公司规模
Large Corporate
地区
- America
国家
- United States
产品
- Denodo Platform
- Layer7
- TIBCO Spotfire BI
技术栈
- Cloud Computing
- Data Virtualization
- Predictive Analytics
实施规模
- Enterprise-wide Deployment
影响指标
- Customer Satisfaction
- Productivity Improvements
技术
- 基础设施即服务 (IaaS) - 云计算
- 分析与建模 - 预测分析
适用功能
- 商业运营
用例
- 预测性维护
- 网络安全
服务
- 云规划/设计/实施服务
- 数据科学服务
关于客户
Asurion is a privately held company based in Nashville, Tennessee that provides device protection and support services for smartphones, tablets, consumer electronics, appliances, and satellite receivers. The company operates in 18 countries with 49 offices worldwide, serves 290 million consumers with 17,000 employees, and recorded more than $5.8B revenue in 2016. Asurion partners with the world’s leading telecommunications and cable service providers. Asurion’s biggest value proposition is its ability to deliver a high-quality customer experience. As Asurion expanded its operations globally, the company partnered with many telecommunications service providers of various sizes and scales of operation, and Asurion’s global client base expected an even higher quality customer experience. At the same time, Asurion started to provide premium support service, which extended beyond offering insurance and warranties to help customers manage their digital home experiences with premium support.
挑战
Asurion's new digital home premium support service required strong predictive analytics, IoT capabilities, and big data architecture support, to be able to provide customers with the right experience. But Asurion's on-premises legacy data architecture could not support its global expansion or premium support service. To exceed customer expectations, Asurion needed a next-generation data architecture that could enable the company to spin up additional infrastructure, services, and products in weeks instead of months. Asurion also faced strict restrictions on migrating data, and had to remain compliant with stringent governmental regulations. As a part of this effort, Asurion needed to centralize companywide security management around a single point of control.
解决方案
Two central technologies that Asurion embraced towards their gen 2.0 data architecture were cloud and data virtualization. Asurion moved to the cloud to be more agile, flexible, cost efficient and to support their international expansion. At the same time Asurion needed to secure their cloud, conform to contractual client specific, regional and departmental data rules and needed proper access control to ensure data integrity and data protection. Asurion created a three-tier architecture with the Denodo Platform providing data virtualization both on-premises and in the cloud, as well as a consuming layer that contained Layer7, a security and management solution, and TIBCO Spotfire BI. The Denodo Platform established a hybrid data layer that abstracted data consumers from the complexities of access across on-premises and cloud sources while also providing better data integration for improved analytics. Because of Asurion's stringent security requirements, Asurion needed to keep the two types of sources physically separate, but logically connected, indefinitely. The Denodo Platform can run either on-premises or in the cloud, so Asurion deployed a Denodo instance in both infrastructures, with a bridge between the two, which formed a hybrid data layer that establishes a single access point to the on-premises sources, in keeping with the company's security requirements.
运营影响
Case Study missing?
Start adding your own!
Register with your work email and create a new case study profile for your business.
相关案例.

Case Study
Remote Monitoring & Predictive Maintenance App for a Solar Energy System
The maintenance & tracking of various modules was an overhead for the customer due to the huge labor costs involved. Being an advanced solar solutions provider, they wanted to ensure early detection of issues and provide the best-in-class customer experience. Hence they wanted to automate the whole process.
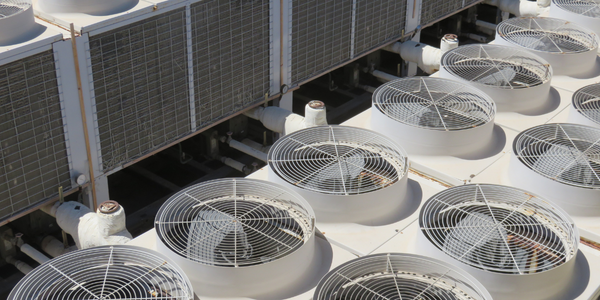
Case Study
Predictive Maintenance for Industrial Chillers
For global leaders in the industrial chiller manufacturing, reliability of the entire production process is of the utmost importance. Chillers are refrigeration systems that produce ice water to provide cooling for a process or industrial application. One of those leaders sought a way to respond to asset performance issues, even before they occur. The intelligence to guarantee maximum reliability of cooling devices is embedded (pre-alarming). A pre-alarming phase means that the cooling device still works, but symptoms may appear, telling manufacturers that a failure is likely to occur in the near future. Chillers who are not internet connected at that moment, provide little insight in this pre-alarming phase.
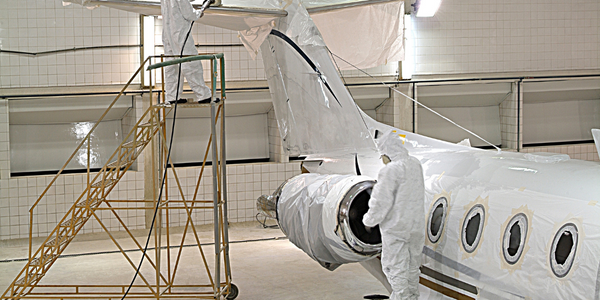
Case Study
Aircraft Predictive Maintenance and Workflow Optimization
First, aircraft manufacturer have trouble monitoring the health of aircraft systems with health prognostics and deliver predictive maintenance insights. Second, aircraft manufacturer wants a solution that can provide an in-context advisory and align job assignments to match technician experience and expertise.
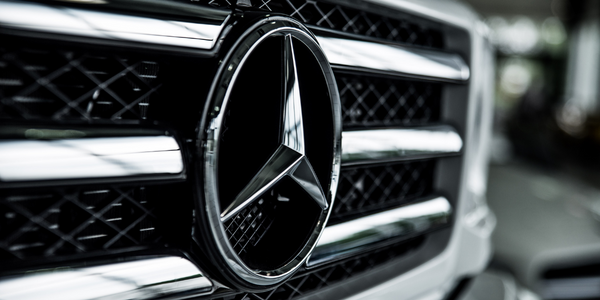
Case Study
Integral Plant Maintenance
Mercedes-Benz and his partner GAZ chose Siemens to be its maintenance partner at a new engine plant in Yaroslavl, Russia. The new plant offers a capacity to manufacture diesel engines for the Russian market, for locally produced Sprinter Classic. In addition to engines for the local market, the Yaroslavl plant will also produce spare parts. Mercedes-Benz Russia and his partner needed a service partner in order to ensure the operation of these lines in a maintenance partnership arrangement. The challenges included coordinating the entire maintenance management operation, in particular inspections, corrective and predictive maintenance activities, and the optimizing spare parts management. Siemens developed a customized maintenance solution that includes all electronic and mechanical maintenance activities (Integral Plant Maintenance).
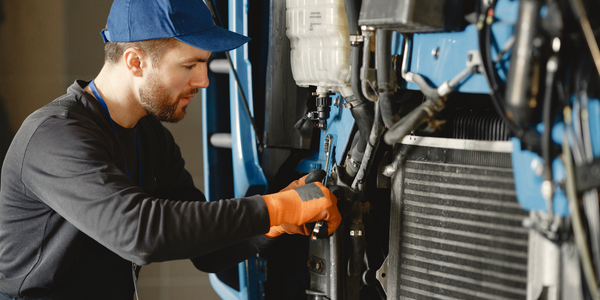
Case Study
Asset Management and Predictive Maintenance
The customer prides itself on excellent engineering and customer centric philosophy, allowing its customer’s minds to be at ease and not worry about machine failure. They can easily deliver the excellent maintenance services to their customers, but there are some processes that can be automated to deliver less downtime for the customer and more efficient maintenance schedules.