公司规模
SME
地区
- America
国家
- United States
产品
- E2 Shop System
技术栈
- Cloud Service
实施规模
- Enterprise-wide Deployment
影响指标
- Productivity Improvements
- Revenue Growth
技术
- 平台即服务 (PaaS) - 应用开发平台
适用功能
- 离散制造
用例
- 自动化制造系统
服务
- 云规划/设计/实施服务
关于客户
HTS Coatings, Inc. 是一家位于圣路易斯的金属涂层公司。该公司由 Jason 和 Ashley Hunsaker 于 2015 年创立,当时当地一家公司即将倒闭,他们决定进军金属涂层业务。他们购买了这家倒闭公司的部分设备,搬到了新大楼,并在短短几个月内成立了 HTS Coatings, Inc.。HTS Coatings, Inc. 的首席财务官 Ashley 在为他们的业务寻找合适的车间规划和管理软件方面发挥了重要作用。
挑战
HTS Coatings, Inc. 是一家金属涂层企业,需要一款价格合理、用户友好且购买后可立即使用的车间规划和管理软件。该公司刚刚成立,创始人 Ashley 和 Jason Hunsaker 一边努力让公司起步,一边照顾新生儿的需求。他们需要一款软件解决方案,只需进行最少的定制,即可帮助他们提高生产力并增加收入。
解决方案
HTS Coatings, Inc. 选择实施 E2 Shop System,这是一款车间规划和管理软件。该软件易于使用,只需极少的定制,非常适合公司。他们还实施了一项名为“收益分享计划”的员工激励计划,该计划使用 E2 的报告模块来跟踪和详细说明每个员工和工作的时间和准确性。在比预期更短的时间内完成任务并为公司节省资金的员工将获得相应级别和奖金。该公司还改用 E2 云服务来改善准时交付和客户沟通。
运营影响
数量效益
Case Study missing?
Start adding your own!
Register with your work email and create a new case study profile for your business.
相关案例.
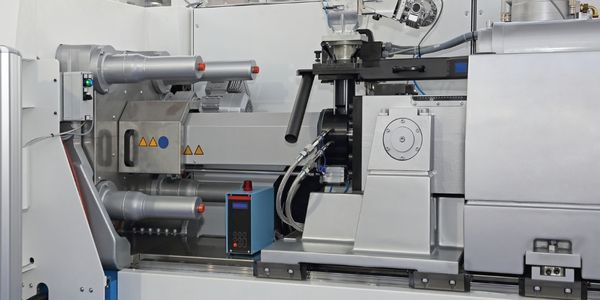
Case Study
Plastic Spoons Case study: Injection Moulding
In order to meet customer expectations by supplying a wide variety of packaging units, from 36 to 1000 spoons per package, a new production and packaging line needed to be built. DeSter wanted to achieve higher production capacity, lower cycle time and a high degree of operator friendliness with this new production line.
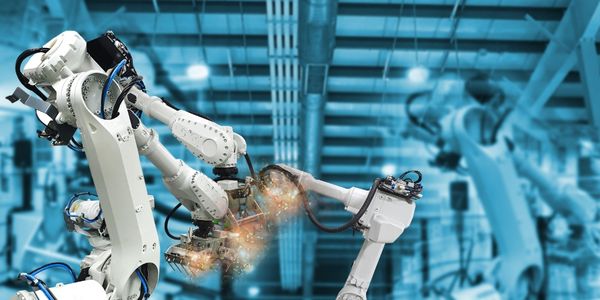
Case Study
Robot Saves Money and Time for US Custom Molding Company
Injection Technology (Itech) is a custom molder for a variety of clients that require precision plastic parts for such products as electric meter covers, dental appliance cases and spools. With 95 employees operating 23 molding machines in a 30,000 square foot plant, Itech wanted to reduce man hours and increase efficiency.
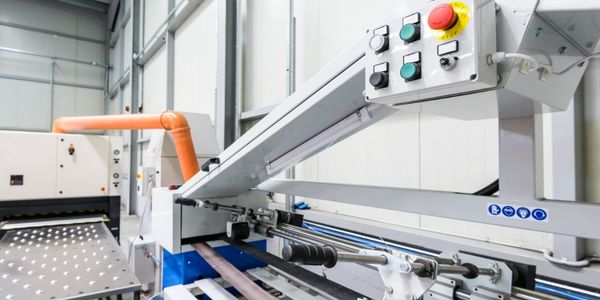
Case Study
Fully Automated Visual Inspection System
Tofflon has developed a fully automatic machine that uses light to inspect vials, medicine bottles, or infusion containers for glass fragments, aluminum particles, rubber grains, hairs, fibers, or other contaminants. It also detects damaged containers with cracks or inclusions (microscopic imperfections), automatically removing faulty or contaminated products. In order to cover all production processes for freeze-dried pharmaceuticals, Tofflon needed to create an open, consistent, and module-based automation concept.
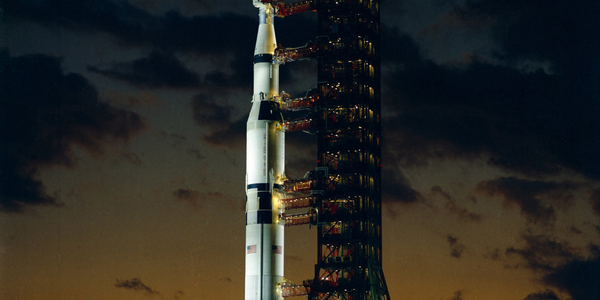
Case Study
SAP Leonardo Enabling Rocket Science
At times, ULA has as many as 15 different operating systems dedicated to overlapping processes, such as rocket design, testing, and launch. Multiple systems created unnecessary costs and unwanted confusion among workers at offices, factories, and launch sites in different location. In order to improve collaboration and transparency during vital activities that directly influence mission success, ULA wanted to improve data sharing and streamline manufacturing processes.
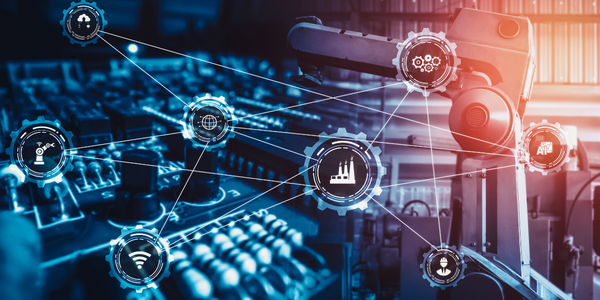
Case Study
IIC Smart Manufacturing Connectivity for Brown-field Sensors
The discrete manufacturing domain is characterized by a strictly hierarchical structure of the automation systems, commonly referred to as the automation pyramid. Data acquired by a sensor typically flows through an IO-module into a Programmable Logic Controller (PLC) which manages the local real-time control system. As all process data are concentrated in the PLC, re-programming the PLC and thus, implementing interfaces to access these data appear to be the natural choice to transfer them to the IT system. However, for brownfield installations this choice has proven impracticable for the following two reasons:In brownfield facilities, PLC usually operate within a once-specified environment and are rarely re-programmed. That is why the active staff is often not familiar with the code and lacks of the competence to modify the existing implementation in a reasonable amount of time.Furthermore, for cost reasons, any PLC was selected to exactly match the requirements of the environment within which it was intended to operate. That is why it cannot be assumed that a PLC will be able to support additional tasks such as communicating data through additional interfaces.
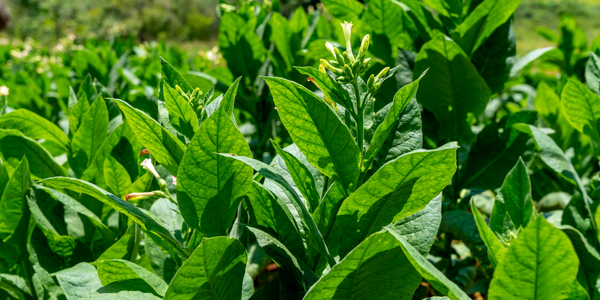
Case Study
Smart Factory Solutions for Tobacco Industries: Bridging the Manufacturing Generation Gap and Improving Operational Efficiency
The tobacco industry, represented in this case by British American Tobacco (BAT), is facing a decline in cigarette volumes worldwide. This decline has led to an increased emphasis on efficient supply chains and optimized production processes. The industry is also grappling with the need for agile production facilities and the integration of Industry 4.0 to accommodate diverse production requirements. BAT, in particular, was seeking a factory solution to automate their product control processes, from the transportation of tobacco and cigarette paper to the placement on cigarette machines and the packing conveyor. The company also needed to support the continuous use of legacy equipment, such as relay-controlled cigarette machines dating back to the 90s and AMK servo drive systems, to sustain production levels at speeds of 8000 to 16000 pieces per minute. Furthermore, changing regulatory guidelines necessitated flexibility in labeling requirements.