Dozuki
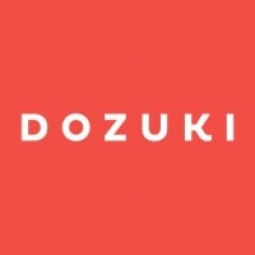
概述
总部
美国
|
成立年份
2011
|
公司类型
私营公司
|
收入
$10-100m
|
员工人数
51 - 200
|
网站
|
公司介绍
Dozuki makes it easy to capture expert knowledge, tie it directly to work guidance, and give frontline workers digital access to standards — driving operational excellence across your company.
Dozuki helps customers achieve a 40% reduction in training time, 61% reduction in document creation time, and 67% improved communication through our easy to roll-out solution.
Supplier missing?
Start adding your own!
Register with your work email and create a new supplier profile for your business.
实例探究.
Case Study
World Class Training with Digital Work Instructions: A Case Study on a Fortune 500 Food and Beverage Company
The company was grappling with several challenges, including increasing staff retirements, lack of digitized processes, and absence of a formal training program. These issues were leading to spikes in quality problems and downtime. As new frontline employees joined, there was no program in place to upskill them properly to meet production demands, leading to a repetitive cycle of issues. The company was losing approximately $3 million per year due to poor frontline training. Their facilities historically relied on job shadowing and word of mouth for operator training, which was proving to be inadequate. With high numbers of retiring staff and outdated documentation held in paper binders, standardizing process information was a pressing need. Changeover errors in their sensitive assembly lines for perishable products were costing the company millions of dollars a year in defects, supply chain issues, and profit losses.
Case Study
Implementing Continuous Improvement for Streamlined Processes and Engaged Employees
Companies, regardless of their size, often struggle with keeping their employees motivated towards shared goals. The challenge lies in creating a culture where teams are invested in company goals and are constantly working towards streamlining processes. The lack of a problem-solving culture can lead to disengaged employees, inefficient workflows, and increased waste and rework. This can ultimately impact the bottom line, reducing the value delivered to customers. Additionally, many companies have a wealth of processes and information locked in tribal knowledge, which is not transferable and cannot be improved upon. This presents a major risk, as without a standard, there is no benchmark to improve upon.
Case Study
Digitizing Processes with Dozuki Saves Thousands Per Hour for Leading Equipment Manufacturer
For nearly a century, a leading manufacturer of construction and mining equipment, diesel and natural gas engines, industrial gas turbines, and diesel-electric locomotives has been striving to digitize and standardize its processes to minimize waste and control machine setups and changeovers. However, the company faced significant challenges in achieving this goal. The existing documentation was limited, making it difficult for frontline workers to share feedback to improve operations. The company was using Excel to create and store process information, which often contained over fifty pages of information that workers had to read and retain. This method also lacked the ability to gather and implement frontline feedback, leading to missed opportunities for operational improvements. The company also faced inconsistencies in production, competency gaps among employees due to job shadowing as a primary training method, and safety concerns. The introduction of new automation technology also posed a challenge as the company needed to ensure that standards were properly distributed to frontline operators.
Case Study
Enterprise Grade Digital Training: A Case Study on Fortune 100 Consumer Goods Manufacturer
The Fortune 100 Consumer Goods Manufacturer, a multinational corporation operating in various fields of industrial manufacturing, faced a significant challenge as a large portion of their veteran workforce approached retirement. The incorporation of increasingly sophisticated technology into frontline production processes meant that tasks such as preventive maintenance and line changeovers required more time and knowledge to complete. Machine operating procedures were complex and resulted in lengthy training times. The documentation was extensive and lacked visual aids, making it difficult for new employees to understand. The impending loss of veteran frontline operators and the uncaptured tribal knowledge posed a significant challenge in scaling the training and support for new employees across multiple facilities. The company also faced issues with increasing cycle times, suggesting that less experienced employees required more time to complete processes. This was costing the company valuable production time and millions of dollars across their 200+ plants.
Case Study
Preserving Tribal Knowledge in the Manufacturing Industry Amidst Workforce Shifts
The case study revolves around a large manufacturing company that relies heavily on tribal knowledge for its maintenance procedures. The company has a unique situation where certain maintenance procedures are only required every 5 to 10 years. This knowledge is passed down from long-term employees who have been with the company for decades. However, the company is facing a potential challenge with the changing dynamics of the workforce. The current trend shows that millennials, who are now the dominant workforce, tend to stay with a company for only 2-3 years, significantly less than the 5-10 year maintenance cycle. The average tenure of workers is 4.6 years, and even lower for millennials at 3.2 years. This poses a significant risk to the company's maintenance procedures as the knowledge may not be passed down effectively due to the shorter tenure of employees.