公司规模
Large Corporate
国家
- Worldwide
产品
- Catalytic
技术栈
- AI
- Intelligent Automation
实施规模
- Enterprise-wide Deployment
影响指标
- Productivity Improvements
- Cost Savings
技术
- 应用基础设施与中间件 - API 集成与管理
适用功能
- 商业运营
用例
- 过程控制与优化
服务
- 软件设计与工程服务
关于客户
电通安吉斯集团是一家媒体和数字营销传播公司,业务遍及 145 个国家。该公司拥有 50,000 多名员工,为 11,000 多家客户提供服务。电通致力于创新,并建立了自动化专业知识中心 (COE),以确保公司的运营始终保持领先地位。自动化 COE 为电通提供了一个框架,以识别集成和智能自动化机会,从而改进其流程并兑现为客户和社会创造新价值的承诺。
挑战
电通安吉斯集团是一家媒体和数字营销传播公司,其中台媒体激活流程面临挑战。这些流程重复、耗时,而且容易出现人为错误。每个客户都有不同的需求,电通需要适应每个客户的需求。该流程需要多个利益相关者之间进行大量的反复沟通,而且团队成员对客户的响应速度会影响流程的速度。需要整个团队来承担预对帐实际工作,以确认大客户的媒体支出。
解决方案
Dentsu 与 Catalytic 合作,实现中台媒体激活流程的自动化。Catalytic 的人工智能和智能自动化方法因其灵活性和可靠的卓越运营经验而被选中。自动化流程包括从多个系统中提取报告、管理和组织数据、自动发送电子邮件进行验证、整合反馈以及使用收集到的反馈更新系统。在两周内,Catalytic 为一个客户团队提供了解决方案,该解决方案将在 2019 年底前部署到 30 多个团队。Catalytic 与 Dentsu 合作制定了进一步自动化的路线图。
运营影响
数量效益
Case Study missing?
Start adding your own!
Register with your work email and create a new case study profile for your business.
相关案例.
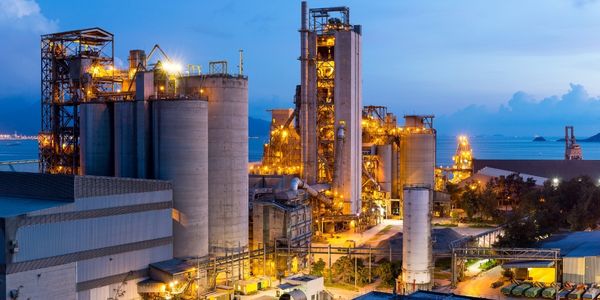
Case Study
System 800xA at Indian Cement Plants
Chettinad Cement recognized that further efficiencies could be achieved in its cement manufacturing process. It looked to investing in comprehensive operational and control technologies to manage and derive productivity and energy efficiency gains from the assets on Line 2, their second plant in India.
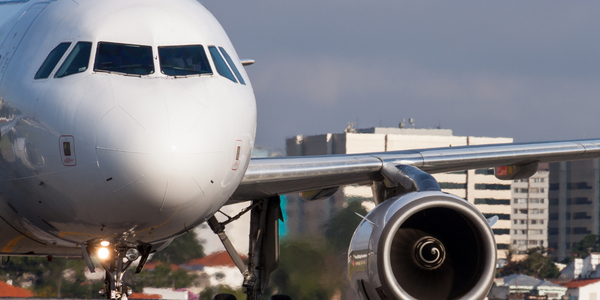
Case Study
Airbus Soars with Wearable Technology
Building an Airbus aircraft involves complex manufacturing processes consisting of thousands of moving parts. Speed and accuracy are critical to business and competitive advantage. Improvements in both would have high impact on Airbus’ bottom line. Airbus wanted to help operators reduce the complexity of assembling cabin seats and decrease the time required to complete this task.
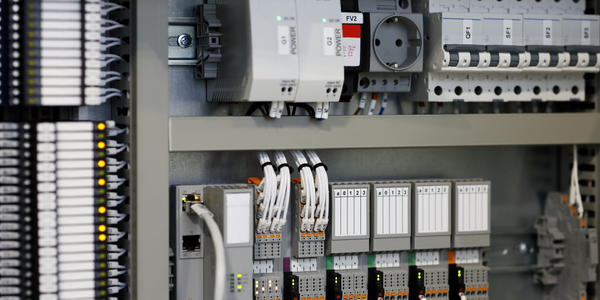
Case Study
Improving Production Line Efficiency with Ethernet Micro RTU Controller
Moxa was asked to provide a connectivity solution for one of the world's leading cosmetics companies. This multinational corporation, with retail presence in 130 countries, 23 global braches, and over 66,000 employees, sought to improve the efficiency of their production process by migrating from manual monitoring to an automatic productivity monitoring system. The production line was being monitored by ABB Real-TPI, a factory information system that offers data collection and analysis to improve plant efficiency. Due to software limitations, the customer needed an OPC server and a corresponding I/O solution to collect data from additional sensor devices for the Real-TPI system. The goal is to enable the factory information system to more thoroughly collect data from every corner of the production line. This will improve its ability to measure Overall Equipment Effectiveness (OEE) and translate into increased production efficiencies. System Requirements • Instant status updates while still consuming minimal bandwidth to relieve strain on limited factory networks • Interoperable with ABB Real-TPI • Small form factor appropriate for deployment where space is scarce • Remote software management and configuration to simplify operations
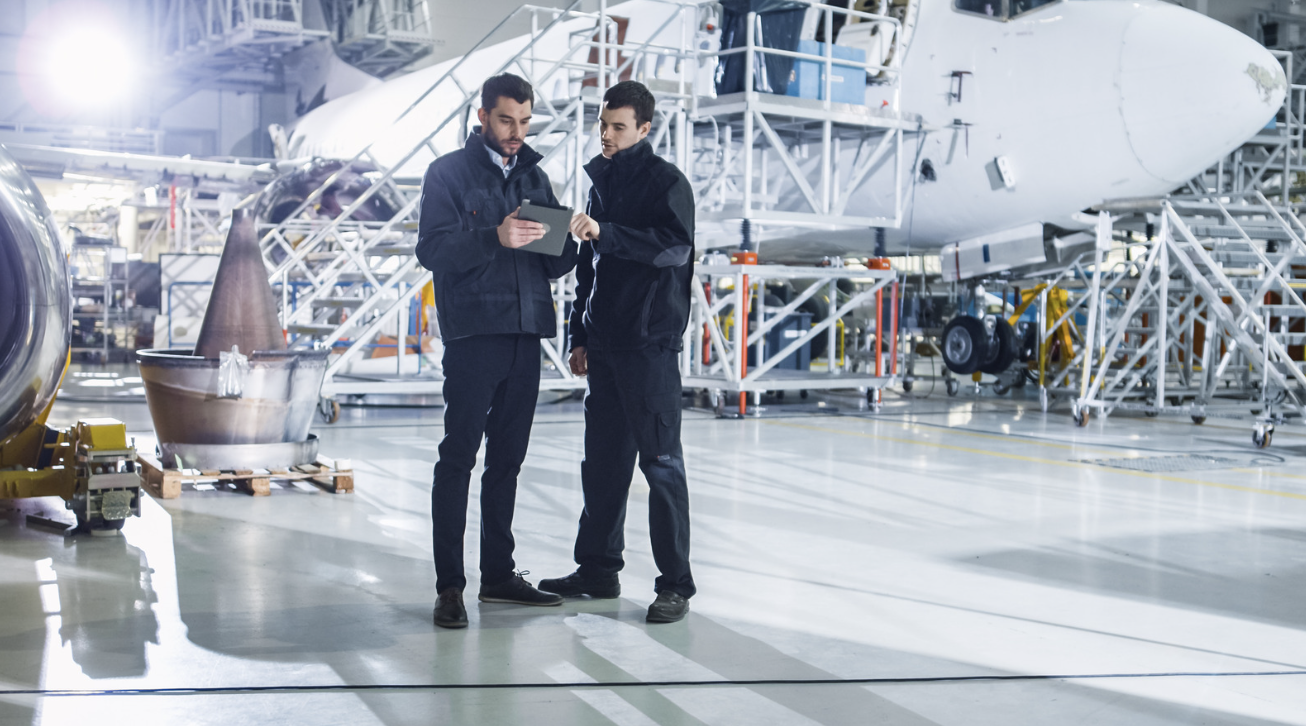
Case Study
Developing Smart Tools for the Airbus Factory
Manufacturing and assembly of aircraft, which involves tens of thousands of steps that must be followed by the operators, and a single mistake in the process could cost hundreds of thousands of dollars to fix, makes the room for error very small.