公司规模
Large Corporate
地区
- America
- Asia
国家
- United States
- Japan
产品
- WebFOCUS
- iWay Software
技术栈
- J.D. Edwards accounting system
- Microsoft Windows 2000 server
实施规模
- Enterprise-wide Deployment
影响指标
- Productivity Improvements
- Cost Savings
技术
- 分析与建模 - 实时分析
适用功能
- 离散制造
- 采购
用例
- 实时定位系统 (RTLS)
- 预测性维护
服务
- 系统集成
- 培训
关于客户
Toppan Interamerica is a division of Toppan Printing, a $16 billion corporation based in Tokyo. The company produces a wide variety of precoated papers for the furniture and laminating industries. Leveraging the experience and resources of Toppan Printing, Toppan Interamerica excels at reproducing the look of natural materials in its wood-grain patterns. The company has seen a steady rise in productivity since its parent company was founded more than 100 years ago. However, key enterprise reporting processes resisted automation until very recently. The small IT staff was burdened with a steady stream of report requests, and employees often had to wait two days or more to obtain information about sales, accounting, production, and other key business activities.
挑战
Toppan Interamerica, a division of Toppan Printing, a $16 billion corporation based in Tokyo, was facing challenges with its reporting processes. The small IT staff was burdened with a steady stream of report requests, and employees often had to wait two days or more to obtain information about sales, accounting, production, and other key business activities. The company was still performing most financial and production reporting manually. The IT staff could barely keep up with the reporting demands of their old systems. They needed to make some changes in their reporting environment if they were to adequately support the information management needs of the business going forward.
解决方案
Toppan Interamerica implemented Information Builders' WebFOCUS and iWay Software to bring their business intelligence (BI) systems up to the same caliber as its advanced manufacturing processes for decorative paper. Installing a new J.D. Edwards accounting system motivated the upgrade to a world-class BI environment. WebFOCUS and iWay were selected for their ability to provide native connectivity to DB/400 data on the AS/400 platform, allowing for real-time data access. The software was used to create a self-service information system that gives executives and managers a personalized, high-level view of business information. The customized reporting environment simplifies the process of running structured reports and performing queries, while dramatically boosting the overall repertoire of standard reports. For example, financial professionals formerly had about 10 accounting reports available; now they have more than 100, and reports that used to take two days to create are now available within an hour.
运营影响
数量效益
Case Study missing?
Start adding your own!
Register with your work email and create a new case study profile for your business.
相关案例.

Case Study
Remote Monitoring & Predictive Maintenance App for a Solar Energy System
The maintenance & tracking of various modules was an overhead for the customer due to the huge labor costs involved. Being an advanced solar solutions provider, they wanted to ensure early detection of issues and provide the best-in-class customer experience. Hence they wanted to automate the whole process.
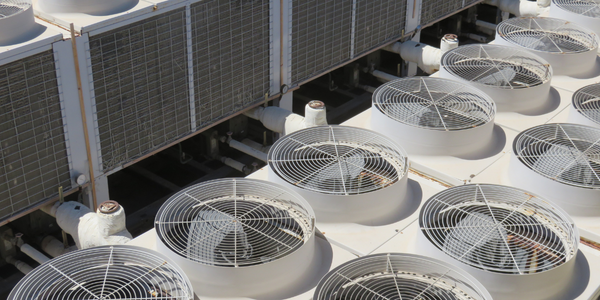
Case Study
Predictive Maintenance for Industrial Chillers
For global leaders in the industrial chiller manufacturing, reliability of the entire production process is of the utmost importance. Chillers are refrigeration systems that produce ice water to provide cooling for a process or industrial application. One of those leaders sought a way to respond to asset performance issues, even before they occur. The intelligence to guarantee maximum reliability of cooling devices is embedded (pre-alarming). A pre-alarming phase means that the cooling device still works, but symptoms may appear, telling manufacturers that a failure is likely to occur in the near future. Chillers who are not internet connected at that moment, provide little insight in this pre-alarming phase.
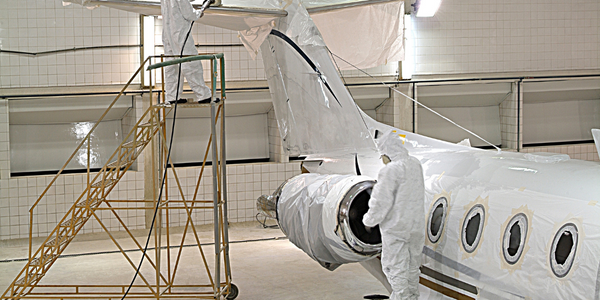
Case Study
Aircraft Predictive Maintenance and Workflow Optimization
First, aircraft manufacturer have trouble monitoring the health of aircraft systems with health prognostics and deliver predictive maintenance insights. Second, aircraft manufacturer wants a solution that can provide an in-context advisory and align job assignments to match technician experience and expertise.
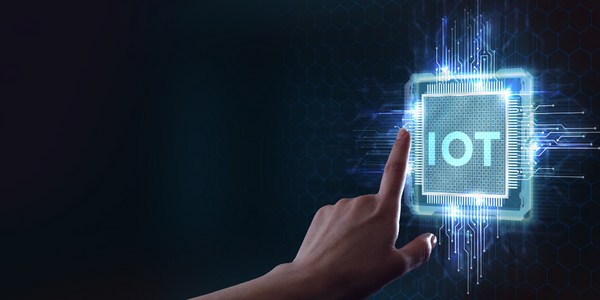
Case Study
Leading Tools Manufacturer Transforms Operations with IoT
Stanley Black & Decker required transparency of real-time overall equipment effectiveness and line productivity to reduce production line change over time.The goal was to to improve production to schedule, reduce actual labor costs and understanding the effects of shift changes and resource shifts from line to line.
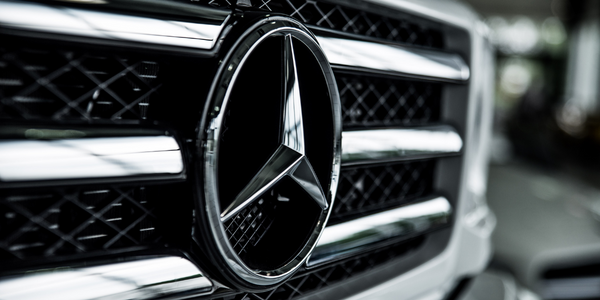
Case Study
Integral Plant Maintenance
Mercedes-Benz and his partner GAZ chose Siemens to be its maintenance partner at a new engine plant in Yaroslavl, Russia. The new plant offers a capacity to manufacture diesel engines for the Russian market, for locally produced Sprinter Classic. In addition to engines for the local market, the Yaroslavl plant will also produce spare parts. Mercedes-Benz Russia and his partner needed a service partner in order to ensure the operation of these lines in a maintenance partnership arrangement. The challenges included coordinating the entire maintenance management operation, in particular inspections, corrective and predictive maintenance activities, and the optimizing spare parts management. Siemens developed a customized maintenance solution that includes all electronic and mechanical maintenance activities (Integral Plant Maintenance).