公司规模
Large Corporate
地区
- America
国家
- United States
产品
- DolphinRTK® software
- Sphera Product Stewardship Solution
技术栈
- Web-based application
实施规模
- Enterprise-wide Deployment
影响指标
- Productivity Improvements
- Cost Savings
- Brand Awareness
技术
- 功能应用 - 企业资源规划系统 (ERP)
适用行业
- 航天
- 国家安全与国防
适用功能
- 离散制造
- 质量保证
用例
- 监管合规监控
服务
- 系统集成
- 软件设计与工程服务
关于客户
Enginetics Aerospace Corporation is a leading provider of complex metal formed components and fabricated assemblies for the global aerospace industry. Founded in 1976, the Ohio-based company began as a small manufacturer of prototype parts. Today, it partners with the US Department of Defense as well as commercial jet builders and military customers in other countries to deliver innovative design and engineering that result in superior quality at lower costs. As its international business expanded, Enginetics decided to seek ISO 14001 certification, a framework that companies can follow to assure management, employees and other stakeholders that environmental impacts are being measured and improved. The company is also committed to ensuring compliance with other global mandates for product stewardship and sustainability, including Tier II chemical inventory reporting under the US Emergency Planning and Community Right-to-Know Act (EPCRA), the Globally Harmonized System for Classification and Labelling of Chemicals (GHS), and the European Union’s Registration, Evaluation, Authorization and Restriction of Chemicals (REACH).
挑战
Enginetics Aerospace Corporation, a leading provider of complex metal formed components and fabricated assemblies for the global aerospace industry, was seeking ISO 14001 certification. ISO 14001 is a framework that companies can follow to assure management, employees and other stakeholders that environmental impacts are being measured and improved. The certification would not only boost the company's reputation but also lower operating costs. However, the process of achieving this certification was challenging due to the need for accurate, timely Safety Data Sheets (SDS) information. Enginetics was already committed to ensuring compliance with other global mandates for product stewardship and sustainability, including Tier II chemical inventory reporting under the US Emergency Planning and Community Right-to-Know Act (EPCRA), the Globally Harmonized System for Classification and Labelling of Chemicals (GHS), and the European Union’s Registration, Evaluation, Authorization and Restriction of Chemicals (REACH). However, managing these compliance mandates manually was proving to be inefficient and prone to errors.
解决方案
To facilitate compliance with these mandates, Enginetics had recently automated management of Safety Data Sheets (SDSs) throughout its operations. It stopped relying on hazard communication information in paper-based SDSs that had to be managed manually in order to streamline its compliance work processes and reduce the likelihood of critical material safety data being inaccessible, in error or out of date. In 2004, Enginetics selected Sphera’s DolphinRTK® software – available on-demand as a Web-based application – part of the Sphera Product Stewardship Solution. The software enabled the Enginetics team to quickly and easily identify SDSs and analyze potential safety and/or environmental impacts in order to meet the ISO certification requirements. The Sphera system also helped the company determine what materials they can and cannot use in their customers’ products, providing accurate, timely data to make informed strategic decisions about product design and development.
运营影响
数量效益
Case Study missing?
Start adding your own!
Register with your work email and create a new case study profile for your business.
相关案例.
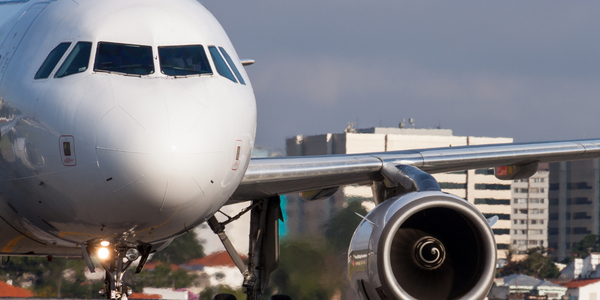
Case Study
Airbus Soars with Wearable Technology
Building an Airbus aircraft involves complex manufacturing processes consisting of thousands of moving parts. Speed and accuracy are critical to business and competitive advantage. Improvements in both would have high impact on Airbus’ bottom line. Airbus wanted to help operators reduce the complexity of assembling cabin seats and decrease the time required to complete this task.
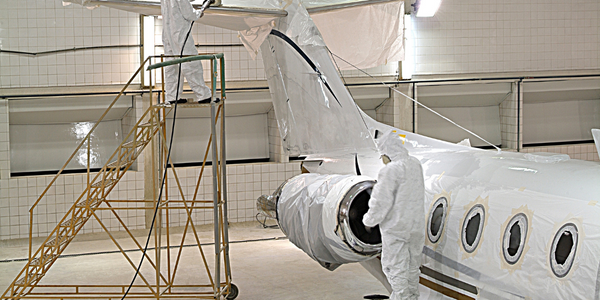
Case Study
Aircraft Predictive Maintenance and Workflow Optimization
First, aircraft manufacturer have trouble monitoring the health of aircraft systems with health prognostics and deliver predictive maintenance insights. Second, aircraft manufacturer wants a solution that can provide an in-context advisory and align job assignments to match technician experience and expertise.
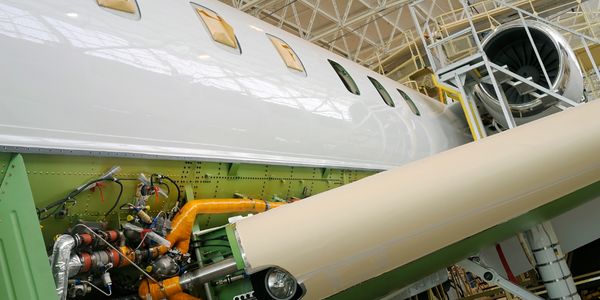
Case Study
Aerospace & Defense Case Study Airbus
For the development of its new wide-body aircraft, Airbus needed to ensure quality and consistency across all internal and external stakeholders. Airbus had many challenges including a very aggressive development schedule and the need to ramp up production quickly to satisfy their delivery commitments. The lack of communication extended design time and introduced errors that drove up costs.
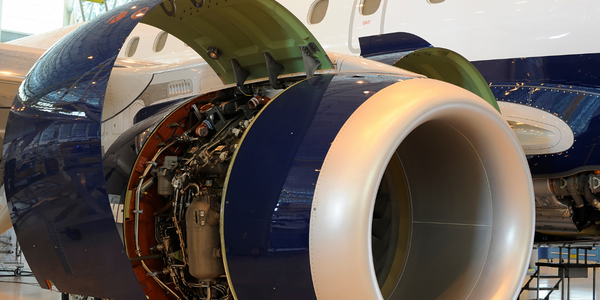
Case Study
Accelerate Production for Spirit AeroSystems
The manufacture and assembly of massive fuselage assemblies and other large structures generates a river of data. In fact, the bill of materials for a single fuselage alone can be millions of rows of data. In-house production processes and testing, as well as other manufacturers and customers created data flows that overwhelmed previous processes and information systems. Spirit’s customer base had grown substantially since their 2005 divestiture from Boeing, resulting in a $41 billion backlog of orders to fill. To address this backlog, meet increased customer demands and minimize additional capital investment, the company needed a way to improve throughput in the existing operational footprint. Spirit had a requirement from customers to increase fuselage production by 30%. To accomplish this goal, Spirit needed real-time information on its value chain and workflow. However, the two terabytes of data being pulled from their SAP ECC was unmanageable and overloaded their business warehouse. It had become time-consuming and difficult to pull aggregate data, disaggregate it for the needed information and then reassemble to create a report. During the 6-8 hours it took to build a report, another work shift (they run three per day) would have already taken place, thus the report content was out-of-date before it was ever delivered. As a result, supervisors often had to rely on manual efforts to provide charts, reports and analysis.
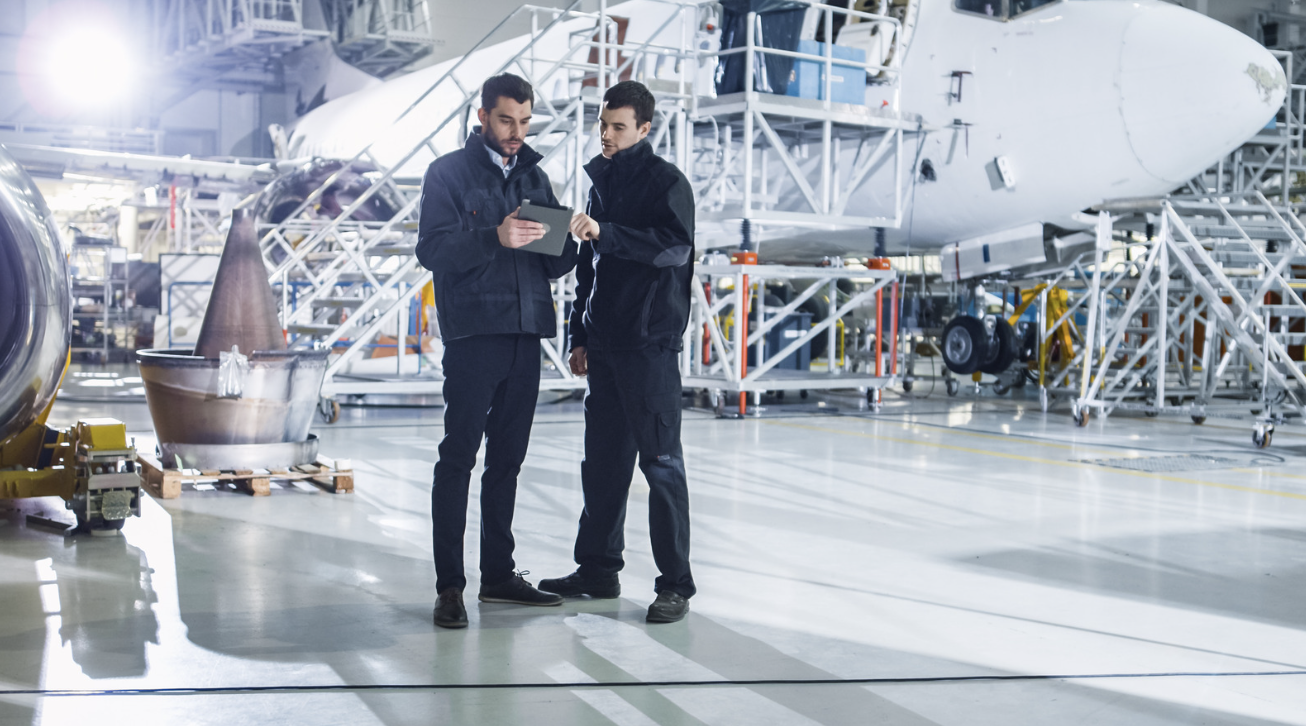
Case Study
Developing Smart Tools for the Airbus Factory
Manufacturing and assembly of aircraft, which involves tens of thousands of steps that must be followed by the operators, and a single mistake in the process could cost hundreds of thousands of dollars to fix, makes the room for error very small.