A North American Energy Company Leverages the Denodo Platform in the Microsoft Azure Cloud to Modernize Its Data Infrastructure
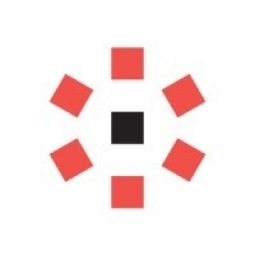
公司规模
Large Corporate
地区
- America
国家
- United States
- Australia
- Canada
产品
- Denodo Platform
- Microsoft Azure
技术栈
- Data Virtualization
- Cloud Computing
实施规模
- Enterprise-wide Deployment
影响指标
- Cost Savings
- Productivity Improvements
- Digital Expertise
技术
- 基础设施即服务 (IaaS) - 云计算
- 平台即服务 (PaaS) - 数据管理平台
适用功能
- 商业运营
- 物流运输
用例
- 能源管理系统
- 预测性维护
- 监管合规监控
服务
- 云规划/设计/实施服务
- 数据科学服务
关于客户
This company is one of North America’s largest energy companies. It operates more than 70 power plants in United States, Canada, and Australia. The company operates wind, hydro, natural gas, and coal power generation facilities and is one of North America’s largest investor owned renewable energy providers. This energy company provides safe, reliable, and affordable power to millions of users. To do this on an everyday basis, the company needs to be able to effectively manage large volumes of critical, often highly dynamic data, while also reporting on its use of this data, to satisfy regulatory requirements. Because the company sells energy on the open market, the company must demonstrate that it does not engage in insider trading. Hence, it is exceptionally critical that only people with the proper authority can access specific data and that all such usage is carefully tracked.
挑战
The company recently decided to migrate its on-premises data infrastructure to the cloud to enable a wider variety of more powerful, cloud-enabled applications while taking advantage of its flexibility, agility, and reduced TCO. However, in doing so, the business intelligence consultant at the company knew that the company would face several predictable challenges: Not all of the company's applications could be simply ported to the cloud, as some rely on authentication procedures that may have been developed for the on-premises environment. Also, because some data centers are farther away than others, geographically, they could introduce unexpected latency into the migration process. Besides, the company needed to move and transform terabytes of data, and the company's extract, transform, and load (ETL) processes would take a prohibitively long time to run. The energy company wanted the flexibility to change application providers during the migration, while also migrating to the cloud in a phased, controlled manner, due to the complexity of some of its applications. The company needed a way to accelerate the migration process while also gaining the flexibility to migrate at its own pace and make changes during the migration without impacting users.
解决方案
After a diligent evaluation process, the company implemented the Denodo Platform, which uses data virtualization to establish a unified data access layer above the company's on-premises and cloud sources. In this way, the Denodo Platform abstracts users from the complexities of accessing the different sources, even when they change. Rather than physically moving the data from each source to a new repository in the company's cloud, the Denodo Platform provides real-time, integrated views of the data across the various data sources, regardless of whether they are on-premises or in the cloud. The company implemented the Denodo Platform on its Microsoft Azure instance, where all of its data infrastructures were targeted to move. The company positioned the Denodo Platform so as to readily connect to data from the company's cloud-based Active Directory instances, real-time sensor data, and other sources, to enable a series of new cloud-based applications, including a virtual data mart for energy traders, an application to predict icing events, and an HR dashboard.
运营影响
数量效益
Case Study missing?
Start adding your own!
Register with your work email and create a new case study profile for your business.
相关案例.

Case Study
Remote Monitoring & Predictive Maintenance App for a Solar Energy System
The maintenance & tracking of various modules was an overhead for the customer due to the huge labor costs involved. Being an advanced solar solutions provider, they wanted to ensure early detection of issues and provide the best-in-class customer experience. Hence they wanted to automate the whole process.
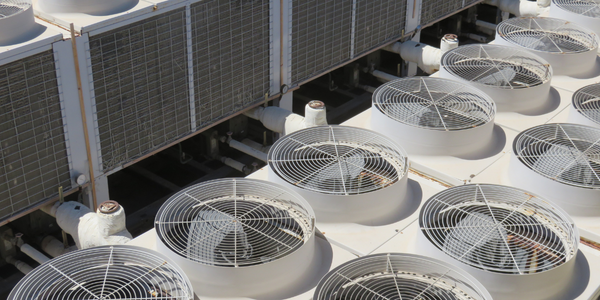
Case Study
Predictive Maintenance for Industrial Chillers
For global leaders in the industrial chiller manufacturing, reliability of the entire production process is of the utmost importance. Chillers are refrigeration systems that produce ice water to provide cooling for a process or industrial application. One of those leaders sought a way to respond to asset performance issues, even before they occur. The intelligence to guarantee maximum reliability of cooling devices is embedded (pre-alarming). A pre-alarming phase means that the cooling device still works, but symptoms may appear, telling manufacturers that a failure is likely to occur in the near future. Chillers who are not internet connected at that moment, provide little insight in this pre-alarming phase.
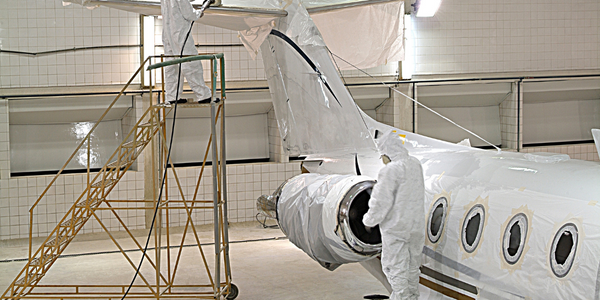
Case Study
Aircraft Predictive Maintenance and Workflow Optimization
First, aircraft manufacturer have trouble monitoring the health of aircraft systems with health prognostics and deliver predictive maintenance insights. Second, aircraft manufacturer wants a solution that can provide an in-context advisory and align job assignments to match technician experience and expertise.
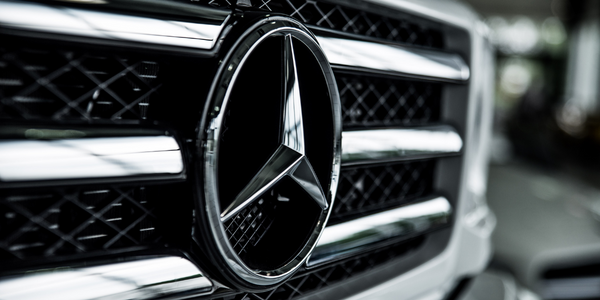
Case Study
Integral Plant Maintenance
Mercedes-Benz and his partner GAZ chose Siemens to be its maintenance partner at a new engine plant in Yaroslavl, Russia. The new plant offers a capacity to manufacture diesel engines for the Russian market, for locally produced Sprinter Classic. In addition to engines for the local market, the Yaroslavl plant will also produce spare parts. Mercedes-Benz Russia and his partner needed a service partner in order to ensure the operation of these lines in a maintenance partnership arrangement. The challenges included coordinating the entire maintenance management operation, in particular inspections, corrective and predictive maintenance activities, and the optimizing spare parts management. Siemens developed a customized maintenance solution that includes all electronic and mechanical maintenance activities (Integral Plant Maintenance).
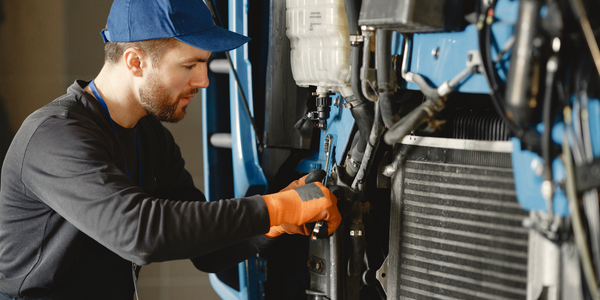
Case Study
Asset Management and Predictive Maintenance
The customer prides itself on excellent engineering and customer centric philosophy, allowing its customer’s minds to be at ease and not worry about machine failure. They can easily deliver the excellent maintenance services to their customers, but there are some processes that can be automated to deliver less downtime for the customer and more efficient maintenance schedules.