GE Tackles the Industrial Internet
公司规模
Large Corporate
地区
- America
国家
- United States
产品
- Flight Quest I
- Flight Quest II
- Hospital Quest
技术栈
- Big Data Analytics
- Predictive Analytics
- Real Time Analytics
实施规模
- Enterprise-wide Deployment
影响指标
- Cost Savings
- Customer Satisfaction
- Productivity Improvements
技术
- 分析与建模 - 大数据分析
- 分析与建模 - 预测分析
- 分析与建模 - 实时分析
适用行业
- 医疗保健和医院
- 运输
适用功能
- 物流运输
- 质量保证
用例
- 过程控制与优化
- 实时定位系统 (RTLS)
服务
- 数据科学服务
- 系统集成
关于客户
General Electric (GE) is a multinational conglomerate headquartered in Boston, Massachusetts. Founded in 1892, GE operates in various sectors including aviation, healthcare, power, renewable energy, digital industry, additive manufacturing, and venture capital and finance. With a workforce of over 200,000 employees, GE is a leader in industrial technology and innovation. The company has been at the forefront of leveraging advanced technologies to solve complex industrial challenges. Since 2012, GE has pursued a multi-year initiative to leverage the “Industrial Internet” of smart machines and advanced analytics. This initiative aims to integrate machine learning, big data, and IoT to optimize industrial operations and drive efficiency.
挑战
Flight dynamics change quickly. From weather to gate conflicts, efficiently adapting to changing flight conditions can save millions of dollars in annual fuel costs, as well as reducing carbon emissions. Flight Quest tackled this real-time big data analysis challenge. In Flight Quest I, participants were given multi-source flight and weather data and asked to predict precise runway and gate arrival times for domestic flights in the United States. The winners produced a 40% accuracy improvement over industry standards—equivalent to saving 5 minutes at the gate per flight (an annual savings of $6.2 million for a mid-sized airline). Flight Quest II was even more challenging: Participants optimized flights in real time. The second phase included significantly more complex weather data—rain, wind, barometric pressure, ice, and more—as well as crew and passenger counts, airport traffic, and no-fly-zones. The winning solution was evaluated in a flight simulator and found to be a 12% efficiency and cost improvement over real flights.
解决方案
GE engaged Kaggle to organize and run three competitions, offering prizes totaling $600,000 to solve high-impact business problems from flight efficiency to hospital operations. In Flight Quest I, participants were given multi-source flight and weather data and asked to predict precise runway and gate arrival times for domestic flights in the United States. The winners produced a 40% accuracy improvement over industry standards. Flight Quest II was even more challenging: Participants optimized flights in real time. The second phase included significantly more complex weather data—rain, wind, barometric pressure, ice, and more—as well as crew and passenger counts, airport traffic, and no-fly-zones. The winning solution was evaluated in a flight simulator and found to be a 12% efficiency and cost improvement over real flights. For Hospital Quest, participants developed healthcare solutions that were evaluated by experts for quality, impact, and ease of implementation. The winning team implemented a referral management system to simplify hospital discharge workflows and greatly improve the quality of post-acute care.
运营影响
数量效益
Case Study missing?
Start adding your own!
Register with your work email and create a new case study profile for your business.
相关案例.
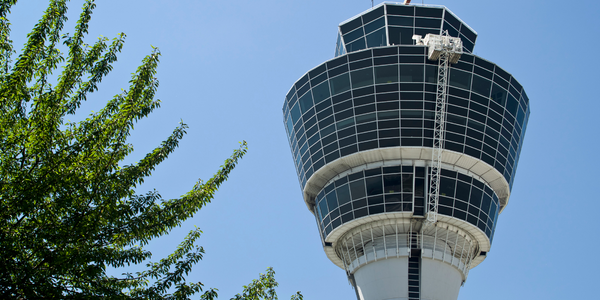
Case Study
Airport SCADA Systems Improve Service Levels
Modern airports are one of the busiest environments on Earth and rely on process automation equipment to ensure service operators achieve their KPIs. Increasingly airport SCADA systems are being used to control all aspects of the operation and associated facilities. This is because unplanned system downtime can cost dearly, both in terms of reduced revenues and the associated loss of customer satisfaction due to inevitable travel inconvenience and disruption.
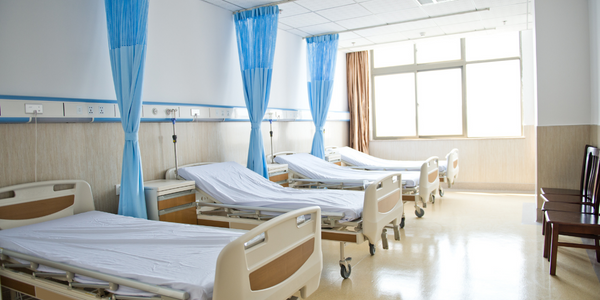
Case Study
Hospital Inventory Management
The hospital supply chain team is responsible for ensuring that the right medical supplies are readily available to clinicians when and where needed, and to do so in the most efficient manner possible. However, many of the systems and processes in use at the cancer center for supply chain management were not best suited to support these goals. Barcoding technology, a commonly used method for inventory management of medical supplies, is labor intensive, time consuming, does not provide real-time visibility into inventory levels and can be prone to error. Consequently, the lack of accurate and real-time visibility into inventory levels across multiple supply rooms in multiple hospital facilities creates additional inefficiency in the system causing over-ordering, hoarding, and wasted supplies. Other sources of waste and cost were also identified as candidates for improvement. Existing systems and processes did not provide adequate security for high-cost inventory within the hospital, which was another driver of cost. A lack of visibility into expiration dates for supplies resulted in supplies being wasted due to past expiry dates. Storage of supplies was also a key consideration given the location of the cancer center’s facilities in a dense urban setting, where space is always at a premium. In order to address the challenges outlined above, the hospital sought a solution that would provide real-time inventory information with high levels of accuracy, reduce the level of manual effort required and enable data driven decision making to ensure that the right supplies were readily available to clinicians in the right location at the right time.
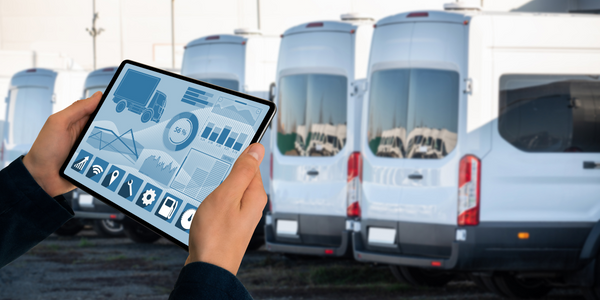
Case Study
IoT-based Fleet Intelligence Innovation
Speed to market is precious for DRVR, a rapidly growing start-up company. With a business model dependent on reliable mobile data, managers were spending their lives trying to negotiate data roaming deals with mobile network operators in different countries. And, even then, service quality was a constant concern.
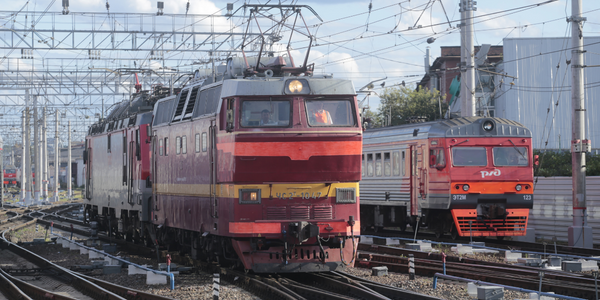
Case Study
Digitize Railway with Deutsche Bahn
To reduce maintenance costs and delay-causing failures for Deutsche Bahn. They need manual measurements by a position measurement system based on custom-made MEMS sensor clusters, which allow autonomous and continuous monitoring with wireless data transmission and long battery. They were looking for data pre-processing solution in the sensor and machine learning algorithms in the cloud so as to detect critical wear.
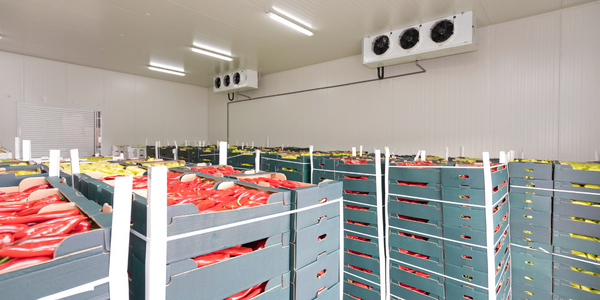
Case Study
Cold Chain Transportation and Refrigerated Fleet Management System
1) Create a digital connected transportation solution to retrofit cold chain trailers with real-time tracking and controls. 2) Prevent multi-million dollar losses due to theft or spoilage. 3) Deliver a digital chain-of-custody solution for door to door load monitoring and security. 4) Provide a trusted multi-fleet solution in a single application with granular data and access controls.