公司规模
Large Corporate
地区
- America
国家
- United States
- Canada
产品
- RF-SMART
- ShipHawk
技术栈
- Cloud-based solution
实施规模
- Enterprise-wide Deployment
影响指标
- Productivity Improvements
- Cost Savings
技术
- 功能应用 - 仓库管理系统 (WMS)
适用功能
- 物流运输
- 仓库和库存管理
用例
- 供应链可见性(SCV)
- 库存管理
服务
- 系统集成
关于客户
Greenlane (NASDAQ: GNLN) is a global distributor of accessories for smoke shops, dispensary channels, and wholesale customers. The company's customers include over 6,400 independent smoke shops, regional retail chain stores that operate an estimated 8,000 locations, and hundreds of licensed cannabis cultivators and processors. They also own and operate two of the highest volume direct-to-consumer eCommerce websites in North America. Founded in 2005, Greenlane is a publicly traded company listed on NASDAQ under the ticker symbol GNLN. The company operates in the wholesale distribution industry and uses RF-SMART as its Warehouse Management System (WMS).
挑战
Greenlane, a global distributor of accessories for smoke shops, dispensary channels, and wholesale customers, was facing challenges due to its sustained growth both domestically and internationally. The company had outgrown their previous shipping software which was built for small businesses. The software was locally installed and worked with five other locally installed softwares, making it unmanageable for a company of Greenlane's size. The absence of a streamlined shipping software meant spending time on manual steps that were driving up fulfillment times. Many of Greenlane’s products require domestic and Canadian HAZMAT labels, but there was no automated system for label generation. The team was forced to use a connector software to pass order data over to separate carrier platforms, all to generate a label. Scan-scan-print was no different - the team had been forced to jump between multiple systems which resulted in more wasted time. Greenlane needed a shipping solution that would address their expanding market presence, which was restricted due to the limitations of their previous shipping connector.
解决方案
Greenlane adopted the ShipHawk platform, a comprehensive cloud-based solution that reduced the amount of software they relied upon while improving the efficiency of their fulfillment processes. ShipHawk replaced Greenlane’s previous shipping solution, FedEx Ship Manager, PC Postage, Dazzle, the Canada Post portal, and the Purolator portal. Fulfillment times were dramatically reduced. ShipHawk’s scan-scan-print capabilities dropped processing times by 89% - from 45 seconds to 5 seconds - all by cutting out unnecessary systems in favor of one centralized solution. Automating HAZMAT label generation within ShipHawk means that the team no longer has to jump from a shipping connector to a carrier platform then back to the connector. Now the team can work in one system. ShipHawk also allowed Greenlane to plan for a sustainable, scalable future - including expanding their business internationally. With ShipHawk, Greenlane consolidated their Canadian and domestic volume into a single platform.
运营影响
数量效益
Case Study missing?
Start adding your own!
Register with your work email and create a new case study profile for your business.
相关案例.
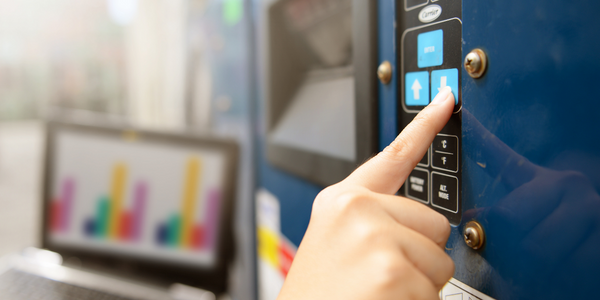
Case Study
Remote Temperature Monitoring of Perishable Goods Saves Money
RMONI was facing temperature monitoring challenges in a cold chain business. A cold chain must be established and maintained to ensure goods have been properly refrigerated during every step of the process, making temperature monitoring a critical business function. Manual registration practice can be very costly, labor intensive and prone to mistakes.
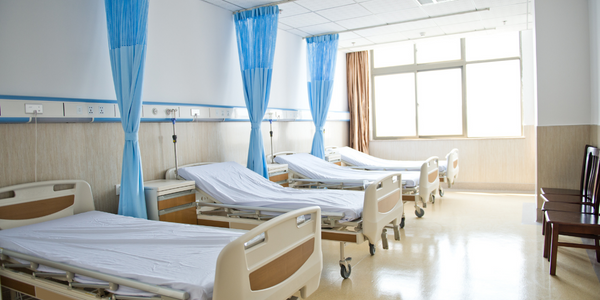
Case Study
Hospital Inventory Management
The hospital supply chain team is responsible for ensuring that the right medical supplies are readily available to clinicians when and where needed, and to do so in the most efficient manner possible. However, many of the systems and processes in use at the cancer center for supply chain management were not best suited to support these goals. Barcoding technology, a commonly used method for inventory management of medical supplies, is labor intensive, time consuming, does not provide real-time visibility into inventory levels and can be prone to error. Consequently, the lack of accurate and real-time visibility into inventory levels across multiple supply rooms in multiple hospital facilities creates additional inefficiency in the system causing over-ordering, hoarding, and wasted supplies. Other sources of waste and cost were also identified as candidates for improvement. Existing systems and processes did not provide adequate security for high-cost inventory within the hospital, which was another driver of cost. A lack of visibility into expiration dates for supplies resulted in supplies being wasted due to past expiry dates. Storage of supplies was also a key consideration given the location of the cancer center’s facilities in a dense urban setting, where space is always at a premium. In order to address the challenges outlined above, the hospital sought a solution that would provide real-time inventory information with high levels of accuracy, reduce the level of manual effort required and enable data driven decision making to ensure that the right supplies were readily available to clinicians in the right location at the right time.