过程控制与优化
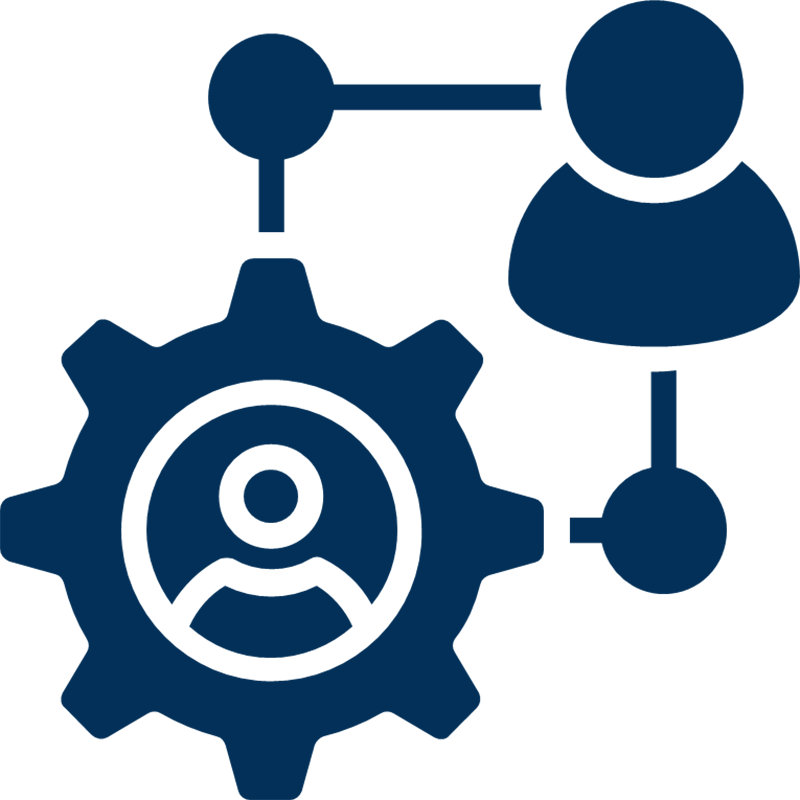
概述
过程控制和优化 (PCO) 是在不违反过程约束的情况下调整过程以维持或优化一组指定参数的学科。 PCO 市场受到对节能生产流程、安全和安保问题的需求不断增长以及能够可靠预测流程偏差的物联网系统开发的推动。从根本上说,可以调整三个参数以影响最佳性能。 - 设备优化:第一步是通过检查运行数据以识别设备瓶颈来验证现有设备是否被充分利用。 - 操作程序:操作程序可能因人而异或因班次而异。工厂的自动化可以提供很大帮助。但是,如果操作员控制并手动运行工厂,自动化将无济于事。 - 控制优化:在典型的加工厂,例如化工厂或炼油厂,有数百甚至数千个控制回路。每个控制回路负责控制过程的一部分,例如保持温度、液位或流量。如果控制回路没有正确设计和调整,则过程会低于其最佳值。该过程的操作成本将更高,并且设备会过早磨损。为了使每个控制回路以最佳方式运行,识别传感器、阀门和调整问题很重要。已充分证明超过 35% 的控制回路通常存在问题。持续监控和优化整个工厂的过程有时称为绩效监督。
适用行业
- 运输
- 设备与机械
- 化学品
适用功能
- 离散制造
- 质量保证
市场规模
案例研究.
.png)
Case Study
Intelligence for Digital Oilfield (WellAware)
WellAware was exploring the market for a reliable solution for collecting data from its customers’ remote well locations. According to WellAware CEO, Matt Harrison, the company’s customers have a tremendous need to tap into the intelligence provided by the digital oilfield. In selecting a provider for its network, WellAware compared the features of an array of communication technologies. Cellular provided adequate coverage, but at the rate of $25-$50 per month per device, the cost was extremely high. Satellite was even more expensive, in excess of $100 per month per device. As a typical oilfield consists of more than 1,000 wells, implementation of these technologies would quickly become cost-prohibitive. Additionally, cellular and satellite technologies were only able to deliver between 85-95 percent data availability and were not able to transmit data at sub-minute frequencies. This was not sufficient to meet the reliability expectations of WellAware’s customers.
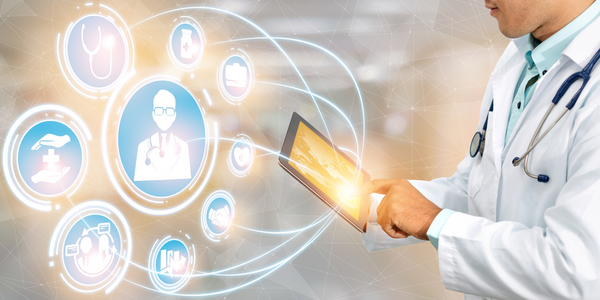
Case Study
Improve the Efficiency and Safety of Liposuction with Data Analysis
Liposuction is a surgery that removes fat from the human body with cannula, a tube that can be inserted into the body. Extracting fat is a very complex surgery procedure. The cannula should precisely reach to the fatty tissue between skin and muscles. When the cannula is injected into deeper issue, it may damage muscle issue. If the cannula isn’t inserted enough, the fat maybe removed unevenly or causes skin necrosis. The fine senses of surgeon is certainly important.Injecting cannula and extracting fat occur 12,000 to 20,000 times per one surgery. It means that moving cannula in time-uniformly is critical. However, every patients has different types of fatty tissue and areas operated on. Due to this complexity of the procedure, skillful surgeon having plenty of experiences were favoured.
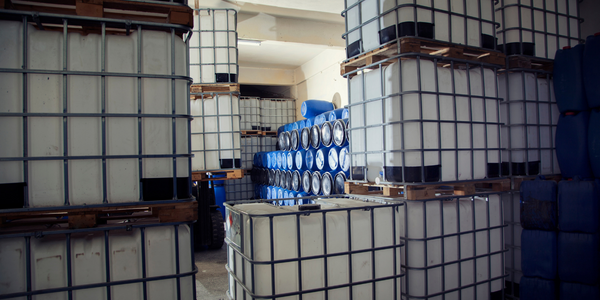
Case Study
New GHS Regulations Require New Identification Concepts
With the GHS regulations (GHS - Globally Harmonized System) the United Nations wanted to minimise the risks to human health and the environment arising from production, transport and the use of hazardous substances. Standardised danger symbols and texts now have to be used for the identification of chemicals around the world. 1200 quality products not only need to be produced, they also need to be stored and shipped in a professional manner. In April 2014, a dedicated team was set up to manage the changeover to the new GHS regulations under the umbrella of the PETROFER CHEMIE ICT (Information & Communication Technology) department. It was chaired by Roland Günther and Jonas Hartmann. They subjected the existing logistics and identification processes to some rigorous tests. They analysed and conceptualised.