公司规模
Large Corporate
地区
- America
国家
- United States
- Canada
产品
- webMethods Business Process Management Suite
- webMethods Integration Server
- webMethods Broker
- webMethods Optimize for Process
技术栈
- Business Process Management
- Integration Server
- Broker
- Optimize for Process
实施规模
- Enterprise-wide Deployment
影响指标
- Productivity Improvements
- Cost Savings
技术
- 应用基础设施与中间件 - API 集成与管理
- 应用基础设施与中间件 - 数据交换与集成
适用行业
- 食品与饮料
适用功能
- 离散制造
- 维护
用例
- 预测性维护
- 资产健康管理 (AHM)
服务
- 系统集成
- 软件设计与工程服务
关于客户
Coca-Cola Refreshments is a wholly owned subsidiary of The Coca-Cola Company, which is the world's largest beverage company in business for more than 126 years with 146,200 associates. The company had a net revenue of $46.5 billion in 2011. Coca-Cola Refreshments is a 21st-century bottling and customer service operation in the U.S. and Canada. The company owns and manages Coca-Cola® branded refrigerators in retail establishments.
挑战
Coca-Cola Refreshments owns and manages Coca-Cola® branded refrigerators in retail establishments. If repairs are needed, equipment may end up at the Make Ready Center. If the equipment can’t be repaired, it may be scrapped. In the past, this meant logging onto legacy systems on multiple servers to locate equipment information, record repair actions and change equipment status. The process was manual, error-prone and took up to eight hours to update information on 30-40 units. The company had no overall visibility into equipment status or maintenance history.
解决方案
Coca-Cola Refreshments found a new thirst for Business Process Management (BPM) with this process automation project. Not only has the company automated the process, it has gained new visibility in equipment use that can improve the bottom line. Now, when equipment arrives at a repair center, associates use a wireless scanner to log up to 60 units at a time. Then they go to a desktop application to assign actions from a standard list. Every piece of equipment goes through a complete cycle of checks, and data is recorded to create a single record on the equipment’s life cycle. The solution incorporates webMethods Business Process Management Suite, Integration Server and Broker. webMethods Optimize for Process tracks how long the batch transmissions take, aids in error handling, keeps count of how many units are moved and captures data to identify opportunities for continued process improvement. Web service calls use the equipment number to gather metadata about the unit from the AS-400-based legacy application, which remains the system of record.
运营影响
数量效益
Case Study missing?
Start adding your own!
Register with your work email and create a new case study profile for your business.
相关案例.

Case Study
The Kellogg Company
Kellogg keeps a close eye on its trade spend, analyzing large volumes of data and running complex simulations to predict which promotional activities will be the most effective. Kellogg needed to decrease the trade spend but its traditional relational database on premises could not keep up with the pace of demand.
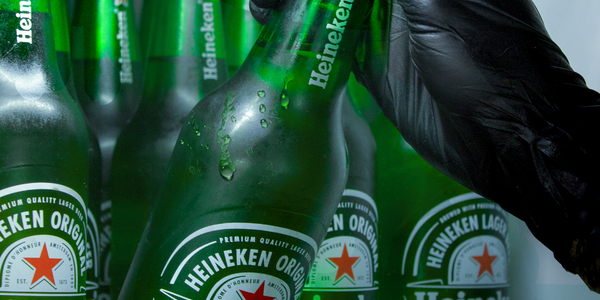
Case Study
HEINEKEN Uses the Cloud to Reach 10.5 Million Consumers
For 2012 campaign, the Bond promotion, it planned to launch the campaign at the same time everywhere on the planet. That created unprecedented challenges for HEINEKEN—nowhere more so than in its technology operation. The primary digital content for the campaign was a 100-megabyte movie that had to play flawlessly for millions of viewers worldwide. After all, Bond never fails. No one was going to tolerate a technology failure that might bruise his brand.Previously, HEINEKEN had supported digital media at its outsourced datacenter. But that datacenter lacked the computing resources HEINEKEN needed, and building them—especially to support peak traffic that would total millions of simultaneous hits—would have been both time-consuming and expensive. Nor would it have provided the geographic reach that HEINEKEN needed to minimize latency worldwide.
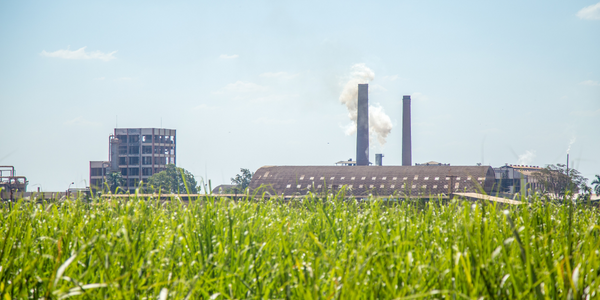
Case Study
Energy Management System at Sugar Industry
The company wanted to use the information from the system to claim under the renewable energy certificate scheme. The benefit to the company under the renewable energy certificates is Rs 75 million a year. To enable the above, an end-to-end solution for load monitoring, consumption monitoring, online data monitoring, automatic meter data acquisition which can be exported to SAP and other applications is required.
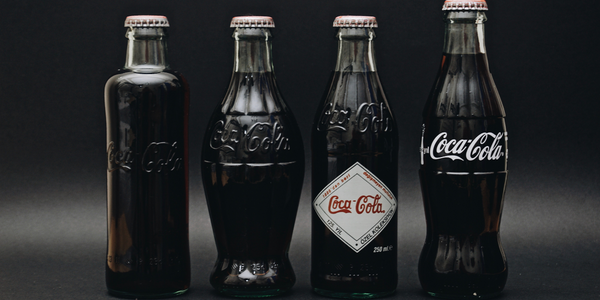
Case Study
Coca Cola Swaziland Conco Case Study
Coco Cola Swaziland, South Africa would like to find a solution that would enable the following results: - Reduce energy consumption by 20% in one year. - Formulate a series of strategic initiatives that would enlist the commitment of corporate management and create employee awareness while helping meet departmental targets and investing in tools that assist with energy management. - Formulate a series of tactical initiatives that would optimize energy usage on the shop floor. These would include charging forklifts and running cold rooms only during off-peak periods, running the dust extractors only during working hours and basing lights and air-conditioning on someone’s presence. - Increase visibility into the factory and other processes. - Enable limited, non-intrusive control functions for certain processes.
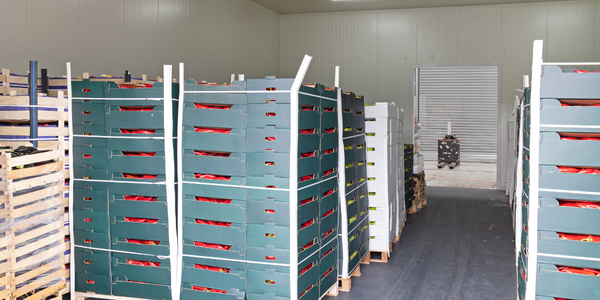
Case Study
Temperature Monitoring for Restaurant Food Storage
When it came to implementing a solution, Mr. Nesbitt had an idea of what functionality that he wanted. Although not mandated by Health Canada, Mr. Nesbitt wanted to ensure quality control issues met the highest possible standards as part of his commitment to top-of-class food services. This wish list included an easy-to use temperature-monitoring system that could provide a visible display of the temperatures of all of his refrigerators and freezers, including historical information so that he could review the performance of his equipment. It also had to provide alert notification (but email alerts and SMS text message alerts) to alert key staff in the event that a cooling system was exceeding pre-set warning limits.
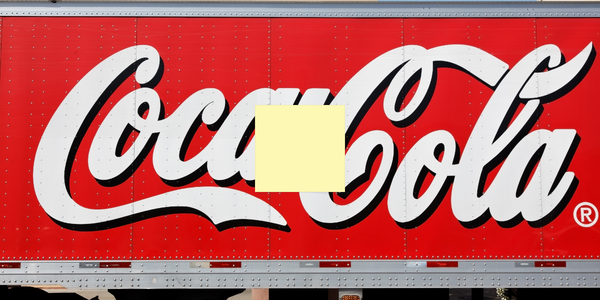
Case Study
Coca-Cola Refreshments, U.S.
Coca-Cola Refreshments owns and manages Coca-Cola branded refrigerators in retail establishments. Legacy systems were used to locate equipment information by logging onto multiple servers which took up to 8 hours to update information on 30-40 units. The company had no overall visibility into equipment status or maintenance history.