FloraCraft's Transition to Plex Manufacturing Cloud Enhances Operational Efficiency and Revenue Growth
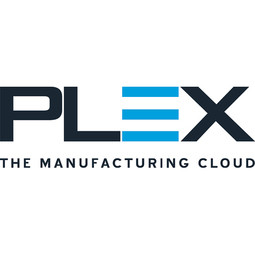
公司规模
Mid-size Company
地区
- America
国家
- United States
产品
- Plex Manufacturing Cloud
- WHSe-LINK
- MXP ERP
技术栈
- Cloud Computing
- ERP Systems
实施规模
- Enterprise-wide Deployment
影响指标
- Productivity Improvements
- Revenue Growth
- Customer Satisfaction
技术
- 平台即服务 (PaaS) - 数据管理平台
- 功能应用 - 企业资源规划系统 (ERP)
适用功能
- 商业运营
- 仓库和库存管理
用例
- 库存管理
- 过程控制与优化
- 供应链可见性(SCV)
服务
- 云规划/设计/实施服务
- 培训
关于客户
FloraCraft, based in Ludington, Michigan, is a family-owned business that has been operating for 70 years. Initially serving the floral arrangements sector, the company expanded into the craft market, producing children's products and educational items. FloraCraft has built a reputation for quality and innovation, which has allowed it to reinvent itself and focus on mass-market production. This strategic shift has led to a significant increase in inventory and product lines, securing additional shelf space with large-scale retailers. With a portfolio of 3,500 SKUs, FloraCraft has fortified its logistics and supply chain capabilities to meet the demands of its expanded operations. The company views IT as a core component of its business strategy, aiming to leverage technology to improve processes, create competitive differentiation, and drive business growth.
挑战
FloraCraft faced challenges with its legacy ERP system, which was unable to keep up with the company's growing needs. The existing system, MXP ERP, provided limited visibility into operational capabilities and financial status, and the warehouse management system, WHSe-LINK, had a lag time in data updates. The company needed a more integrated and real-time solution to manage its expanded product lines and increased lead times for overseas manufacturing operations. Additionally, the manual verification process for universal product codes (UPCs) was prone to errors, which was a significant issue given the company's 3,500 SKUs.
解决方案
FloraCraft implemented the Plex Manufacturing Cloud, a true cloud solution that provides always-current functionality without version control issues. This transition allowed FloraCraft to eliminate the need for managing additional servers and software, reducing overhead and simplifying ERP licensing management. The company designed a comprehensive testing and training plan to ensure a seamless cutover and protect production integrity. Intensive training was provided to the plant floor workforce, enabling them to effectively use the new system despite initial concerns about their IT skills. The Plex Manufacturing Cloud introduced automated scanning and verification of UPC codes, eliminating manual errors and ensuring 100% accuracy. The system also provided real-time data and insights, allowing FloraCraft to make informed decisions about product development and operational efficiency.
运营影响
数量效益
Case Study missing?
Start adding your own!
Register with your work email and create a new case study profile for your business.
相关案例.
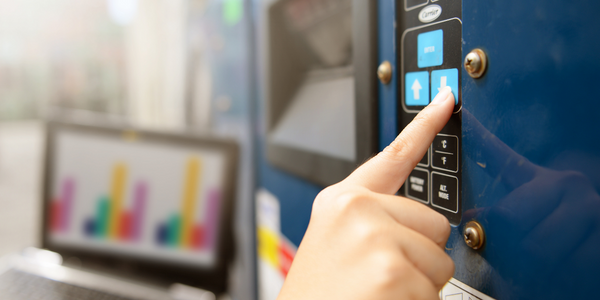
Case Study
Remote Temperature Monitoring of Perishable Goods Saves Money
RMONI was facing temperature monitoring challenges in a cold chain business. A cold chain must be established and maintained to ensure goods have been properly refrigerated during every step of the process, making temperature monitoring a critical business function. Manual registration practice can be very costly, labor intensive and prone to mistakes.
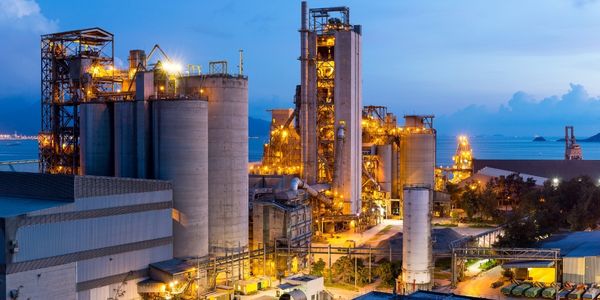
Case Study
System 800xA at Indian Cement Plants
Chettinad Cement recognized that further efficiencies could be achieved in its cement manufacturing process. It looked to investing in comprehensive operational and control technologies to manage and derive productivity and energy efficiency gains from the assets on Line 2, their second plant in India.
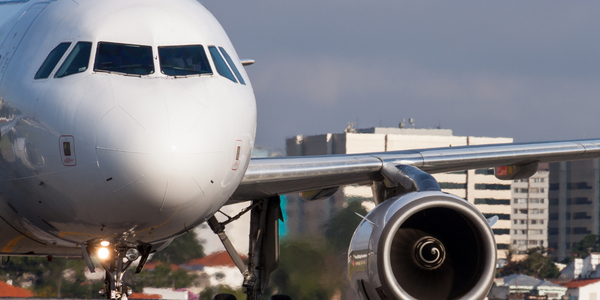
Case Study
Airbus Soars with Wearable Technology
Building an Airbus aircraft involves complex manufacturing processes consisting of thousands of moving parts. Speed and accuracy are critical to business and competitive advantage. Improvements in both would have high impact on Airbus’ bottom line. Airbus wanted to help operators reduce the complexity of assembling cabin seats and decrease the time required to complete this task.
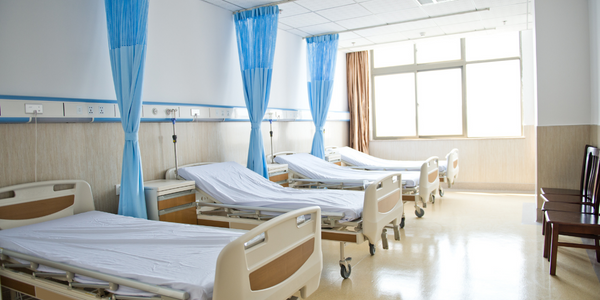
Case Study
Hospital Inventory Management
The hospital supply chain team is responsible for ensuring that the right medical supplies are readily available to clinicians when and where needed, and to do so in the most efficient manner possible. However, many of the systems and processes in use at the cancer center for supply chain management were not best suited to support these goals. Barcoding technology, a commonly used method for inventory management of medical supplies, is labor intensive, time consuming, does not provide real-time visibility into inventory levels and can be prone to error. Consequently, the lack of accurate and real-time visibility into inventory levels across multiple supply rooms in multiple hospital facilities creates additional inefficiency in the system causing over-ordering, hoarding, and wasted supplies. Other sources of waste and cost were also identified as candidates for improvement. Existing systems and processes did not provide adequate security for high-cost inventory within the hospital, which was another driver of cost. A lack of visibility into expiration dates for supplies resulted in supplies being wasted due to past expiry dates. Storage of supplies was also a key consideration given the location of the cancer center’s facilities in a dense urban setting, where space is always at a premium. In order to address the challenges outlined above, the hospital sought a solution that would provide real-time inventory information with high levels of accuracy, reduce the level of manual effort required and enable data driven decision making to ensure that the right supplies were readily available to clinicians in the right location at the right time.