地区
- America
- Europe
国家
- United States
产品
- Accident Service
- Fleet Partnership Solutions
- Fuel Service
- Maintenance Service
- Personal Usage & Expense Tracking Service
- Title, Licensing & Registration Service
实施规模
- Enterprise-wide Deployment
影响指标
- Cost Savings
- Customer Satisfaction
- Employee Satisfaction
- Productivity Improvements
适用功能
- 物流运输
用例
- 车队管理
服务
- 系统集成
关于客户
The customer is a construction tool manufacturer with a fleet size of 1,400 vehicles. The company utilizes various services including Accident, Fleet Partnership Solutions, Fuel, Maintenance, Personal Usage & Expense Tracking, and Title, Licensing & Registration. The company was looking to optimize its fleet to maximize productivity, improve safety, and decrease maintenance costs. The company also had specific fuel efficiency sustainability guidelines based on its European parent company’s fleet.
挑战
The construction tool manufacturer was looking to optimize its fleet of 1,400 vehicles to maximize productivity, improve safety, and decrease maintenance costs. The company also had specific fuel efficiency sustainability guidelines based on its European parent company’s fleet. The company faced issues with ergonomics, limited visibility due to upfitting design, loading weight distribution, exceeding allowed weight of loads and excessive idling, all of which impacted safety, maintenance, depreciation and fuel economy.
解决方案
Element Fleet Management conducted ride-alongs with company drivers in both the U.S. and Europe to understand the challenges faced by the drivers. They conducted Total Cost of Ownership analyses to select the most cost-effective and sustainable mix of vehicles. Element recommended a two-year replacement model and a change from mid-size pickup trucks to more cost-effective and sustainable ½ ton pickup trucks as well as a new generation of fuel-efficient cargo vans, depending on the job application. They also designed a safer and more accessible upfitting system for new vehicles.
运营影响
Case Study missing?
Start adding your own!
Register with your work email and create a new case study profile for your business.
相关案例.
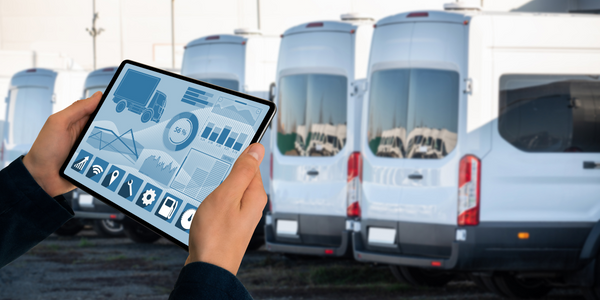
Case Study
IoT-based Fleet Intelligence Innovation
Speed to market is precious for DRVR, a rapidly growing start-up company. With a business model dependent on reliable mobile data, managers were spending their lives trying to negotiate data roaming deals with mobile network operators in different countries. And, even then, service quality was a constant concern.
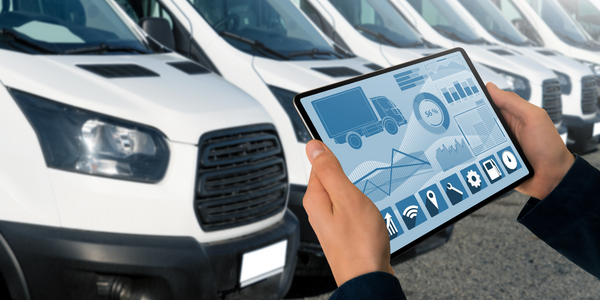
Case Study
Vehicle Fleet Analytics
Organizations frequently implement a maintenance strategy for their fleets of vehicles using a combination of time and usage based maintenance schedules. While effective as a whole, time and usage based schedules do not take into account driving patterns, environmental factors, and sensors currently deployed within the vehicle measuring crank voltage, ignition voltage, and acceleration, all of which have a significant influence on the overall health of the vehicle.In a typical fleet, a large percentage of road calls are related to electrical failure, with battery failure being a common cause. Battery failures result in unmet service agreement levels and costly re-adjustment of scheduled to provide replacement vehicles. To reduce the impact of unplanned maintenance, the transportation logistics company was interested in a trial of C3 Vehicle Fleet Analytics.
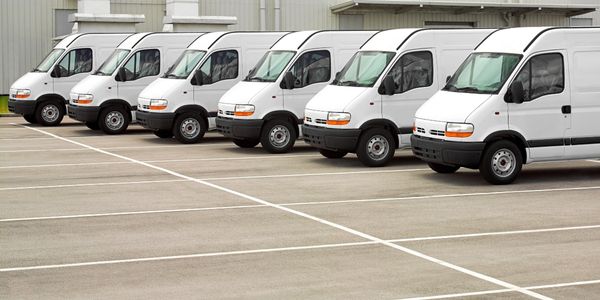
Case Study
Zonar Takes the Wheel with a M2M Solution
Zonar’s fleet management solutions collect, report and analyze data before, during and after a vehicle’s trip. The company needed Machine-to-Machine (M2M) connectivity to enable communication between in-vehicle devices and back-end systems. To deliver high volumes of potentially sensitive information from and to moving vehicles – and keep pace with its rapid business growth – Zonar wanted a highly secure solution that it could easily manage and that had the required national and global reach.