Digital Factory Transformation with 26,000 Pieces of Manufacturing Equipment Connected in the Cloud
公司规模
Large Corporate
国家
- Worldwide
产品
- 42Q
技术栈
- Cloud Computing
- IIoT
实施规模
- Enterprise-wide Deployment
影响指标
- Productivity Improvements
- Cost Savings
技术
- 基础设施即服务 (IaaS) - 云计算
适用行业
- 电子产品
- 汽车
- 医疗保健和医院
适用功能
- 离散制造
- 质量保证
用例
- 自动化制造系统
- 供应链可见性(SCV)
服务
- 云规划/设计/实施服务
- 系统集成
关于客户
Sanmina is a tier one contract manufacturer that manufactures 250 million products annually for 700 different Original Equipment Manufacturers (OEMs). The company produces over 200,000 different top-level assemblies each year, with up to 20,000 forecast changes per week. The OEMs that Sanmina serves operate in diverse industries including telecommunications, enterprise computing & storage, industrial and clean technology. A significant amount of Sanmina's production is for medical, aerospace and automotive products, which have strict regulatory requirements. The company has 50 manufacturing facilities worldwide.
挑战
Sanmina, a tier one contract manufacturer, was facing challenges with its existing on-premise Manufacturing Execution System (MES). The system, although advanced, limited the management's visibility of real-time production metrics in each factory and required significant maintenance from operations and IT teams. The company manufactures 250 million products per year for 700 different OEM customers, with over 200,000 different top-level assemblies produced each year. The OEMs operate in diverse industries including telecommunications, enterprise computing & storage, industrial and clean technology. A significant amount of production is for medical, aerospace and automotive products with strict regulatory requirements. The existing on-premise MES was not well suited for factory automation and other IIoT initiatives.
解决方案
Sanmina adopted 42Q, a fully featured global cloud-based system capable of integrating product yield, WIP and inventory information across a global network of 10,000 suppliers delivering components to 50 manufacturing facilities in 15 countries around the world. The solution accommodated Sanmina’s diverse manufacturing processes including enclosure fabrication, PCBA manufacturing and complex systems integration. It also complies with regulatory requirements in medical, aerospace and automotive industries. A unified multitenant cloud architecture with in-built redundancy provides access from anywhere in the world. A method to digitally represent product specifications and manufacturing processes was developed. 26,000 devices including scanners, production equipment, automatic optical inspection machines and functional testers were connected to 42Q, providing data in real time. Applications accessible by browser from anywhere in the world were developed to analyze millions of records of data and present it in an actionable manner.
运营影响
Case Study missing?
Start adding your own!
Register with your work email and create a new case study profile for your business.
相关案例.
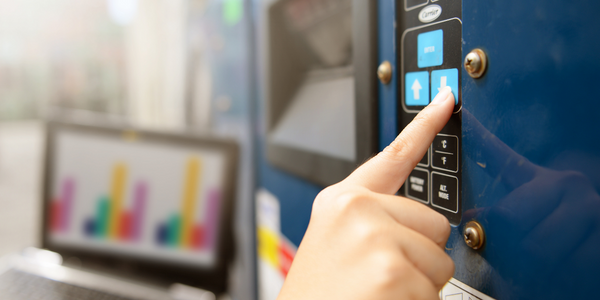
Case Study
Remote Temperature Monitoring of Perishable Goods Saves Money
RMONI was facing temperature monitoring challenges in a cold chain business. A cold chain must be established and maintained to ensure goods have been properly refrigerated during every step of the process, making temperature monitoring a critical business function. Manual registration practice can be very costly, labor intensive and prone to mistakes.
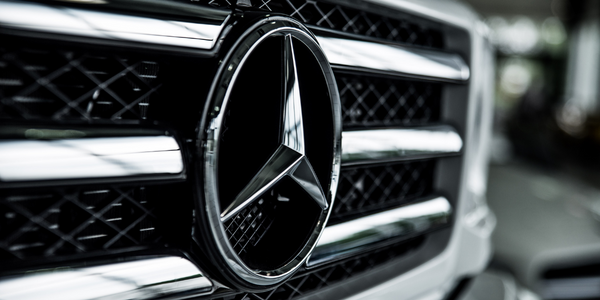
Case Study
Integral Plant Maintenance
Mercedes-Benz and his partner GAZ chose Siemens to be its maintenance partner at a new engine plant in Yaroslavl, Russia. The new plant offers a capacity to manufacture diesel engines for the Russian market, for locally produced Sprinter Classic. In addition to engines for the local market, the Yaroslavl plant will also produce spare parts. Mercedes-Benz Russia and his partner needed a service partner in order to ensure the operation of these lines in a maintenance partnership arrangement. The challenges included coordinating the entire maintenance management operation, in particular inspections, corrective and predictive maintenance activities, and the optimizing spare parts management. Siemens developed a customized maintenance solution that includes all electronic and mechanical maintenance activities (Integral Plant Maintenance).
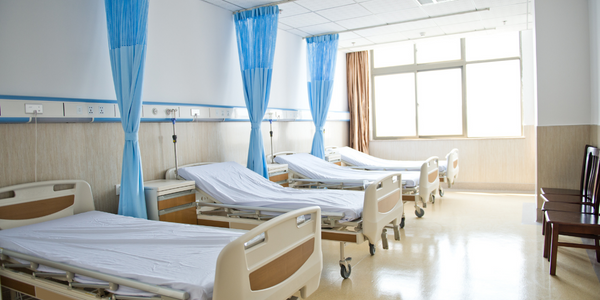
Case Study
Hospital Inventory Management
The hospital supply chain team is responsible for ensuring that the right medical supplies are readily available to clinicians when and where needed, and to do so in the most efficient manner possible. However, many of the systems and processes in use at the cancer center for supply chain management were not best suited to support these goals. Barcoding technology, a commonly used method for inventory management of medical supplies, is labor intensive, time consuming, does not provide real-time visibility into inventory levels and can be prone to error. Consequently, the lack of accurate and real-time visibility into inventory levels across multiple supply rooms in multiple hospital facilities creates additional inefficiency in the system causing over-ordering, hoarding, and wasted supplies. Other sources of waste and cost were also identified as candidates for improvement. Existing systems and processes did not provide adequate security for high-cost inventory within the hospital, which was another driver of cost. A lack of visibility into expiration dates for supplies resulted in supplies being wasted due to past expiry dates. Storage of supplies was also a key consideration given the location of the cancer center’s facilities in a dense urban setting, where space is always at a premium. In order to address the challenges outlined above, the hospital sought a solution that would provide real-time inventory information with high levels of accuracy, reduce the level of manual effort required and enable data driven decision making to ensure that the right supplies were readily available to clinicians in the right location at the right time.