公司规模
Large Corporate
国家
- Worldwide
产品
- Intelex’s safety management applications
- Audit Management
- Incident Management
- Job Safety Analysis
- Permits Management
- Training Management
技术栈
- AI
- Data Analysis
- Mobile Application
实施规模
- Enterprise-wide Deployment
影响指标
- Employee Satisfaction
- Productivity Improvements
技术
- 应用基础设施与中间件 - 数据交换与集成
适用行业
- 化学品
- 医疗保健和医院
适用功能
- 离散制造
- 质量保证
用例
- 预测性维护
- 资产健康管理 (AHM)
- 计算机视觉
服务
- 数据科学服务
- 系统集成
关于客户
Linde is a global company with a reputation for supporting industrial excellence and creating sustainable solutions. With over 140 years of technology innovation, Linde's mission is to make the world more productive and sustainable. The company's expertise touches almost every part of modern technology innovation, including clean hydrogen and carbon capture systems to support the energy transition, life-saving medical gases and specialty gases for electronics, as well as engineering solutions for the hydrocarbon industry. Linde operates over 2,000 sites in more than 100 countries around the world with over 70,000 employees and $33 billion in sales in 2022. After merging with Praxair in 2019, Linde added solutions and material production serving the aviation, energy, industrial and emerging applications industries. It also added 30 plants in 11 countries with more than 2,300 employees to its organisation.
挑战
Linde, a global company with over 2,000 sites in more than 100 countries and over 70,000 employees, faced the challenge of creating a unified safety culture. The company's size and diversity made it difficult to ensure that all employees embraced safety and recognized the importance of reporting incidents. Following the merger with Praxair in 2019, Linde had to deal with several legacy systems, making it difficult to get benchmark KPIs when different systems were used in different business units. The company needed a system that could be used by frontline employees and that would encourage them to report incidents, no matter how small. Linde also wanted to support the business units with advanced data analysis to improve safety across the organization and to direct resources for continuous improvement.
解决方案
To meet its safety culture challenge, Linde turned to Intelex’s safety management applications. The main objective was to get acceptance for a global system that could be used by frontline employees. Linde’s safety management system is supported by an extensive collection of Intelex applications, including Audit Management, Incident Management, Job Safety Analysis, Permits Management and Training Management. The flexibility this collection of applications provides was a key factor in selecting Intelex. The critical role of the frontline worker at Linde meant that it was important they could enter incident data directly into a mobile application, even without an Internet connection. Once that data has been entered into the system, Linde uses Predictive Solutions applications to perform innovative data analysis that allows them to produce reports and communications they hadn’t been able to produce in the past.
运营影响
数量效益
Case Study missing?
Start adding your own!
Register with your work email and create a new case study profile for your business.
相关案例.
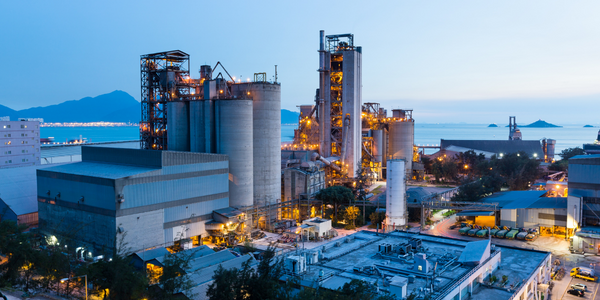
Case Study
Honeywell - Tata Chemicals Improves Data Accessibility with OneWireless
Tata was facing data accessibility challenges in the cement plant control room tapping signals from remote process control areas and other distant locations, including the gas scrubber. Tata needed a wireless solution to extend its control network securely to remote locations that would also provide seamless communication with existing control applications.
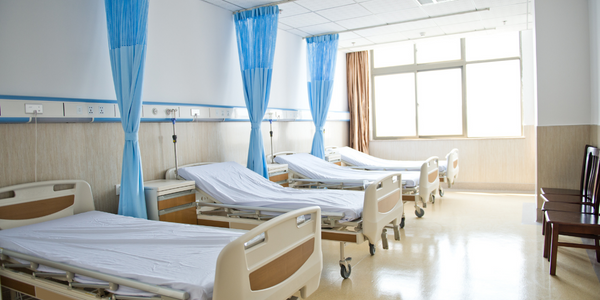
Case Study
Hospital Inventory Management
The hospital supply chain team is responsible for ensuring that the right medical supplies are readily available to clinicians when and where needed, and to do so in the most efficient manner possible. However, many of the systems and processes in use at the cancer center for supply chain management were not best suited to support these goals. Barcoding technology, a commonly used method for inventory management of medical supplies, is labor intensive, time consuming, does not provide real-time visibility into inventory levels and can be prone to error. Consequently, the lack of accurate and real-time visibility into inventory levels across multiple supply rooms in multiple hospital facilities creates additional inefficiency in the system causing over-ordering, hoarding, and wasted supplies. Other sources of waste and cost were also identified as candidates for improvement. Existing systems and processes did not provide adequate security for high-cost inventory within the hospital, which was another driver of cost. A lack of visibility into expiration dates for supplies resulted in supplies being wasted due to past expiry dates. Storage of supplies was also a key consideration given the location of the cancer center’s facilities in a dense urban setting, where space is always at a premium. In order to address the challenges outlined above, the hospital sought a solution that would provide real-time inventory information with high levels of accuracy, reduce the level of manual effort required and enable data driven decision making to ensure that the right supplies were readily available to clinicians in the right location at the right time.

Case Study
Advanced Elastomer Systems Upgrades Production
In order to maintain its share of the international market for thermoplastic elastomers AES recently expanded its Florida plant by adding a new production line. While the existing lines were operating satisfactorily using a PROVOX distributed control system with traditional analog I/O, AES wanted advanced technology on the new line for greater economy, efficiency, and reliability. AES officials were anxious to get this line into production to meet incoming orders, but two hurricanes slowed construction.
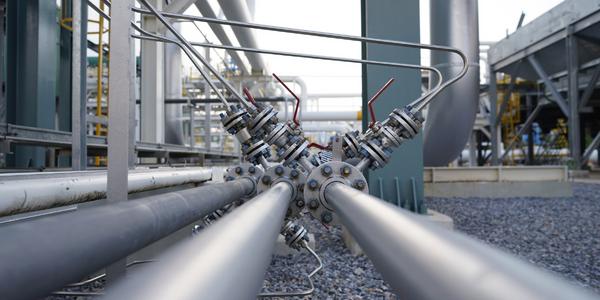
Case Study
Gas Pipeline Monitoring System for Hospitals
This system integrator focuses on providing centralized gas pipeline monitoring systems for hospitals. The service they provide makes it possible for hospitals to reduce both maintenance and labor costs. Since hospitals may not have an existing network suitable for this type of system, GPRS communication provides an easy and ready-to-use solution for remote, distributed monitoring systems System Requirements - GPRS communication - Seamless connection with SCADA software - Simple, front-end control capability - Expandable I/O channels - Combine AI, DI, and DO channels
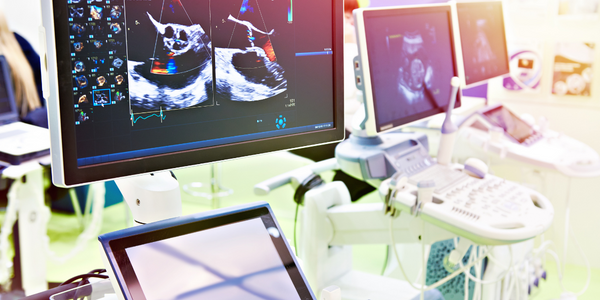
Case Study
Driving Digital Transformations for Vitro Diagnostic Medical Devices
Diagnostic devices play a vital role in helping to improve healthcare delivery. In fact, an estimated 60 percent of the world’s medical decisions are made with support from in vitrodiagnostics (IVD) solutions, such as those provided by Roche Diagnostics, an industry leader. As the demand for medical diagnostic services grows rapidly in hospitals and clinics across China, so does the market for IVD solutions. In addition, the typically high cost of these diagnostic devices means that comprehensive post-sales services are needed. Wanteed to improve three portions of thr IVD:1. Remotely monitor and manage IVD devices as fixed assets.2. Optimizing device availability with predictive maintenance.3. Recommending the best IVD solution for a customer’s needs.