公司规模
SME
地区
- America
国家
- United States
产品
- Hyper Racing chassis
- Micro sprint race cars
- Fuel injection systems
- Parts/accessories
技术栈
- NetSuite
- ShipHawk
实施规模
- Enterprise-wide Deployment
影响指标
- Productivity Improvements
- Cost Savings
- Customer Satisfaction
技术
- 功能应用 - 企业资源规划系统 (ERP)
适用行业
- 汽车
适用功能
- 物流运输
- 仓库和库存管理
用例
- 库存管理
- 车队管理
服务
- 系统集成
关于客户
Hyper Racing is a company that specializes in the production of micro sprint race cars, fuel injection systems, and parts/accessories. The company was incorporated in 1994 by Mike Dicely and his wife, Christy, who had extensive micro sprint racing experience. The company's growth accelerated in 2018 and throughout the COVID-19 pandemic as consumers looked for outdoor recreational sports. Many NASCAR drivers use Hyper Racing’s class of cars to keep their skills sharp in between races. The company operates three warehouses and handles approximately 8,000 SKUs.
挑战
Hyper Racing, a company that sells micro sprint race cars, fuel injection systems, and parts/accessories, was facing a challenge in its shipping process. With three warehouses and approximately 8,000 SKUs, the company needed an advanced shipping solution to increase productivity and reduce shipping costs without hiring more employees. The weights and dimensions of Hyper Racing’s products are incredibly varied, and the small warehouse team had to rush through the packing process, often grabbing whatever carton they knew would fit the contents of the order just to get it out the door faster. Another challenge was that there wasn’t enough time to accurately and manually rate shop shipping options for the hundreds of packages shipped per day. As a result, Hyper Racing was often paying for more expensive carriers or an unnecessary shipping method.
解决方案
Hyper Racing implemented ShipHawk’s solution to automate and upgrade the company’s operation. By automatically calculating the final packed dimensions and weight for each order, the solution improves the customer experience and expedites order processing. The solution also integrates seamlessly with Hyper Racing's ERP, NetSuite, which allows order details to automatically sync back to NetSuite, saving the warehouse team time from inputting order details in a system and then double-checking that everything is correct. To improve the customer experience, Hyper Racing took advantage of in-cart rating to ensure customers are always seeing the most accurate shipping rates within the shopping cart in real-time.
运营影响
Case Study missing?
Start adding your own!
Register with your work email and create a new case study profile for your business.
相关案例.
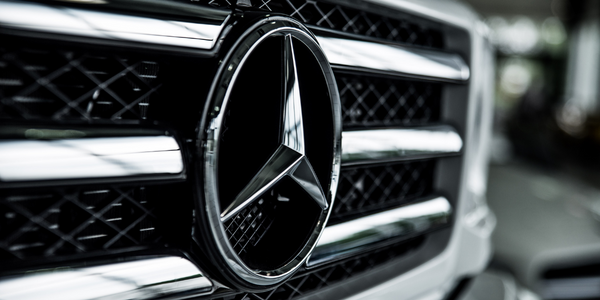
Case Study
Integral Plant Maintenance
Mercedes-Benz and his partner GAZ chose Siemens to be its maintenance partner at a new engine plant in Yaroslavl, Russia. The new plant offers a capacity to manufacture diesel engines for the Russian market, for locally produced Sprinter Classic. In addition to engines for the local market, the Yaroslavl plant will also produce spare parts. Mercedes-Benz Russia and his partner needed a service partner in order to ensure the operation of these lines in a maintenance partnership arrangement. The challenges included coordinating the entire maintenance management operation, in particular inspections, corrective and predictive maintenance activities, and the optimizing spare parts management. Siemens developed a customized maintenance solution that includes all electronic and mechanical maintenance activities (Integral Plant Maintenance).
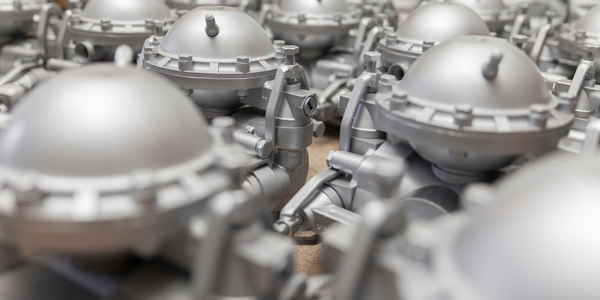
Case Study
Monitoring of Pressure Pumps in Automotive Industry
A large German/American producer of auto parts uses high-pressure pumps to deburr machined parts as a part of its production and quality check process. They decided to monitor these pumps to make sure they work properly and that they can see any indications leading to a potential failure before it affects their process.