公司规模
Large Corporate
地区
- Asia
国家
- Japan
产品
- Google Cloud AI Infrastructure
- Google Kubernetes Engine (GKE)
- Google Cloud AI Hypercomputer
- Google Cloud's Tech Acceleration Program (TAP)
- Gemini Code Assist
技术栈
- Hybrid Cloud
- Microservices Architecture
- SCRUM Development Methodology
- Google Cloud VPC
- Google Cloud Build
实施规模
- Enterprise-wide Deployment
影响指标
- Productivity Improvements
- Cost Savings
- Innovation Output
技术
- 分析与建模 - 机器学习
- 平台即服务 (PaaS) - 数据管理平台
- 基础设施即服务 (IaaS) - 云计算
适用行业
- 汽车
适用功能
- 流程制造
- 质量保证
用例
- 预测性维护
- 机器状态监测
- 过程控制与优化
服务
- 云规划/设计/实施服务
- 系统集成
- 培训
关于客户
Toyota, a global leader in the automotive industry, is renowned for its innovative production system, the Toyota Production System, which emphasizes efficiency and quality. The company has been at the forefront of automotive manufacturing, setting the gold standard with principles like 'Jidoka' (automation with a human touch) and 'Just-in-Time' inventory management. Despite its success, Toyota recognized the need to adapt to the evolving landscape of the automotive industry, characterized by the rise of connected cars, autonomous driving, shared mobility, and electrification. To maintain its competitive edge, Toyota embarked on a digital transformation journey, focusing on integrating AI into its manufacturing processes. The company's Production Digital Transformation Office played a pivotal role in this initiative, aiming to democratize AI development and empower factory workers to create and deploy machine learning models. By leveraging AI, Toyota sought to enhance manufacturing efficiency, automate labor-intensive tasks, and improve overall productivity. The company's commitment to innovation and continuous improvement has positioned it as a leader in the automotive sector, driving advancements in manufacturing technology and setting new benchmarks for the industry.
挑战
The automotive industry is undergoing a significant transformation driven by the rise of connected cars, autonomous driving, shared mobility, and electrification. Manufacturers, including Toyota, face the challenge of increasing efficiency, automating manufacturing processes, and improving quality. Despite Toyota's renowned production system, certain parts of the system resist conventional automation. Additionally, Toyota faced a bottleneck in promoting AI due to a shortage of employees with AI expertise. To overcome these challenges, Toyota's Production Digital Transformation Office aimed to democratize AI development within its factories, enabling factory floor employees to create machine learning models easily. This initiative sought to automate manual, labor-intensive tasks, allowing human workers to focus on higher-value activities such as process optimization and data-driven decision-making.
解决方案
Toyota developed an AI Platform using Google Cloud's AI Infrastructure to empower factory workers to create and deploy machine learning models. The platform, built on a hybrid architecture combining on-premises infrastructure and cloud computing, facilitates agile development and resource optimization. By adopting a microservices-based architecture and agile methodologies like SCRUM, Toyota rapidly iterated and deployed new features while maintaining robust security. The hybrid cloud approach allowed Toyota to use on-premises resources during normal operations and scale to the cloud during peak demand, reducing GPU usage costs and optimizing performance. This approach also minimized the need for extensive on-premises hardware investments, aligning with Toyota's 'Just-in-Time' method. Toyota chose Google Cloud for its flexibility in using GPUs, ease of use, and speed of build and processing. Google Cloud's unique features, such as multi-instance GPUs and time-sharing GPUs, optimized costs and increased business value. The speed of communication and processing, facilitated by Google Kubernetes Engine (GKE), Autopilot, and Image Streaming, improved cost-effectiveness and operational efficiency. The collaboration with Google Cloud enabled Toyota to complete the large-scale development of the AI Platform in 1.5 years with a small team of six developers, significantly enhancing the development experience and user adoption.
运营影响
数量效益
Case Study missing?
Start adding your own!
Register with your work email and create a new case study profile for your business.
相关案例.
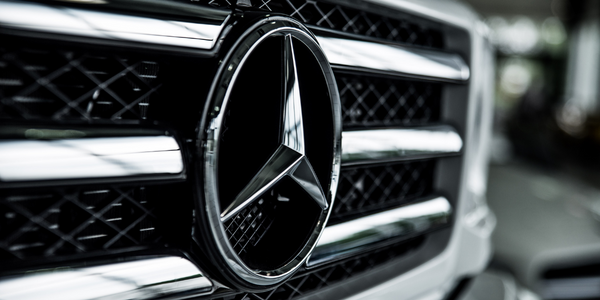
Case Study
Integral Plant Maintenance
Mercedes-Benz and his partner GAZ chose Siemens to be its maintenance partner at a new engine plant in Yaroslavl, Russia. The new plant offers a capacity to manufacture diesel engines for the Russian market, for locally produced Sprinter Classic. In addition to engines for the local market, the Yaroslavl plant will also produce spare parts. Mercedes-Benz Russia and his partner needed a service partner in order to ensure the operation of these lines in a maintenance partnership arrangement. The challenges included coordinating the entire maintenance management operation, in particular inspections, corrective and predictive maintenance activities, and the optimizing spare parts management. Siemens developed a customized maintenance solution that includes all electronic and mechanical maintenance activities (Integral Plant Maintenance).
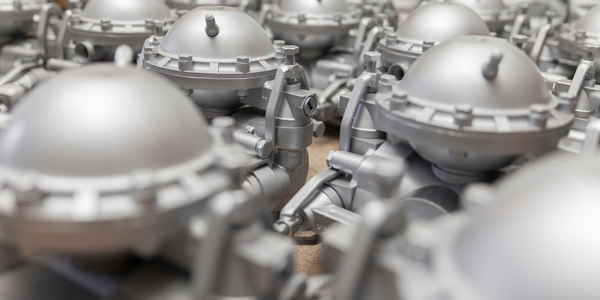
Case Study
Monitoring of Pressure Pumps in Automotive Industry
A large German/American producer of auto parts uses high-pressure pumps to deburr machined parts as a part of its production and quality check process. They decided to monitor these pumps to make sure they work properly and that they can see any indications leading to a potential failure before it affects their process.