公司规模
Large Corporate
地区
- Europe
- America
- Asia
国家
- Germany
- Hungary
- Poland
- Spain
- Mexico
产品
- HYDRA Shop Floor Scheduling
- HYDRA Shop Floor Data Collection
- HYDRA Premium & Incentive Wages
- HYDRA Access Control
技术栈
- Windows Server
- Oracle Database
- SAP Interfaces
实施规模
- Enterprise-wide Deployment
影响指标
- Digital Expertise
- Productivity Improvements
技术
- 功能应用 - 制造执行系统 (MES)
- 应用基础设施与中间件 - 数据交换与集成
适用行业
- 汽车
适用功能
- 流程制造
- 质量保证
用例
- 自动化制造系统
- 机器状态监测
- 过程控制与优化
服务
- 系统集成
关于客户
GEDIA Automotive Group, founded in 1910 in Attendorn, is a leading developer and processor of stamped body parts, welded assemblies, and safety components for the automotive industry. With an annual turnover exceeding 600 million Euros, GEDIA employs over 4,000 people across eight production sites in Germany, Spain, Hungary, Poland, India, China, USA, and Mexico. The company is known for its high technical innovation, continuous process optimization, and customer-oriented organization. GEDIA's modern production technologies and in-house tool development have positioned it as a key supplier to international automotive giants like Ford, Opel, VW, BMW, and AUDI. The company is certified to ISO TS 16949, ensuring compliance with stringent quality standards.
挑战
GEDIA Automotive Group required a modular application package to connect ERP, HR, and production systems to increase machine and personnel capacities, obtain real-time data evaluations, and optimize planning. The challenge was to use as many standard functions as possible to ensure seamless integration and efficiency. The company needed a solution that could handle detailed planning on shift levels, specify order processing, and provide real-time progress tracking. Additionally, the solution had to support data collection from numerous machines and terminals, and facilitate the calculation of incentive wages while ensuring access control for authorized personnel.
解决方案
GEDIA implemented the MES solution HYDRA as a subsystem to SAP to address its challenges. The HYDRA Shop Floor Scheduling module was used to transfer production orders from SAP for detailed planning on shift levels. This module specified which order was processed in which shift and on what machine. The HYDRA Shop Floor Data Collection module allowed users to view order progress online, utilizing numerous PCs and terminals to collect order and machine data. Over 290 machines, including presses and welding robots, were directly connected to HYDRA. The system was used by management, production managers, and supervisors on 160 PCs to issue reports and evaluations such as shift reports and downtime analyses. The HYDRA module Premium & Incentive Wages was used to calculate incentive wages, while the Access Control module ensured only authorized personnel had site access. The MES HYDRA was successfully deployed across five locations in Germany, Spain, Hungary, and Poland, with plans for a rollout in Mexico.
运营影响
数量效益
Case Study missing?
Start adding your own!
Register with your work email and create a new case study profile for your business.
相关案例.
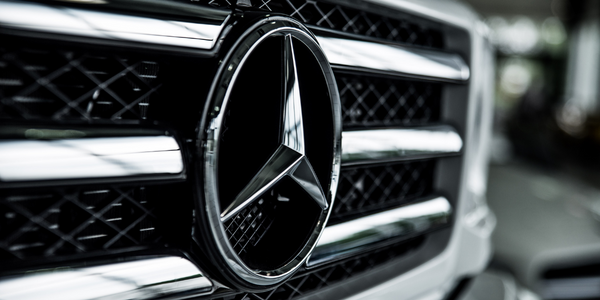
Case Study
Integral Plant Maintenance
Mercedes-Benz and his partner GAZ chose Siemens to be its maintenance partner at a new engine plant in Yaroslavl, Russia. The new plant offers a capacity to manufacture diesel engines for the Russian market, for locally produced Sprinter Classic. In addition to engines for the local market, the Yaroslavl plant will also produce spare parts. Mercedes-Benz Russia and his partner needed a service partner in order to ensure the operation of these lines in a maintenance partnership arrangement. The challenges included coordinating the entire maintenance management operation, in particular inspections, corrective and predictive maintenance activities, and the optimizing spare parts management. Siemens developed a customized maintenance solution that includes all electronic and mechanical maintenance activities (Integral Plant Maintenance).
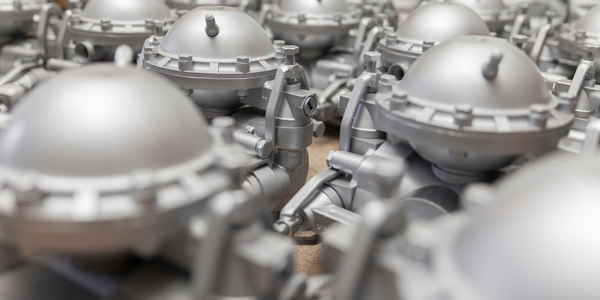
Case Study
Monitoring of Pressure Pumps in Automotive Industry
A large German/American producer of auto parts uses high-pressure pumps to deburr machined parts as a part of its production and quality check process. They decided to monitor these pumps to make sure they work properly and that they can see any indications leading to a potential failure before it affects their process.