制造系统自动化
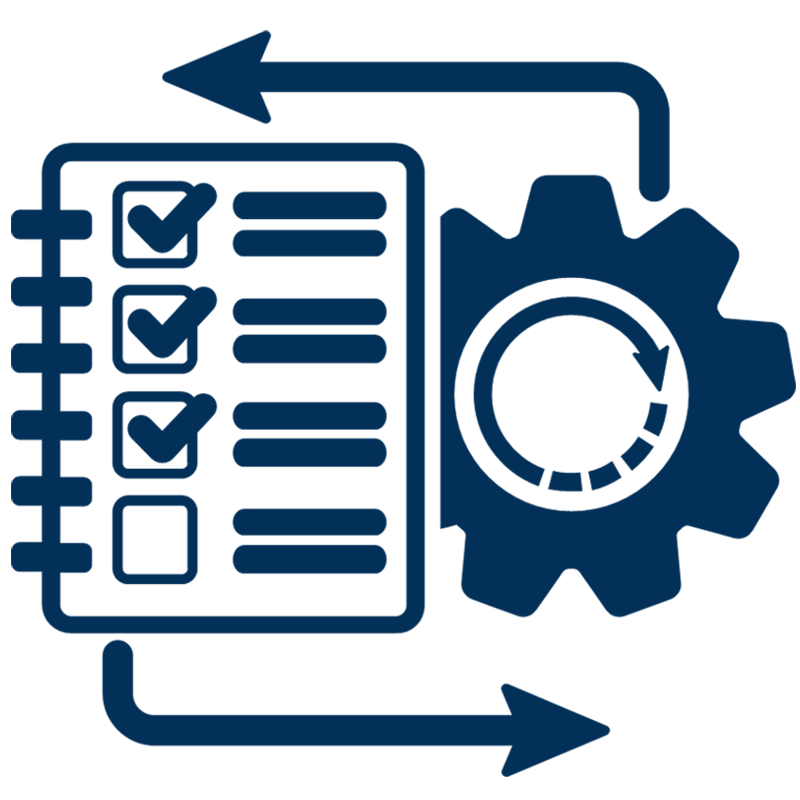
概述
制造系统自动化集成了软件和机械,使制造过程通过计算机编程自主运行。制造系统自动化的目标是最大限度地减少制造过程中所需的人工协助。这些系统提供恒定的反馈回路并根据安装在机器上的 PLC 和智能传感器的反馈调整控制参数。传感器通常嵌入在新设备中,也可以安装在旧设备上。自动化已经通过各种方式实现,包括机械、液压、气动、电气、电子设备和计算机,通常是结合使用。自动化的好处包括降低与劳动力、电力、水、天然气和废料相关的成本,以及提高质量、准确性和精度。制造系统自动化还可以减少转换时间,从而实现小批量生产和大规模定制。
适用行业
- 汽车
- 设备与机械
适用功能
- 离散制造
- 产品开发
- 质量保证
市场规模
商业观点
自动化制造系统如何提供商业价值?
● 员工更安全
● 提高生产力(24/7 运行时间)
● 提高产品质量
● 更高的收益
● 更准确的数据采集
自动化工业系统不仅提高了生产能力,而且提高了生产质量,同时提高了操作设备的员工的安全性。这些系统还可以配置为提供更准确的数据,以优化薄弱环节并大大减少人为错误导致的产品缺陷。
微电网有什么好处?
为电网的最终用户和运营商提供电能质量、可靠性和安全性
加强分布式能源和可再生能源的整合
具有成本竞争力和效率
实现智能电网技术集成
本地控制的电能质量
通过最大限度地利用当地清洁能源发电,最大限度地减少碳足迹和温室气体排放
增加客户(最终用户)参与度
技术观点
制造技术的最新趋势是什么?
新的制造技术不断涌现。近年来的一些最大趋势包括:
- 3D 打印:几乎可以使用金属、塑料和其他材料制造任何组件,缩短交货时间并简化从设计到生产的流程
- 云服务:从任何位置快速有效地实现数据和服务的虚拟共享
- 物联网 (IoT):不仅改变消费市场,还改变制造过程中使用的电子设备的维护和保养
- 纳米技术:实现更快的计算机处理、更长的产品生命周期和超精密制造,以及空间工程和生物技术等领域的开创性进步
- 先进的数据分析和预测技术:在制造过程中实现更好的过程控制、缺陷预防和更快的响应时间
- 工业机器人:通过自动化困难或单调的任务,提供提高生产力、提高质量和降低成本的方法。
部署挑战
制造系统自动化面临的最大挑战是什么?
● 初始投资成本
实施自动化制造系统只有一个真正的缺点,那就是初始成本。这包括机器成本和实施自动化编程以及培训员工以管理这些新系统。然而,这项投资的投资回报率通常会在几年内收回成本。
案例研究.

Case Study
Driving Digital Transformation: Lordan
Lordan needed a manufacturing automation system that could identify bottlenecks, reduce downtime and waste, and improve overall equipment effectiveness (OEE). Requirements included the ability to view overall throughput and track mission-critical manufacturing information in real time directly from the production floor, rather than rely on periodical assessments.
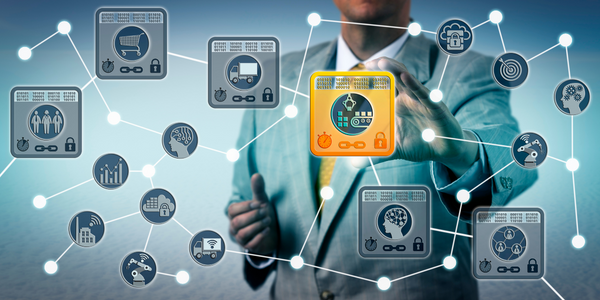
Case Study
Covisint Improves Mitsubishi's Collaboration With Its Supply Chain
Mitsubishi sought to improve supplier relationships on a global basis and to offer an easy-to-use solution to interact with them. In August 2004, Mitsubishi selected Covisint’s platform to help improve sharing of information and collaborative business processes with its global suppliers. Covisint enabled Mitsubishi to provide its suppliers with immediate access to information and applications to obtain more collaborative working relationships
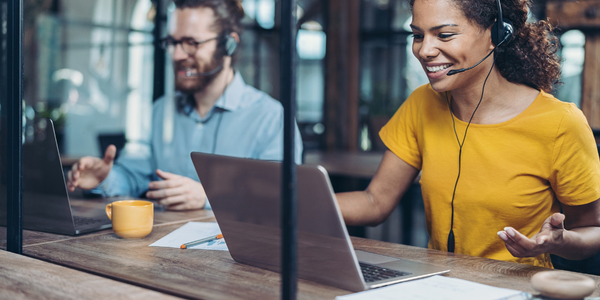
Case Study
Enables 1st Class Customer Service
Applied Automation needed an efficient yet effective way to do customer services without sending the engineers to all parts of the world.Ongoing customer support is provided by the company’s engineers based on the south west coast of England. They need a remote access solutions which allow them to do customer service in England.