公司规模
Mid-size Company
地区
- Asia
国家
- China
产品
- EcoStruxure Machine
- EcoStruxure Machine Advisor
- AVEVA’s System Platform
- Modicon PLCs
- Harmony HMI
技术栈
- IoT
- Cloud Computing
- Data Analytics
- Automation
- Remote Monitoring
实施规模
- Enterprise-wide Deployment
影响指标
- Cost Savings
- Productivity Improvements
- Digital Expertise
- Energy Saving
- Waste Reduction
技术
- 平台即服务 (PaaS) - 连接平台
- 分析与建模 - 实时分析
- 功能应用 - 远程监控系统
适用行业
- 服装
适用功能
- 离散制造
- 质量保证
用例
- 预测性维护
- 工厂可见化与智能化
- 库存管理
- 边缘计算与边缘智能
服务
- 系统集成
- 云规划/设计/实施服务
关于客户
ROSO Automation Technology Co., Ltd. is a high-tech enterprise based in Chengdu, China. The company specializes in the research and development, production, and sales of zipper dyeing production lines, providing the most complete production lines in the industry. For years, its cloth belt shaping technology has been helping domestic zipper enterprises greatly improve product quality and effectively reduce production costs. ROSO operates in a highly competitive industry, with China being the world’s largest manufacturer and exporter of zipper products. The company has adopted a unique business model by offering their operating services to zipper manufacturers, in addition to providing customers with a complete set of production line equipment for zipper dyeing.
挑战
ROSO Automation Technology Co., Ltd. is a high-tech enterprise specializing in the research and development, production, and sales of zipper dyeing production lines. The company faced challenges in digitizing their machines and transforming from simple to smart manufacturing. Traditional zipper production was labor-intensive, incurring high labor costs with low product added value. The company also had to deal with the dual challenges of manufacturing and operation due to its business model of providing operating services to zipper manufacturers. The lack of digital systems in production and operation at the factory led to errors and omissions during material handover, inconvenient management of onsite logistics, and confusion regarding the locations of finished and semi-finished products. There was also no adequate mechanism for managing the dyeing formulas, which are central to the dyeing process.
解决方案
To address the cost, efficiency, and management challenges at the factory, ROSO implemented a zipper dyeing production line using Schneider Electric’s EcoStruxure Machine solution. The hardware system, including Modicon PLCs, frequency converters, Lexium servo drives, Harmony touchscreens, and low-voltage power distribution products, ensures the stability and reliability of the production line equipment. On the software side, EcoStruxure Machine Advisor and AVEVA’s System Platform provide support for the long-term operation of the production line. The jointly developed solution is based on AVEVA’s System Platform. The software can quickly develop a tailor-made information system on demand to complete order management, scheduling, warehouse management, and quality inspection. EcoStruxure Machine Advisor makes remote equipment maintenance convenient and efficient. Staff can also implement automatic parameter adjustments through Machine Advisor’s analysis center function to improve yield.
运营影响
数量效益
Case Study missing?
Start adding your own!
Register with your work email and create a new case study profile for your business.
相关案例.
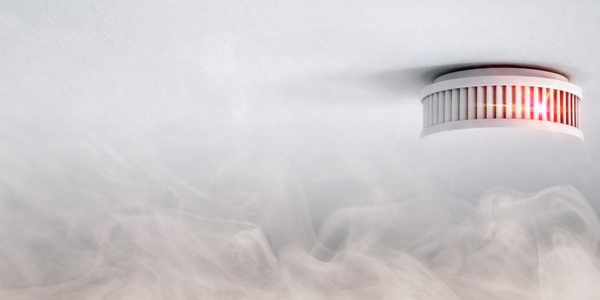
Case Study
Fire Alarm System and Remote Monitoring Sytem
Fire alarm systems are essential in providing an early warning in the event of fire. They help to save lives and protect property whilst also fulfilling the needs of insurance companies and government departments.Fire alarm systems typically consist of several inter-linked components, such as smoke detectors, heat detector, carbon monoxide, manual call points, sounders, alarm and buzzer. The fire alarm system should give immediate information in order to prevent the fire spread and protect live and property.To get maximum protection a shoe manufacturer in Indonesia opted for a new fire alarm system to monitor 13 production sites spread over 160 hectars. Although the company had an existing fire alarm system, it could not be monitored remotely.It was essential that the new system would be able to be monitored from a central control room. It needed to be able to connect to the existing smoke detector and manual call point. Information should be easily collected and passed on to the Supervisory Control and Data Acquisition (SCADA) system. Furthermore, the system should have several features such as alarm management, auto reporting, being connected to many client computers without additional cost, and run 24/7 without fails. The company also needed a system which could be implemented without changing the architecture of the existing fire alarm system.
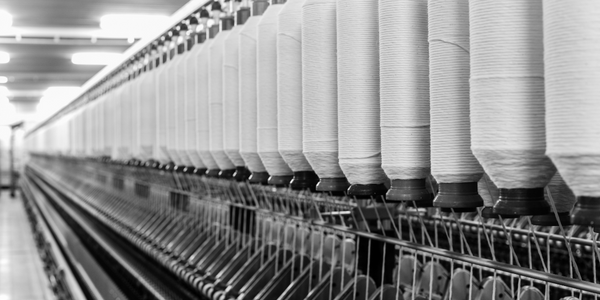
Case Study
IoT Applications and Upgrades in Textile Plant
At any given time, the textile company’s manufacturing facility has up to 2,000 textile carts in use. These carts are pushed from room to room, carrying materials or semi-finished products. Previously, a paper with a hand-written description was attached to each cart. This traditional method of processing made product tracking extremely difficult. Additionally, making sure that every cart of materials or semi-finished products went to its correct processing work station was also a problem. Therefore, the company desired an intelligent solution for tracking assets at their factories. They also wanted a solution that would help them collect process data so they could improve their manufacturing efficiency.
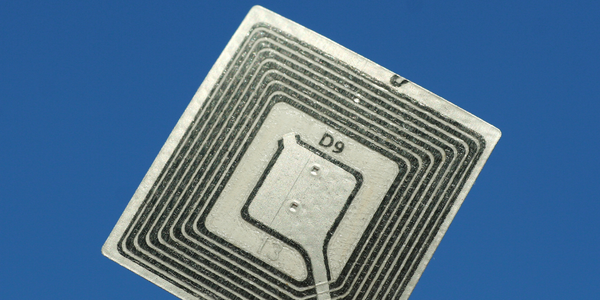
Case Study
Retailer Uses RFID Scanner to Improve Efficiency
Patrizia Pepe wished to improve the logistics of their warehouse: accepting incoming goods from their production sites, movement of items throughout
the warehouse, and packaging of goods for distribution to the retail locations. They initially tried to use barcodes for this function. Because barcodes must be individually scanned within a line-of-sight, the acceptance of goods coming into the warehouse was too time consuming. Working with the University of Florence, Patrizia Pepe instituted a five-month pilot project beginning in August of 2009 to test the validity of an RFID solution. The pilot involved tagging of about 60,000 items for the second seasonal collection, and convinced the company to move forward with tagging all items.
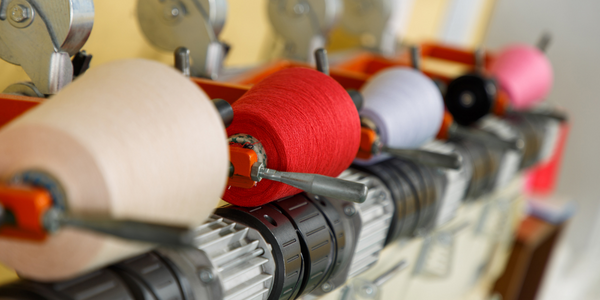
Case Study
Monitoring and Controlling Automatic Mixing and Dispensing Machines
As technology advances, textile manufacturing has been transformed from a labor-intensive to a partially or fully automated industry. Automation is significant in all segments of textile production - from spinning to printing, and textile machinery manufacturers are constantly searching for new technologies and automation processes will increase the productivity of their machines. The color paste mixing and dispensing machine is an essential part of the printing and dyeing process. With the advantage of automatically computerized controls and database management, the system can significantly improve its dispensing precision, working efficiency and production quality as well as reducing material consumption.