公司规模
Mid-size Company
地区
- America
国家
- Canada
产品
- Poka mobile performance support app
技术栈
- QR code
- iPad
实施规模
- Enterprise-wide Deployment
影响指标
- Productivity Improvements
- Customer Satisfaction
- Employee Satisfaction
技术
- 应用基础设施与中间件 - API 集成与管理
适用行业
- 电子产品
适用功能
- 离散制造
- 质量保证
用例
- 自动化制造系统
- 实时定位系统 (RTLS)
- 远程协作
服务
- 软件设计与工程服务
关于客户
ABB Saint Jean is a plant in the installation products division of ABB Group. It is a market leader in electric boxes and fittings. The plant is committed to consistently exceeding customer expectations and in today’s economy, that means being more agile in order to quickly respond to customer requests. The plant has 450 employees and is located in Saint-Jean, QC, Canada. The manufacturing operations span 200,000 square feet and includes three shifts. The plant is undergoing a digital transformation journey to modernize its operations by upgrading outdated equipment and IT systems, and empowering their workforce.
挑战
ABB Saint Jean, a plant in the installation products division of ABB Group, was looking for ways to improve product quality and customer satisfaction, while driving greater efficiency in production. The plant recognized an untapped opportunity to harness and build upon the knowledge of its factory workers. They knew workers were key to uncovering what’s happening on the factory floor, finding solutions to problems and contributing to continuous improvement. However, the plant was facing a digital gap. The way they get their information and communicate had evolved dramatically in the past 15 years, but how they do things on the factory floor hadn’t changed in over 25 years.
解决方案
To address the digital gap, the plant implemented a mobile performance support app developed by Poka. This app combines digital content, communications and collaboration into a single, worker-centered interface to support the unique needs of the factory floor. Workers just scan a QR code on their equipment or work order using an iPad to access the most up-to-date instructions, drawings and training guides. Over 450 employees at the plant now use Poka to instantly access the resources they need to work to standard, troubleshoot problems, and share updates directly at their workstations. This has enabled ABB to digitally transform its Saint-Jean plant. Workers are now able to share and learn from one another in real time and contribute to continuous improvement as part of the flow of their daily work.
运营影响
数量效益
Case Study missing?
Start adding your own!
Register with your work email and create a new case study profile for your business.
相关案例.
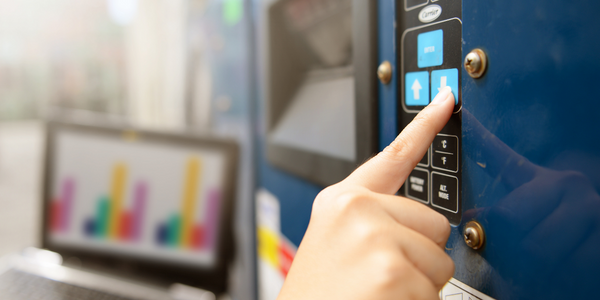
Case Study
Remote Temperature Monitoring of Perishable Goods Saves Money
RMONI was facing temperature monitoring challenges in a cold chain business. A cold chain must be established and maintained to ensure goods have been properly refrigerated during every step of the process, making temperature monitoring a critical business function. Manual registration practice can be very costly, labor intensive and prone to mistakes.
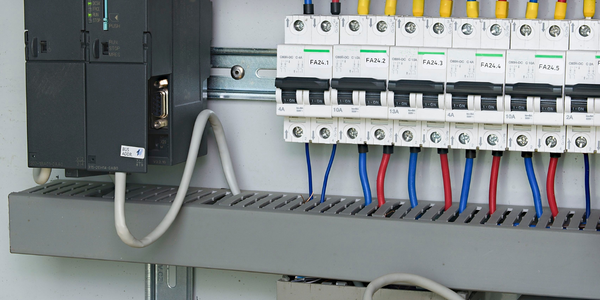
Case Study
Predictive maintenance in Schneider Electric
Schneider Electric Le Vaudreuil factory in France is recognized by the World Economic Forum as one of the world’s top nine most advanced “lighthouse” sites, applying Fourth Industrial Revolution technologies at large scale. It was experiencing machine-health and unplanned downtime issues on a critical machine within their manufacturing process. They were looking for a solution that could easily leverage existing machine data feeds, be used by machine operators without requiring complex setup or extensive training, and with a fast return on investment.
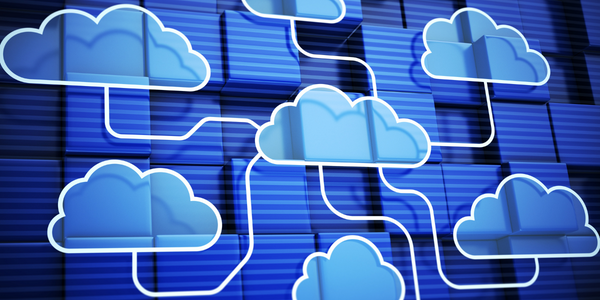
Case Study
Cloud Solution for Energy Management Platform-Schneider Electric
Schneider Electric required a cloud solution for its energy management platform to manage high computational operations, which were essential for catering to client requirements. As the business involves storage and analysis of huge amounts of data, the company also needed a convenient and scalable storage solution to facilitate operations efficiently.
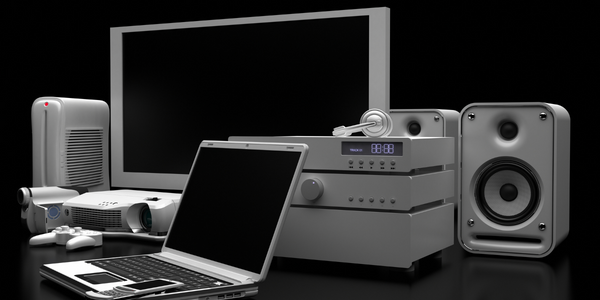
Case Study
Leveraging the IoT to Gain a Competitive Edge in International Competition
Many large manufacturers in and outside Japan are competing for larger market share in the same space, expecting a growing demand for projectors in the areas of entertainment, which requires glamor and strong visual performance as well as digital signage that can attract people’s attention. “It is becoming more and more difficult to differentiate ourselves with stand-alone hardware products,” says Kazuyuki Kitagawa, Director of Service & Support at Panasonic AVC Networks. “In order for Panasonic to grow market share and overall business, it is essential for us to develop solutions that deliver significant added value.” Panasonic believes projection failure and quality deterioration should never happen. This is what and has driven them to make their projectors IoT-enabled. More specifically, Panasonic has developed a system that collects data from projectors, visualizes detailed operational statuses, and predicts issues and address them before failure occurs. Their projectors are embedded with a variety of sensors that measure power supply, voltage, video input/ output signals, intake/exhaust air temperatures, cooling fan operations, and light bulb operating time. These sensors have been used to make the projector more intelligent, automatically suspending operation when the temperature rises excessively, and automatically switching light bulbs. Although this was a great first step, Panasonic projectors were still not equipped with any capability to send the data over a network.