公司规模
Large Corporate
地区
- Europe
- Asia
国家
- Germany
- Portugal
- Thailand
产品
- HYDRA Manufacturing Execution System
- HYDRA Time & Attendance
- HYDRA Access Control
技术栈
- Windows Server
- MS SQL Database
- ERP Interface to SAP
实施规模
- Enterprise-wide Deployment
影响指标
- Productivity Improvements
- Cost Savings
- Digital Expertise
技术
- 功能应用 - 制造执行系统 (MES)
- 应用基础设施与中间件 - 数据交换与集成
适用行业
- 消费品
- 建筑与基础设施
适用功能
- 流程制造
- 质量保证
用例
- 自动化制造系统
- 工厂可见化与智能化
- 过程控制与优化
服务
- 系统集成
- 软件设计与工程服务
关于客户
GROHE AG, marketed under the trademark GROHE, is a leading manufacturer of sanitary fittings, known for its focus on quality, technology, and sustainability. The company employs about 6,000 people worldwide, with significant operations in Germany, Portugal, and Thailand. In 2015, GROHE generated a consolidated revenue of approximately 1.3 billion Euros. The company manufactures products for kitchens, bathrooms, commercial and public sectors, and installation and flushing systems. GROHE's commitment to innovation and excellence has positioned it as a key player in the sanitary fittings industry.
挑战
Producing fittings and fixtures involves several steps such as casting, machining, surface finishing, and final assembly. The challenge was to collect data across the entire processing chain and efficiently plan and control the procedures. The focus was on perfect utilization of tools and machines to avoid unnecessary stockpiling and ensure smooth operations. The need for real-time data collection and evaluation was critical to address malfunctions and bottlenecks promptly.
解决方案
GROHE implemented the HYDRA Manufacturing Execution System (MES) by MPDV across its German sites to manage the production process. The system connects various production stages such as tooling, core molding, casting, machining, electroplating, injection molding, and installation. HYDRA collects data on piece numbers and machine conditions automatically, allowing operators to log orders and reasons for downtimes. The system provides real-time data evaluation and visualization through big screens, enabling operators to react quickly to malfunctions and bottlenecks. The integration of Shop Floor Scheduling and Control ensures optimal utilization of machines and tools without unnecessary stockpiling. Additionally, GROHE uses HYDRA Time & Attendance and Access Control modules to enhance operational efficiency.
运营影响
数量效益
Case Study missing?
Start adding your own!
Register with your work email and create a new case study profile for your business.
相关案例.
.png)
Case Study
Improving Vending Machine Profitability with the Internet of Things (IoT)
The vending industry is undergoing a sea change, taking advantage of new technologies to go beyond just delivering snacks to creating a new retail location. Intelligent vending machines can be found in many public locations as well as company facilities, selling different types of goods and services, including even computer accessories, gold bars, tickets, and office supplies. With increasing sophistication, they may also provide time- and location-based data pertaining to sales, inventory, and customer preferences. But at the end of the day, vending machine operators know greater profitability is driven by higher sales and lower operating costs.
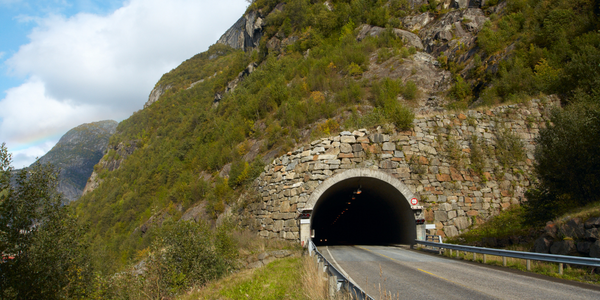
Case Study
IoT System for Tunnel Construction
The Zenitaka Corporation ('Zenitaka') has two major business areas: its architectural business focuses on structures such as government buildings, office buildings, and commercial facilities, while its civil engineering business is targeted at structures such as tunnels, bridges and dams. Within these areas, there presented two issues that have always persisted in regard to the construction of mountain tunnels. These issues are 'improving safety" and "reducing energy consumption". Mountain tunnels construction requires a massive amount of electricity. This is because there are many kinds of electrical equipment being used day and night, including construction machinery, construction lighting, and ventilating fan. Despite this, the amount of power consumption is generally not tightly managed. In many cases, the exact amount of power consumption is only ascertained when the bill from the power company becomes available. Sometimes, corporations install demand-monitoring equipment to help curb the maximum power demanded. However, even in these cases, the devices only allow the total volume of power consumption to be ascertained, or they may issue warnings to prevent the contracted volume of power from being exceeded. In order to tackle the issue of reducing power consumption, it was first necessary to obtain an accurate breakdown of how much power was being used in each particular area. In other words, we needed to be able to visualize the amount of power being consumed. Safety, was also not being managed very rigorously. Even now, tunnel construction sites often use a 'name label' system for managing entry into the work site. Specifically, red labels with white reverse sides that bear the workers' names on both sides are displayed at the tunnel work site entrance. The workers themselves then flip the name label to the appropriate side when entering or exiting from the work site to indicate whether or not they are working inside the tunnel at any given time. If a worker forgets to flip his or her name label when entering or exiting from the tunnel, management cannot be performed effectively. In order to tackle the challenges mentioned above, Zenitaka decided to build a system that could improve the safety of tunnel construction as well as reduce the amount of power consumed. In other words, this new system would facilitate a clear picture of which workers were working in each location at the mountain tunnel construction site, as well as which processes were being carried out at those respective locations at any given time. The system would maintain the safety of all workers while also carefully controlling the electrical equipment to reduce unnecessary power consumption. Having decided on the concept, our next concern was whether there existed any kind of robust hardware that would not break down at the construction work site, that could move freely in response to changes in the working environment, and that could accurately detect workers and vehicles using radio frequency identification (RFID). Given that this system would involve many components that were new to Zenitaka, we decided to enlist the cooperation of E.I.Sol Co., Ltd. ('E.I.Sol') as our joint development partner, as they had provided us with a highly practical proposal.
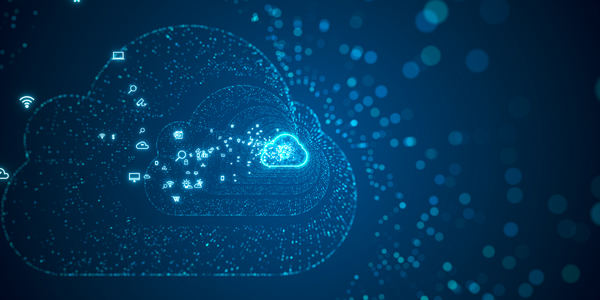
Case Study
Splunk Partnership Ties Together Big Data & IoT Services
Splunk was faced with the need to meet emerging customer demands for interfacing IoT projects to its suite of services. The company required an IoT partner that would be able to easily and quickly integrate with its Splunk Enterprise platform, rather than allocating development resources and time to building out an IoT interface and application platform.
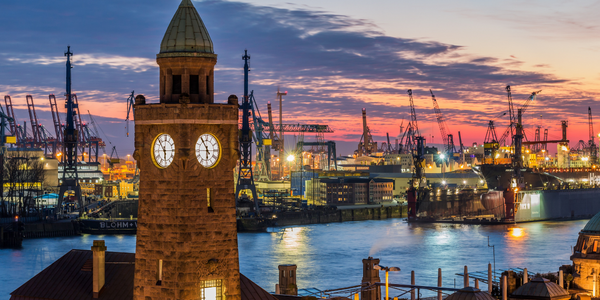
Case Study
Bridge monitoring in Hamburg Port
Kattwyk Bridge is used for both rail and road transport, and it has played an important role in the Port of Hamburg since 1973. However, the increasing pressure from traffic requires a monitoring solution. The goal of the project is to assess in real-time the bridge's status and dynamic responses to traffic and lift processes.