公司规模
Large Corporate
地区
- America
国家
- United States
产品
- Sage 500 ERP
- Sage SalesLogix
- Sage HRMS
- Sage Sales Tax
技术栈
- SQL Database
实施规模
- Enterprise-wide Deployment
影响指标
- Productivity Improvements
- Cost Savings
技术
- 功能应用 - 企业资源规划系统 (ERP)
适用功能
- 离散制造
- 采购
用例
- 自动化制造系统
- 库存管理
服务
- 系统集成
关于客户
75 多年来,Nashville Wire Products 一直致力于设计和制造焊接线材产品。纵观公司的发展历程,公司不断扩大业务规模并实现业务多元化,进军多个市场,服务数千家客户。如今,公司收入超过 9000 万美元,其三个部门每年出货数百万件产品。尖端技术、优质产品和无与伦比的服务使 Nashville Wire Products 在其服务的所有市场中占据领先地位。这家家族企业始终将技术作为提高效率和发展业务的工具,现在将其运营委托给 Sage 500 ERP。
挑战
Nashville Wire Products 公司正在使用高度定制的 ProfitKey 版本,这是一款 ERP 和制造应用程序。事实证明,该系统的维护和支持成本高昂,而且很难从中获取数据和运营指标。该技术既陈旧又繁琐,不够灵活,无法支持其快节奏的运营。内部项目团队分析了可用的选项,包括 Sage 500 ERP、Microsoft Dynamics AX 和 Microsoft Dynamics NV。他们选择 Sage 500 ERP 的原因有很多,包括它提供的更直观的界面和强大的业务合作伙伴支持。
解决方案
Sage 500 ERP 被选为运营的骨干,Sage SalesLogix、Sage HRMS 和 Sage Sales Tax 则作为配套解决方案。Sage 500 ERP 及其配套产品采用的行业标准 SQL 数据库为公司带来了显著优势。他们能够从七八个单独的数据库(分别保存制造、客户和财务数据)转移到一个可访问、稳定且易于管理的集成数据库。Business Insights Explorer 模块通过提供在整个企业范围内快速查询数据的功能,帮助使数据可访问。
运营影响
数量效益
Case Study missing?
Start adding your own!
Register with your work email and create a new case study profile for your business.
相关案例.
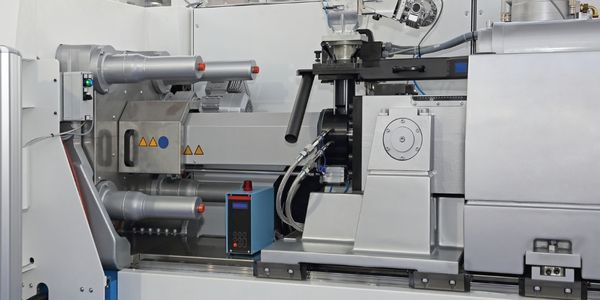
Case Study
Plastic Spoons Case study: Injection Moulding
In order to meet customer expectations by supplying a wide variety of packaging units, from 36 to 1000 spoons per package, a new production and packaging line needed to be built. DeSter wanted to achieve higher production capacity, lower cycle time and a high degree of operator friendliness with this new production line.
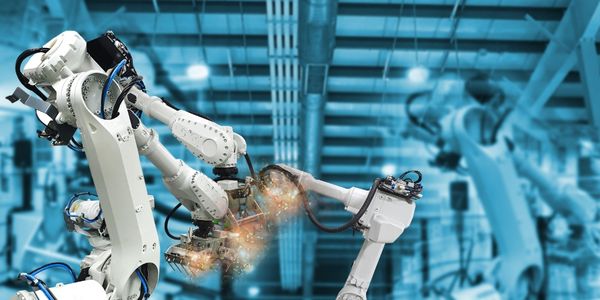
Case Study
Robot Saves Money and Time for US Custom Molding Company
Injection Technology (Itech) is a custom molder for a variety of clients that require precision plastic parts for such products as electric meter covers, dental appliance cases and spools. With 95 employees operating 23 molding machines in a 30,000 square foot plant, Itech wanted to reduce man hours and increase efficiency.
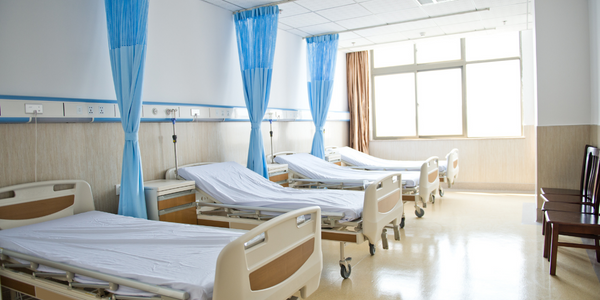
Case Study
Hospital Inventory Management
The hospital supply chain team is responsible for ensuring that the right medical supplies are readily available to clinicians when and where needed, and to do so in the most efficient manner possible. However, many of the systems and processes in use at the cancer center for supply chain management were not best suited to support these goals. Barcoding technology, a commonly used method for inventory management of medical supplies, is labor intensive, time consuming, does not provide real-time visibility into inventory levels and can be prone to error. Consequently, the lack of accurate and real-time visibility into inventory levels across multiple supply rooms in multiple hospital facilities creates additional inefficiency in the system causing over-ordering, hoarding, and wasted supplies. Other sources of waste and cost were also identified as candidates for improvement. Existing systems and processes did not provide adequate security for high-cost inventory within the hospital, which was another driver of cost. A lack of visibility into expiration dates for supplies resulted in supplies being wasted due to past expiry dates. Storage of supplies was also a key consideration given the location of the cancer center’s facilities in a dense urban setting, where space is always at a premium. In order to address the challenges outlined above, the hospital sought a solution that would provide real-time inventory information with high levels of accuracy, reduce the level of manual effort required and enable data driven decision making to ensure that the right supplies were readily available to clinicians in the right location at the right time.
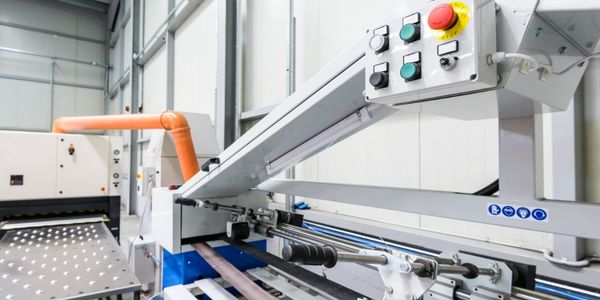
Case Study
Fully Automated Visual Inspection System
Tofflon has developed a fully automatic machine that uses light to inspect vials, medicine bottles, or infusion containers for glass fragments, aluminum particles, rubber grains, hairs, fibers, or other contaminants. It also detects damaged containers with cracks or inclusions (microscopic imperfections), automatically removing faulty or contaminated products. In order to cover all production processes for freeze-dried pharmaceuticals, Tofflon needed to create an open, consistent, and module-based automation concept.
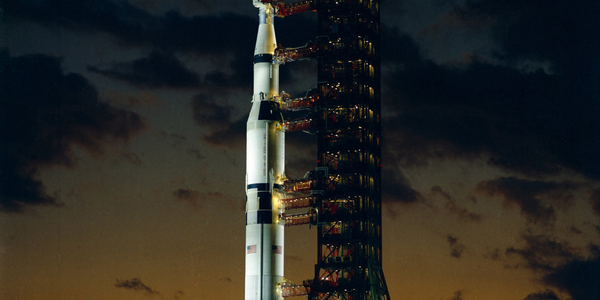
Case Study
SAP Leonardo Enabling Rocket Science
At times, ULA has as many as 15 different operating systems dedicated to overlapping processes, such as rocket design, testing, and launch. Multiple systems created unnecessary costs and unwanted confusion among workers at offices, factories, and launch sites in different location. In order to improve collaboration and transparency during vital activities that directly influence mission success, ULA wanted to improve data sharing and streamline manufacturing processes.