公司规模
Mid-size Company
地区
- America
国家
- United States
产品
- Plex Manufacturing Cloud ERP
技术栈
- Cloud ERP
- Barcode Inventory System
实施规模
- Enterprise-wide Deployment
影响指标
- Productivity Improvements
- Cost Savings
- Customer Satisfaction
技术
- 功能应用 - 企业资源规划系统 (ERP)
- 网络与连接 - 无线局域网
适用功能
- 商业运营
- 质量保证
用例
- 库存管理
- 过程控制与优化
- 资产跟踪
服务
- 云规划/设计/实施服务
- 系统集成
关于客户
DECC Company, Inc. is a family-owned business based in Grand Rapids, Michigan, specializing in solving customer problems through specialized coating applications and custom coating services. Initially founded to serve the automotive industry, DECC has diversified its services to cater to a variety of industries, including aerospace/avionics, food production, furniture, medical, diesel industries, and the military. Known for its innovative solutions, DECC is recognized as an industry leader by its customers. Despite its reputation, the company had only kept up with evolving enterprise resource planning (ERP) technology on an as-needed basis, which led to challenges in maintaining and upgrading its existing systems. DECC's commitment to quality and customer satisfaction drives its continuous improvement efforts, making it a key player in the industrial manufacturing sector.
挑战
DECC Company faced challenges in maintaining and upgrading its existing maintenance tracking system and gage tracking software. The company had multiple systems tracking different parts of the production process, which did not communicate with each other, making it difficult to get a comprehensive overview of the processes. DECC lacked the ability to easily get a real-time view into the status of all processes within the plant and to share necessary information with its employees and suppliers. The company needed an ERP solution that mirrored the quality of its products and could provide better visibility and traceability across its operations.
解决方案
DECC Company implemented the Plex Manufacturing Cloud ERP solution after attending a presentation by automotive parts manufacturer GR Spring & Stamping. The company was impressed by Plex's focus on capturing information on the shop floor and making it visible throughout the organization. Plex offered all the functional capabilities DECC was seeking without the high cost of configuring a custom solution. The pricing model, which includes a single cost for the entire company regardless of the number of users, was also appealing to DECC. With Plex, DECC achieved enhanced traceability, streamlined workcenter operations, electronic job processing, and improved employee tracking. The ERP system allowed DECC to continually track and control costing as a routine part of the process, enabling the company to anticipate problems before they occur and quickly take necessary actions. Plex's traceability function provided major benefits in the manufacturing process, allowing DECC to track parts, coatings, solvents, and blends with serialized job numbers on barcode labels. This improved the company's ability to detect issues or deviations in the process and quickly introduce solutions.
运营影响
数量效益
Case Study missing?
Start adding your own!
Register with your work email and create a new case study profile for your business.
相关案例.
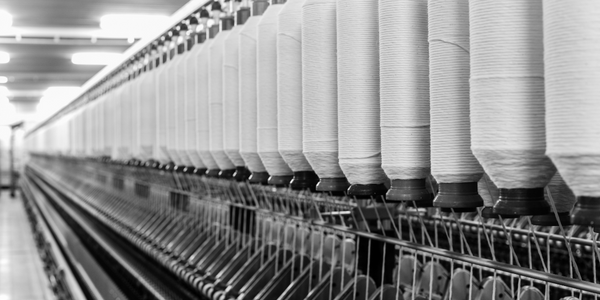
Case Study
IoT Applications and Upgrades in Textile Plant
At any given time, the textile company’s manufacturing facility has up to 2,000 textile carts in use. These carts are pushed from room to room, carrying materials or semi-finished products. Previously, a paper with a hand-written description was attached to each cart. This traditional method of processing made product tracking extremely difficult. Additionally, making sure that every cart of materials or semi-finished products went to its correct processing work station was also a problem. Therefore, the company desired an intelligent solution for tracking assets at their factories. They also wanted a solution that would help them collect process data so they could improve their manufacturing efficiency.
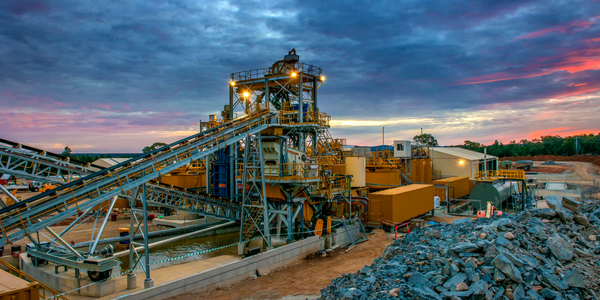
Case Study
Goldcorp: Internet of Things Enables the Mine of the Future
Goldcorp is committed to responsible mining practices and maintaining maximum safety for its workers. At the same time, the firm is constantly exploring ways to improve the efficiency of its operations, extend the life of its assets, and control costs. Goldcorp needed technology that can maximize production efficiency by tracking all mining operations, keep employees safe with remote operations and monitoring of hazardous work areas and control production costs through better asset and site management.
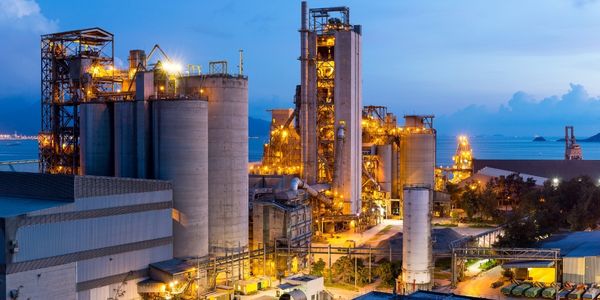
Case Study
System 800xA at Indian Cement Plants
Chettinad Cement recognized that further efficiencies could be achieved in its cement manufacturing process. It looked to investing in comprehensive operational and control technologies to manage and derive productivity and energy efficiency gains from the assets on Line 2, their second plant in India.
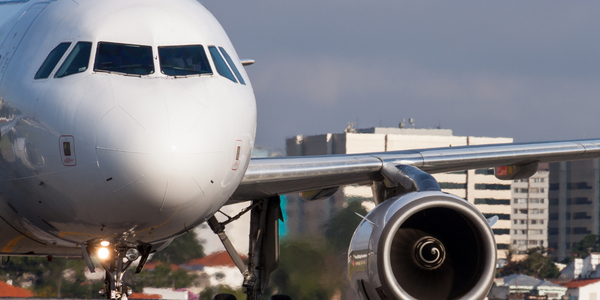
Case Study
Airbus Soars with Wearable Technology
Building an Airbus aircraft involves complex manufacturing processes consisting of thousands of moving parts. Speed and accuracy are critical to business and competitive advantage. Improvements in both would have high impact on Airbus’ bottom line. Airbus wanted to help operators reduce the complexity of assembling cabin seats and decrease the time required to complete this task.