技术
- 执行器 - 液压执行器
- 传感器 - 电表
适用行业
- 城市与自治市
- 石油和天然气
适用功能
- 维护
- 产品研发
用例
- 数字孪生
- 智慧城市供水管理
服务
- 系统集成
- 测试与认证
关于客户
ATLC 基础设施咨询私人有限公司Ltd. 是一家私营公司,承包设计一个项目,旨在为印度北方邦 Mirzapur 的 Marihan 街区的 128 个村庄开发管道供水系统。该项目由州政府发起,旨在改善 30 万居民和重要印度教寺庙 Vindhachal Dham 的众多游客的生活质量。该公司面临的挑战是设计一个系统,该系统至少能够在 2053 年之前持续运行并适应人口增长,并满足州法规的要求。该项目需要扩建现有的水处理厂、水处理厂内的一个新泵站、四个额外的水泵站和 12 个配水库,以及数公里长的输配电干线和带有水表的房屋连接。
挑战
印度北方邦政府启动了一个开发管道供水系统的项目,以确保将处理后的水平等分配到米尔扎普尔 Marihan 街区的所有 128 个村庄。该项目旨在改善 300,000 名居民以及重要印度教寺庙 Vindhachal Dham 的众多游客的生活质量。 ATLC 基础设施咨询私人有限公司有限公司负责设计该项目,该项目需要至少到 2053 年继续运营并适应人口增长,并满足国家法规。该项目需要扩建现有的水处理厂、水处理厂内的一个新泵站、四个额外的水泵站和 12 个配水库,以及数公里长的输配电干线和带有水表的房屋连接。设计团队面临着全面了解起伏地形(高度变化高达 140 米)并提供替代路线走线建议的挑战。他们还努力分析设计变更对水压的影响,并使用他们使用的旧工具满足所需的 90 天期限。
解决方案
ATLC 基础设施咨询私人有限公司Ltd. 决定使用 OpenFlows WaterGEMS 和 STAAD 来无缝设计网络并进行水力分析。详细的水力分析揭示了地下水位的确切状态,这有助于他们确定需要在哪里建设资产以及如何确保清洁的水。使用 OpenFlows WaterGEMS,设计团队整合了现场数据,并根据需要进行更新的水力分析,以优化设计,确保其安全性和可靠性。该分析包括对供水的完整评估、均衡分配的压力分区以及确定家庭连接的最有效分配。通过 STAAD,ATLC 优化了进水井、高架配水库和水处理厂的结构设计。他们构建了整个工作区域的数字孪生,清晰地可视化了项目的范围和细节,帮助他们与项目利益相关者分享他们的工作。
运营影响
数量效益
Case Study missing?
Start adding your own!
Register with your work email and create a new case study profile for your business.
相关案例.
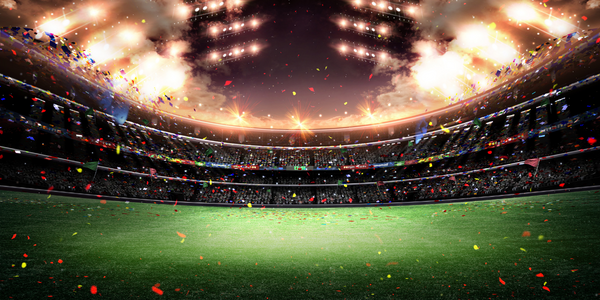
Case Study
Turning A Stadium Into A Smart Building
Honeywell created what it called the “intelligent system” for the National Stadium in Beijing, China, turning the venue for the opening and closing events at the 2008 Summer Olympics into a “smart building.” Designed by highly controversial artist Ai Weiwei, the “Bird’s Nest” remains one of the most impressive feats of stadium architecture in the world. The 250,000 square meter structure housed more than 100,000 athletes and spectators at a time. To accommodate such capacity, China turned to Honeywell’s EBI Integrated Building Management System to create an integrated “intelligent system” for improved building security, safety and energy efficiency.
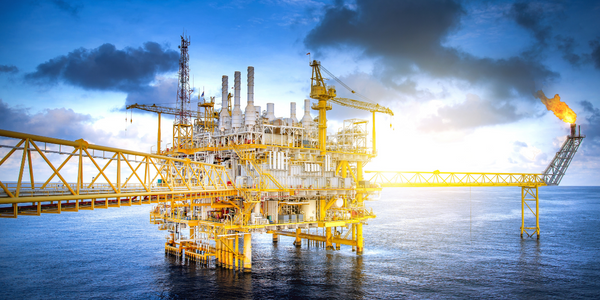
Case Study
Taking Oil and Gas Exploration to the Next Level
DownUnder GeoSolutions (DUG) wanted to increase computing performance by 5 to 10 times to improve seismic processing. The solution must build on current architecture software investments without sacrificing existing software and scale computing without scaling IT infrastructure costs.
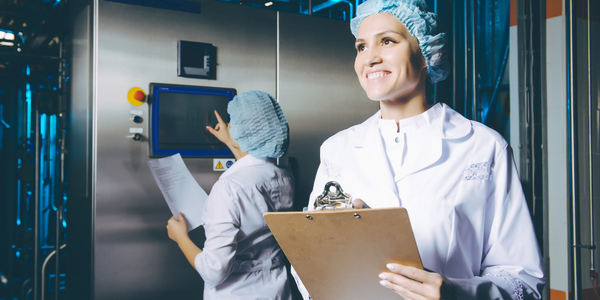
Case Study
Remote Wellhead Monitoring
Each wellhead was equipped with various sensors and meters that needed to be monitored and controlled from a central HMI, often miles away from the assets in the field. Redundant solar and wind generators were installed at each wellhead to support the electrical needs of the pumpstations, temperature meters, cameras, and cellular modules. In addition to asset management and remote control capabilities, data logging for remote surveillance and alarm notifications was a key demand from the customer. Terra Ferma’s solution needed to be power efficient, reliable, and capable of supporting high-bandwidth data-feeds. They needed a multi-link cellular connection to a central server that sustained reliable and redundant monitoring and control of flow meters, temperature sensors, power supply, and event-logging; including video and image files. This open-standard network needed to interface with the existing SCADA and proprietary network management software.
.png)
Case Study
Smart Street Light Network (Copenhagen)
Key stakeholders are taking a comprehensive approach to rethinking smart city innovation. City leaders have collaborated through partnerships involving government, research institutions and solution providers. The Copenhagen Solutions Lab is one of the leading organizations at the forefront of this movement. By bringing together manufacturers with municipal buyers, the Copenhagen Solutions Lab has catalyzed the development and deployment of next-generation smart city innovations. Copenhagen is leveraging this unique approach to accelerate the implementation of smart city solutions. One of the primary focus areas is LED street lighting.
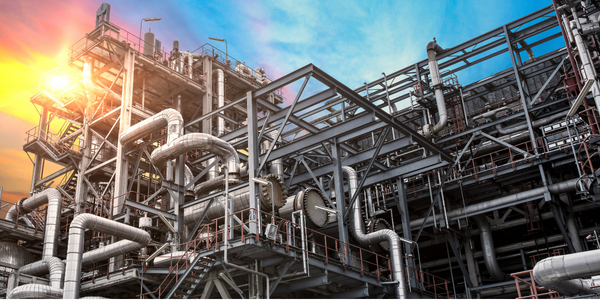
Case Study
Refinery Saves Over $700,000 with Smart Wireless
One of the largest petroleum refineries in the world is equipped to refine various types of crude oil and manufacture various grades of fuel from motor gasoline to Aviation Turbine Fuel. Due to wear and tear, eight hydrogen valves in each refinery were leaking, and each cost $1800 per ton of hydrogen vented. The plant also had leakage on nearly 30 flare control hydrocarbon valves. The refinery wanted a continuous, online monitoring system that could catch leaks early, minimize hydrogen and hydrocarbon production losses, and improve safety for maintenance.