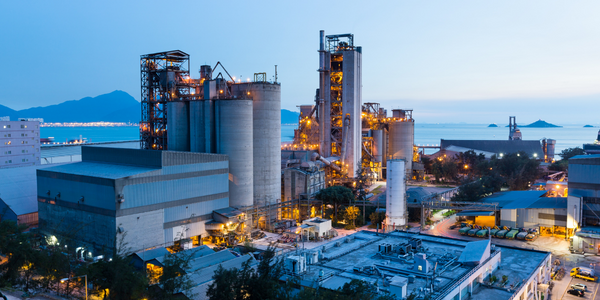
Case Study
Honeywell - Tata Chemicals Improves Data Accessibility with OneWireless
Tata was facing data accessibility challenges in the cement plant control room tapping signals from remote process control areas and other distant locations, including the gas scrubber. Tata needed a wireless solution to extend its control network securely to remote locations that would also provide seamless communication with existing control applications.

Case Study
Advanced Elastomer Systems Upgrades Production
In order to maintain its share of the international market for thermoplastic elastomers AES recently expanded its Florida plant by adding a new production line. While the existing lines were operating satisfactorily using a PROVOX distributed control system with traditional analog I/O, AES wanted advanced technology on the new line for greater economy, efficiency, and reliability. AES officials were anxious to get this line into production to meet incoming orders, but two hurricanes slowed construction.
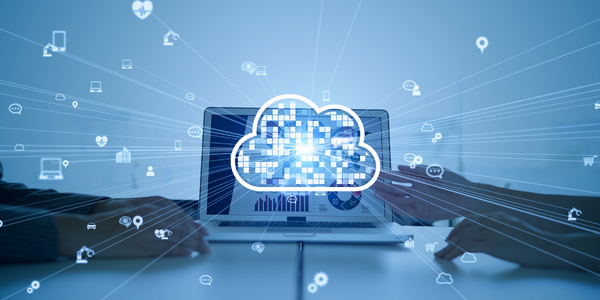
Case Study
Fusion Middleware Integration on Cloud for Pharma Major
Customer wanted a real-time, seamless, cloud based integration between the existing on premise and cloud based application using SOA technology on Oracle Fusion Middleware Platform, a Contingent Worker Solution to collect, track, manage and report information for on-boarding, maintenance and off-boarding of contingent workers using a streamlined and Integrated business process, and streamlining of integration to the back-end systems and multiple SaaS applications.
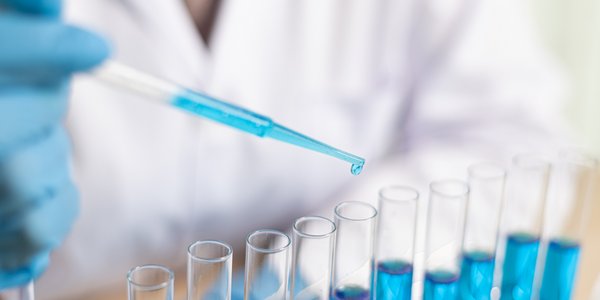
Case Study
Process Control System Support
In many automated production facilities, changes are made to SIMATIC PCS 7 projects on a daily basis, with individual processes often optimised by multiple workers due to shift changes. Documentation is key here, as this keeps workers informed about why a change was made. Furthermore, SIMATIC PCS 7 installations are generally used in locations where documentation is required for audits and certification. The ability to track changes between two software projects is not only an invaluable aid during shift changes, but also when searching for errors or optimising a PCS 7 installation. Every change made to the system is labour-intensive and time-consuming. Moreover, there is also the risk that errors may occur. If a change is saved in the project, then the old version is lost unless a backup copy was created in advance. If no backup was created, it will no longer be possible to return to the previous state if and when programming errors occur. Each backup denotes a version used by the SIMATIC PCS 7 system to operate an installation. To correctly interpret a version, information is required on WHO changed WHAT, WHERE, WHEN and WHY: - Who created the version/who is responsible for the version? - Who released the version? - What was changed in the version i.e. in which block or module of the SIMATIC PCS 7 installation were the changes made? - When was the version created? Is this the latest version or is there a more recent version? - Why were the changes made to the version? If they are part of a regular maintenance cycle, then is the aim to fix an error or to improve production processes? - Is this particular version also the version currently being used in production? The fact that SIMATIC PCS 7 projects use extremely large quantities of data complicates the situation even further, and it can take a long time to load and save information as a result. Without a sustainable strategy for operating a SIMATIC PCS 7 installation, searching for the right software version can become extremely time-consuming and the installation may run inefficiently as a result.