公司规模
Large Corporate
地区
- America
国家
- United States
产品
- webMethods product suite
技术栈
- webMethods Business Process Management (BPM)
- webMethods item canonical
实施规模
- Enterprise-wide Deployment
影响指标
- Productivity Improvements
- Cost Savings
技术
- 应用基础设施与中间件 - API 集成与管理
- 应用基础设施与中间件 - 数据交换与集成
适用行业
- 食品与饮料
适用功能
- 产品研发
- 质量保证
用例
- 供应链可见性(SCV)
- 库存管理
服务
- 系统集成
- 软件设计与工程服务
关于客户
Dean Foods is one of the leading food and beverage companies in the USA, and the largest processor and distributor of milk and other dairy products. It is also the nation’s leading manufacturer of soy milk, organic milk and other organic foods. Through its WhiteWave Foods Company, it offers a variety of nationally branded products, such as Silk soy milk, Horizon Organic dairy products, International Delight coffee creamers, LAND O’LAKES creamers and fluid dairy products. Dean Foods operates more than 110 plants in the United States and Spain. Over the years, Dean Foods has grown through acquisitions, resulting in a complex and diverse business structure with multiple independent business units.
挑战
Over the years, Dean Foods acquired several new businesses which operate as independent business units. This resulted in inconsistent data across its business units for the same products and a lengthy process to find and validate the data that customers needed. Tracking product formulas for all flavors within business units created inaccuracies and complexity that slowed the item maintenance process. As a result of company acquisitions, Dean Foods acquired a challenging number of new and inconsistent SKUs and UPC codes. There was inconsistent data between business units for the same products and a lengthy process to find and validate the data that customers needed. Dean also needed to simplify and homogenize complex product information. There were multiple levels of descriptions for the same product, and tracking product formulas for all flavors within business units created inaccuracies and complexity that slowed the item maintenance process.
解决方案
Dean Foods decided to leverage the webMethods product suite to create a Master Item Synchronization Process that ensured consistent data use across multiple business units and customers; a process that adhered to industry and customer mandates for information and involved end-users from different functional areas of the business. With the webMethods solution, end-users from different functional areas of the business would be involved in item setup and maintenance activities to validate data accuracy. webMethods Business Process Management (BPM) workflow and portal bring together end-users from different areas of the business to support best practices and ensure visibility and accuracy of item information. No one individual owns the product data but everyone has a part in ensuring consistency and accuracy. Dean Foods employed the use of a webMethods item canonical to describe products used by different business units and customers. Their ability to achieve consistency and accuracy with product information across the company and with customers has been largely driven by their commitment and adoption of a single process leveraging a single item canonical.
运营影响
数量效益
Case Study missing?
Start adding your own!
Register with your work email and create a new case study profile for your business.
相关案例.

Case Study
The Kellogg Company
Kellogg keeps a close eye on its trade spend, analyzing large volumes of data and running complex simulations to predict which promotional activities will be the most effective. Kellogg needed to decrease the trade spend but its traditional relational database on premises could not keep up with the pace of demand.
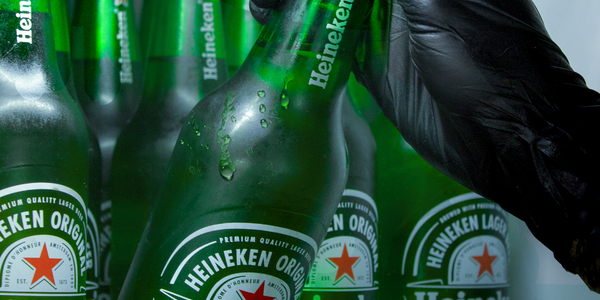
Case Study
HEINEKEN Uses the Cloud to Reach 10.5 Million Consumers
For 2012 campaign, the Bond promotion, it planned to launch the campaign at the same time everywhere on the planet. That created unprecedented challenges for HEINEKEN—nowhere more so than in its technology operation. The primary digital content for the campaign was a 100-megabyte movie that had to play flawlessly for millions of viewers worldwide. After all, Bond never fails. No one was going to tolerate a technology failure that might bruise his brand.Previously, HEINEKEN had supported digital media at its outsourced datacenter. But that datacenter lacked the computing resources HEINEKEN needed, and building them—especially to support peak traffic that would total millions of simultaneous hits—would have been both time-consuming and expensive. Nor would it have provided the geographic reach that HEINEKEN needed to minimize latency worldwide.
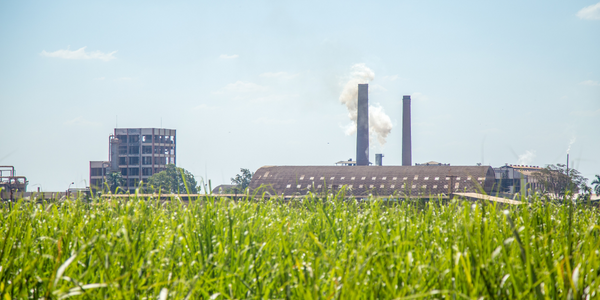
Case Study
Energy Management System at Sugar Industry
The company wanted to use the information from the system to claim under the renewable energy certificate scheme. The benefit to the company under the renewable energy certificates is Rs 75 million a year. To enable the above, an end-to-end solution for load monitoring, consumption monitoring, online data monitoring, automatic meter data acquisition which can be exported to SAP and other applications is required.
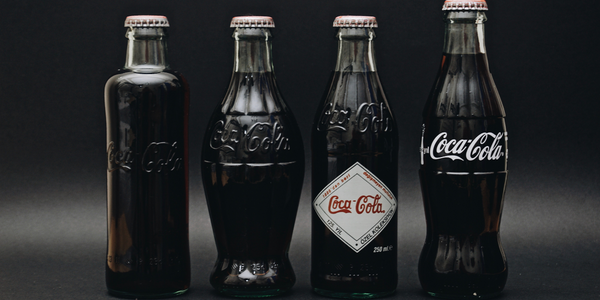
Case Study
Coca Cola Swaziland Conco Case Study
Coco Cola Swaziland, South Africa would like to find a solution that would enable the following results: - Reduce energy consumption by 20% in one year. - Formulate a series of strategic initiatives that would enlist the commitment of corporate management and create employee awareness while helping meet departmental targets and investing in tools that assist with energy management. - Formulate a series of tactical initiatives that would optimize energy usage on the shop floor. These would include charging forklifts and running cold rooms only during off-peak periods, running the dust extractors only during working hours and basing lights and air-conditioning on someone’s presence. - Increase visibility into the factory and other processes. - Enable limited, non-intrusive control functions for certain processes.
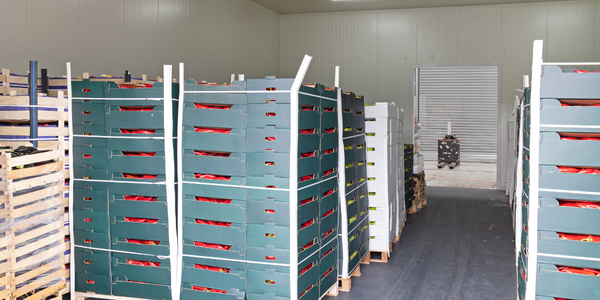
Case Study
Temperature Monitoring for Restaurant Food Storage
When it came to implementing a solution, Mr. Nesbitt had an idea of what functionality that he wanted. Although not mandated by Health Canada, Mr. Nesbitt wanted to ensure quality control issues met the highest possible standards as part of his commitment to top-of-class food services. This wish list included an easy-to use temperature-monitoring system that could provide a visible display of the temperatures of all of his refrigerators and freezers, including historical information so that he could review the performance of his equipment. It also had to provide alert notification (but email alerts and SMS text message alerts) to alert key staff in the event that a cooling system was exceeding pre-set warning limits.
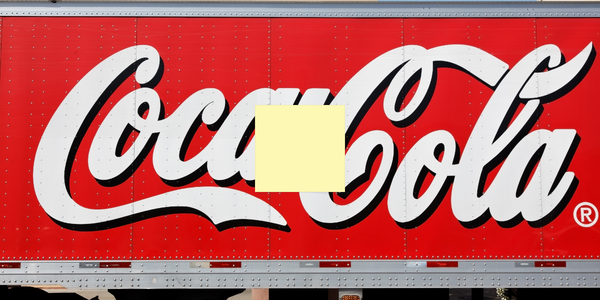
Case Study
Coca-Cola Refreshments, U.S.
Coca-Cola Refreshments owns and manages Coca-Cola branded refrigerators in retail establishments. Legacy systems were used to locate equipment information by logging onto multiple servers which took up to 8 hours to update information on 30-40 units. The company had no overall visibility into equipment status or maintenance history.