公司规模
Mid-size Company
地区
- America
国家
- United States
产品
- Rootstock Cloud ERP
- Salesforce CRM
- FinancialForce
- Box.com
技术栈
- Cloud Computing
- Salesforce Platform
实施规模
- Enterprise-wide Deployment
影响指标
- Productivity Improvements
- Customer Satisfaction
- Digital Expertise
技术
- 平台即服务 (PaaS) - 应用开发平台
- 平台即服务 (PaaS) - 数据管理平台
适用功能
- 离散制造
- 销售与市场营销
用例
- 自动化制造系统
- 预测性维护
服务
- 云规划/设计/实施服务
- 软件设计与工程服务
关于客户
Pioneer Motor Bearing Co. 是一家由第四代家族经营的企业,提供交钥匙设计和升级服务,擅长快速响应、紧急维修油膜轴承,产品范围从最新的美国海军舰艇到核蒸汽涡轮机。该公司的客户包括通用电气、西门子、西屋电气、东芝、三菱日立等领先的原始设备制造商。Pioneer 还为美国大多数公共和私营电力公司提供服务,例如杜克能源、太平洋天然气和电力公司、南方电力公司、洛杉矶水电局、佐治亚电力公司和 TVA。
挑战
Pioneer Motor Bearing 是一家家族企业,100 年来一直致力于为发电和工业市场维修、制造和设计油膜轴承,该公司一直在努力寻找内部部署 ERP 解决方案。该系统无法提供客户的 360 度视图,而这对于改善客户关系和快速访问相关信息至关重要。该公司正在寻找一种简化的订单处理系统,可以无缝地从 RFQ 过渡到报价再到销售订单。但是,他们的内部部署 ERP 系统要求他们重新输入所有相同的产品信息。估算是 Pioneer 车间环境中的一个关键过程,但仍然需要大量的手动流程,并且无法在一个地方捕获历史客户信息。报告是另一个问题。该公司意识到,仅仅为了保持其内部部署 ERP 系统处于活动状态,就需要进行大量的实施工作并中断其业务。
解决方案
Pioneer 决定将其业务系统迁移到云端,特别是 Salesforce 平台。他们之所以选择 Rootstock Cloud ERP,是因为它与 Salesforce 兼容,并且能够支持他们的业务。Rootstock 能够处理每一种制造模式和操作环境,尤其是车间的需求,这对 Pioneer 来说尤其有吸引力。该公司还欣赏 Rootstock 易于定制的特点。自 2015 年实施 Rootstock Cloud ERP 以来,Pioneer 一直在使用其许多模块,包括销售订单、销售订单履行、销售订单开票、工单、工单操作、工作中心、劳动力预订、车间调度、采购订单、信用备忘录和库存管理。该公司还使用 Rootstock 工程和项目控制。Pioneer 还根据自己的特定需求构建了自己的应用程序,例如劳动力预订应用程序、质量管理应用程序和估算引擎。
运营影响
数量效益
Case Study missing?
Start adding your own!
Register with your work email and create a new case study profile for your business.
相关案例.

Case Study
Remote Monitoring & Predictive Maintenance App for a Solar Energy System
The maintenance & tracking of various modules was an overhead for the customer due to the huge labor costs involved. Being an advanced solar solutions provider, they wanted to ensure early detection of issues and provide the best-in-class customer experience. Hence they wanted to automate the whole process.
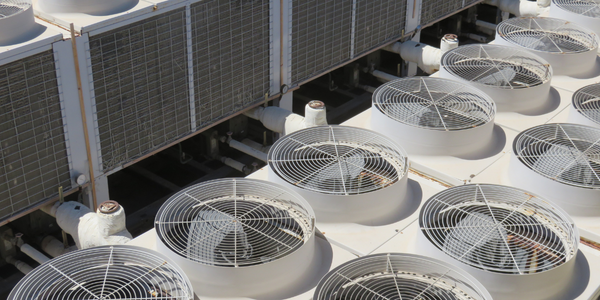
Case Study
Predictive Maintenance for Industrial Chillers
For global leaders in the industrial chiller manufacturing, reliability of the entire production process is of the utmost importance. Chillers are refrigeration systems that produce ice water to provide cooling for a process or industrial application. One of those leaders sought a way to respond to asset performance issues, even before they occur. The intelligence to guarantee maximum reliability of cooling devices is embedded (pre-alarming). A pre-alarming phase means that the cooling device still works, but symptoms may appear, telling manufacturers that a failure is likely to occur in the near future. Chillers who are not internet connected at that moment, provide little insight in this pre-alarming phase.
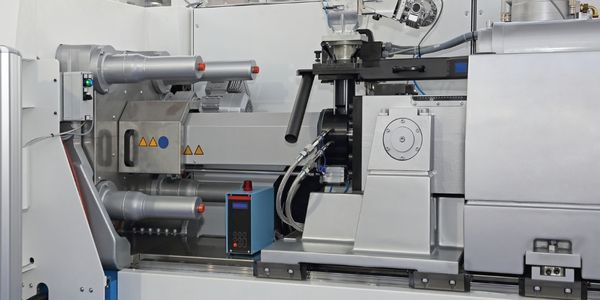
Case Study
Plastic Spoons Case study: Injection Moulding
In order to meet customer expectations by supplying a wide variety of packaging units, from 36 to 1000 spoons per package, a new production and packaging line needed to be built. DeSter wanted to achieve higher production capacity, lower cycle time and a high degree of operator friendliness with this new production line.
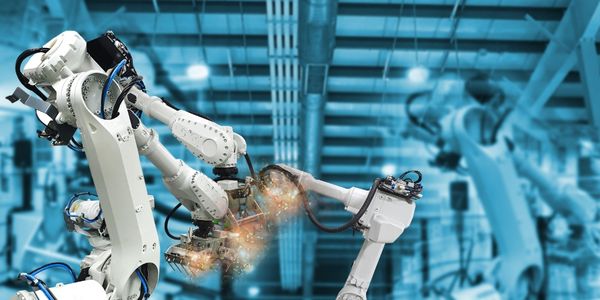
Case Study
Robot Saves Money and Time for US Custom Molding Company
Injection Technology (Itech) is a custom molder for a variety of clients that require precision plastic parts for such products as electric meter covers, dental appliance cases and spools. With 95 employees operating 23 molding machines in a 30,000 square foot plant, Itech wanted to reduce man hours and increase efficiency.
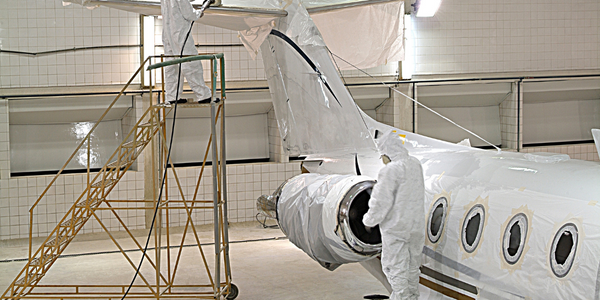
Case Study
Aircraft Predictive Maintenance and Workflow Optimization
First, aircraft manufacturer have trouble monitoring the health of aircraft systems with health prognostics and deliver predictive maintenance insights. Second, aircraft manufacturer wants a solution that can provide an in-context advisory and align job assignments to match technician experience and expertise.
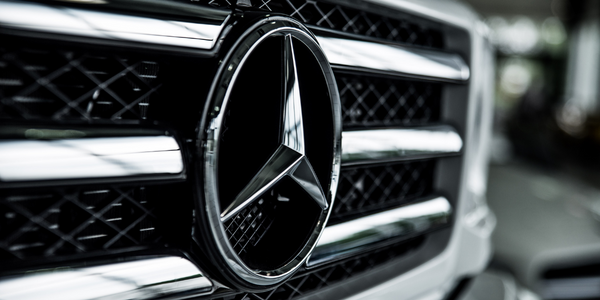
Case Study
Integral Plant Maintenance
Mercedes-Benz and his partner GAZ chose Siemens to be its maintenance partner at a new engine plant in Yaroslavl, Russia. The new plant offers a capacity to manufacture diesel engines for the Russian market, for locally produced Sprinter Classic. In addition to engines for the local market, the Yaroslavl plant will also produce spare parts. Mercedes-Benz Russia and his partner needed a service partner in order to ensure the operation of these lines in a maintenance partnership arrangement. The challenges included coordinating the entire maintenance management operation, in particular inspections, corrective and predictive maintenance activities, and the optimizing spare parts management. Siemens developed a customized maintenance solution that includes all electronic and mechanical maintenance activities (Integral Plant Maintenance).