公司规模
Mid-size Company
地区
- America
国家
- United States
产品
- Plex
- IntelliPlex
- Plex Web Services
技术栈
- Cloud-based Architecture
- Business Intelligence Software
实施规模
- Enterprise-wide Deployment
影响指标
- Productivity Improvements
- Cost Savings
- Digital Expertise
技术
- 平台即服务 (PaaS) - 数据管理平台
- 功能应用 - 企业资源规划系统 (ERP)
- 分析与建模 - 大数据分析
适用行业
- 航天
- 医疗保健和医院
适用功能
- 产品研发
- 质量保证
- 商业运营
用例
- 预测性维护
- 机器状态监测
- 远程资产管理
服务
- 云规划/设计/实施服务
- 系统集成
- 软件设计与工程服务
关于客户
Quatro Composites is a contract component manufacturer and developer specializing in the design, analysis, prototyping, and production of advanced composite structures. The company operates in the aerospace, medical, and industrial markets, focusing on converting small parts typically made of metal or other materials into carbon fiber composites. This conversion results in parts that are lighter, safer, and stronger. Quatro's primary engineering and technology center is located in Poway, California, while its corporate administration, manufacturing, warehousing, and distribution are based in Orange City, Iowa. Over the past decade, Quatro has experienced significant growth, expanding its operations eight times to accommodate a 25-50 percent year-over-year growth rate. The largest expansion occurred in 2012 when the company doubled its manufacturing space. Quatro's commitment to innovation and quality has positioned it as a leader in the composites manufacturing industry, serving a diverse range of clients with its advanced composite solutions.
挑战
Quatro Composites faced a significant challenge in managing its rapid growth and the complexity of its operations. The company had inherited an IFS ERP solution from its sister company, which did not meet its needs. This led to an exhaustive search for a new ERP/MRP solution that could handle multi-location access, scalability, and a low total cost of ownership (TCO) over ten years. The existing system was heavily reliant on manual data entry through spreadsheets and Access databases, which was inefficient and prone to errors. Quatro needed a solution that could automate data collection and provide a centralized, integrated system for managing business operations and data storage. The company also required a system that could support collaborative processes, eliminate departmental siloes, and improve data integrity to speed up product development. Additionally, Quatro aimed to reduce scrap across the organization and needed a system that could provide comprehensive analytics and reporting capabilities to track progress and savings for continuous improvement.
解决方案
Quatro Composites selected Plex as its ERP/MRP solution after evaluating 40 providers. Plex's cloud-based architecture offered multi-location ease of access, scalability, and a low 10-year TCO, which were crucial for Quatro's rapid growth. The system replaced the manual data entry process with an automated data collection system, allowing for efficient recording, managing, and accessing of production information with minimal operator input. Plex provided a central, integrated system that managed Quatro's business operations and stored all data, enabling comprehensive analysis and reporting across the organization. The cloud-based system supported collaborative processes, eliminating departmental siloes and improving data integrity. This facilitated faster product development and allowed employees at different sites to access documents and data with ease. Quatro also utilized IntelliPlex business intelligence software to centralize data in the Plex database, making it visible across the company. The software enabled the creation of role-oriented reports and dashboards, which automatically generated reports on various timeframes. Quatro designed a closed-loop process leveraging IntelliPlex reporting to track progress and savings for continuous improvement, with a focus on reducing scrap across the organization. The company plans to expand its use of IntelliPlex and increase the number of IntelliPlex builders by 50 percent over the next year to exploit additional Big Data sources and provide custom dashboards and reports to various departments.
运营影响
数量效益
Case Study missing?
Start adding your own!
Register with your work email and create a new case study profile for your business.
相关案例.
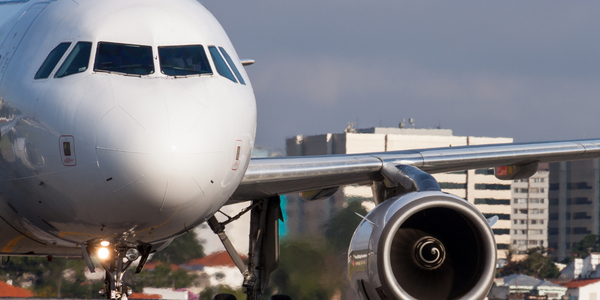
Case Study
Airbus Soars with Wearable Technology
Building an Airbus aircraft involves complex manufacturing processes consisting of thousands of moving parts. Speed and accuracy are critical to business and competitive advantage. Improvements in both would have high impact on Airbus’ bottom line. Airbus wanted to help operators reduce the complexity of assembling cabin seats and decrease the time required to complete this task.
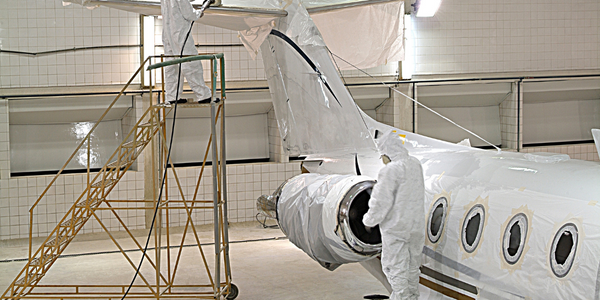
Case Study
Aircraft Predictive Maintenance and Workflow Optimization
First, aircraft manufacturer have trouble monitoring the health of aircraft systems with health prognostics and deliver predictive maintenance insights. Second, aircraft manufacturer wants a solution that can provide an in-context advisory and align job assignments to match technician experience and expertise.
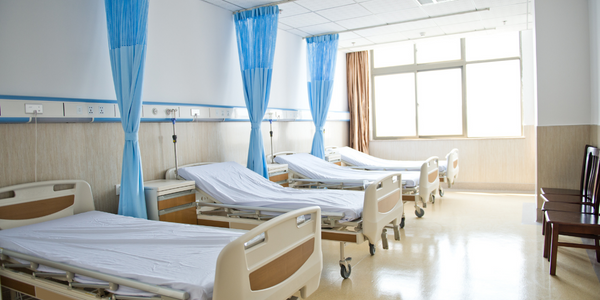
Case Study
Hospital Inventory Management
The hospital supply chain team is responsible for ensuring that the right medical supplies are readily available to clinicians when and where needed, and to do so in the most efficient manner possible. However, many of the systems and processes in use at the cancer center for supply chain management were not best suited to support these goals. Barcoding technology, a commonly used method for inventory management of medical supplies, is labor intensive, time consuming, does not provide real-time visibility into inventory levels and can be prone to error. Consequently, the lack of accurate and real-time visibility into inventory levels across multiple supply rooms in multiple hospital facilities creates additional inefficiency in the system causing over-ordering, hoarding, and wasted supplies. Other sources of waste and cost were also identified as candidates for improvement. Existing systems and processes did not provide adequate security for high-cost inventory within the hospital, which was another driver of cost. A lack of visibility into expiration dates for supplies resulted in supplies being wasted due to past expiry dates. Storage of supplies was also a key consideration given the location of the cancer center’s facilities in a dense urban setting, where space is always at a premium. In order to address the challenges outlined above, the hospital sought a solution that would provide real-time inventory information with high levels of accuracy, reduce the level of manual effort required and enable data driven decision making to ensure that the right supplies were readily available to clinicians in the right location at the right time.
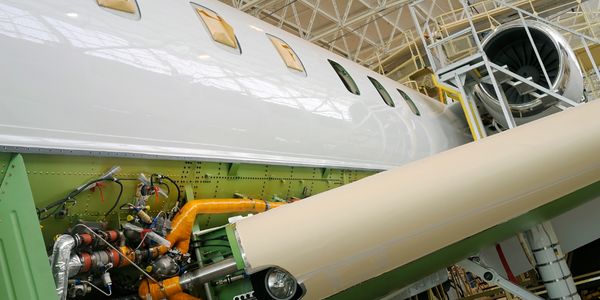
Case Study
Aerospace & Defense Case Study Airbus
For the development of its new wide-body aircraft, Airbus needed to ensure quality and consistency across all internal and external stakeholders. Airbus had many challenges including a very aggressive development schedule and the need to ramp up production quickly to satisfy their delivery commitments. The lack of communication extended design time and introduced errors that drove up costs.
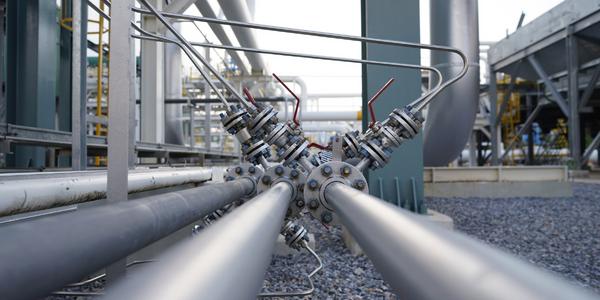
Case Study
Gas Pipeline Monitoring System for Hospitals
This system integrator focuses on providing centralized gas pipeline monitoring systems for hospitals. The service they provide makes it possible for hospitals to reduce both maintenance and labor costs. Since hospitals may not have an existing network suitable for this type of system, GPRS communication provides an easy and ready-to-use solution for remote, distributed monitoring systems System Requirements - GPRS communication - Seamless connection with SCADA software - Simple, front-end control capability - Expandable I/O channels - Combine AI, DI, and DO channels