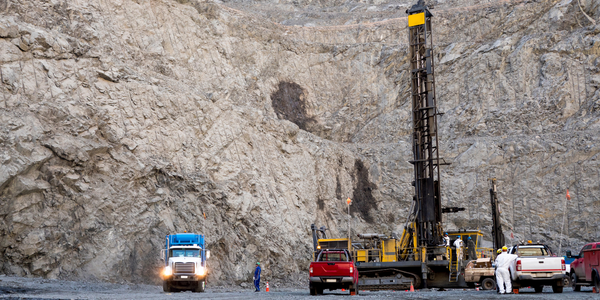
技术
- 功能应用 - 远程监控系统
- 可穿戴设备 - 补丁标签
适用功能
- 流程制造
用例
- 流程追踪
客户
肯纳金属
关于客户
Kennametal – 超过 75 年的工业技术领导者,帮助希望在苛刻环境中获得最佳性能的客户实现生产力提升。公司提供创新的耐磨产品、应用技术和服务
挑战
Kennametal 的高品质钻头及其相关的铝托盘在加工完成后经过彻底的清洁过程,包括超声波、湿法和真空清洁过程。在进入这个清洗设施之前,订单文件和托盘是分开的,然后在清洗后重新分配。一个涉及风险的工作步骤,分析表明,有时托盘和订单文件在清洁后分配不正确。钻头经过了本应用于不同订单的涂层工艺。因此,有必要完全消除混淆。
解决方案
解决方案以 Structobond® 的形式出现,这种塑料标签永久地封闭在环氧树脂粘合剂中,能够承受甚至复杂的清洁过程。当从托盘库存中取出托盘以填充订单空白时,将来会从其 Structobond® 标签上扫描条形码。在车站,条形码和全文复制在标准的不干胶标签上,并粘贴在订单文件上。现在,托盘和订单文件在生产的所有阶段都“结合”了,包括清洗过程,确保在任何时候都没有错误的分配。
运营影响
Case Study missing?
Start adding your own!
Register with your work email and create a new case study profile for your business.
相关案例.
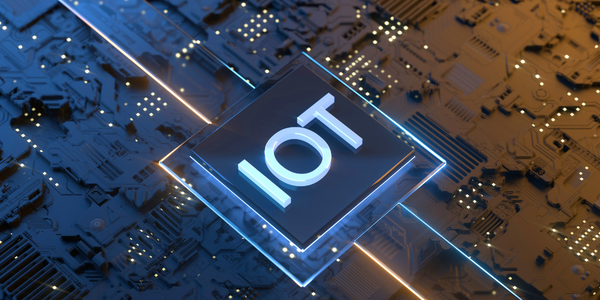
Case Study
IoT Gateway Enables Faurecia to Improve Traceability for Customers
While Faurecia has a long track record of providing its customers with exemplary products, the increasing need to provide customers traceability for the parts it was producing motivated the company to further support these efforts. The large automotive OEMs expected Faurecia to be able to both track the process of operations and production and to make that information available on demand. For example, customers wanted to know which airbags were added to which cars, as well as detailed data characteristics about how each airbag was installed, including torque and angle of installation.
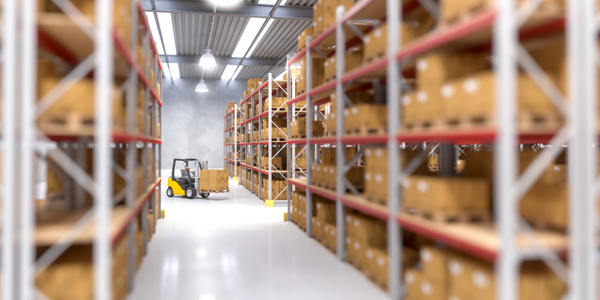
Case Study
Fully Automated Identification for Alping Italia
Full material traceability ensures process reliability in production and it is a major building block for the economic success of manufacturing companies. To optimise production management, automated identification systems with tags which have barcodes printed on them are now increasingly used in production facilities and warehouses. This ensures full control from the receipt of raw materials to the finishing of the products and shipping.The steel industry in particular, is a difficult environment and the labels and tags that ensure full material traceability have to withstand extreme conditions. Raw materials and products have rough surfaces. In addition, the data carriers are exposed to enormous heat and heavy soiling. And last but not least, the whole identification process always has to be carried out under time pressure.
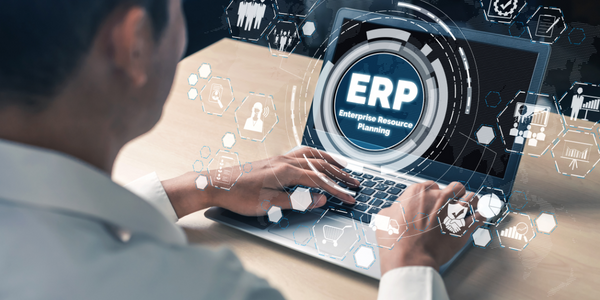
Case Study
Tripling Sales with Deacom ERP: A Case Study on Copps Industries
Since 1979, Copps Industries has been a global provider of epoxy resins to various markets. However, the company faced challenges in scaling to meet market demand due to outdated technology and manual workarounds to fill in process gaps. The company relied heavily on people to deliver scalable and repeatable processes, which limited the volume of SKUs manageable by their small team. Copps was also burdened with an outdated disk-operating system (DOS) that no longer supported its business needs, and employees struggled with managing a paper trail of documents. The retirement of two 20+ year veterans further complicated matters, leading to issues with process control and onboarding new employees. Copps Industries needed a solution that would tighten process control, scale with its business, and centralize information for easy access.
Case Study
Advantech Industry 4.0 Solutions, Excellence in Pharmaceutical Manufacturing
União Química, one of the biggest players in Brazil’s burgeoning pharmaceutical industry, was being held back by its reliance on outdated production methods. The firm’s managers found their production lines hampered by a low productivity and a lack of efficient quality monitoring, as well as a lack of remote connectivity enabling easy access to critical production line data. One key distinguishing feature in drug manufacturing is the necessity of carefully documenting each step of the production process for compliance. These strict requirements led pharmaceutical manufacturers to store production information in paper records for future reference, but this approach also made it difficult for production managers to make process improvements.
Case Study
Mirriad Delivers Next-Generation Ad Tech Using AWS
Mirriad, a London-based company, delivers next-generation advertising solutions by using its computer vision technology to naturally place brands in premium video content across TV, online, and mobile channels. The challenge for Mirriad was achieving this intelligent insertion of ads at scale. The company was initially using physical data centers, which proved to be a bottleneck when it came to onboarding big businesses. In addition to fast access to compute capacity, another vital requirement for the company was the ability to use NVIDIA GPUs across multiple regions worldwide.
Case Study
Integratis Enhances Decision-Making with Alteryx Analytic Process Automation Platform
UK-based consultancy Integratis, which provides tailored solutions in strategy development and business planning to private, public, and third sector clients, was facing challenges in optimizing data in the highly scrutinized environments of public and third sector organizations. The company was growing rapidly and needed to strengthen and differentiate their customer offerings while maintaining their core value of data-led decision making. As the business grew, so did the need for integration with multiple systems and applications. The team at Integratis was becoming increasingly frustrated with the limited capabilities of Microsoft Access and Excel, and the lack of consistency this offered when collaborating across teams. They needed a system that would allow them to collaborate effectively with full traceability at every step, especially in the public sector where transparency is crucial due to stringent and often unpredictable auditing demands.