Qualio
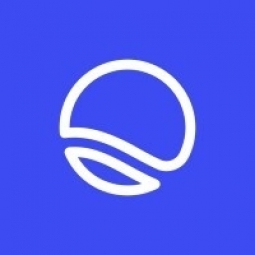
概述
公司介绍
Qualio is a cloud-based quality management software system designed for life science companies. Qualio empowers medical device, pharmaceutical, biotech, and contract organizations to get to market faster, boost revenue, and cut risk. Over 650+ companies in 80 countries use Qualio to embed and automate GxP, FDA, and ISO compliance.
Qualio unites your teams, processes, and data in a single source of truth that supports a quality culture and makes your business stronger, fitter, and more competitive.
Supplier missing?
Start adding your own!
Register with your work email and create a new supplier profile for your business.
实例探究.
Case Study
StayinFront's Success with eQMS System for Global Quality Standards
StayinFront, a leading global provider of mobile cloud-based field force effectiveness and CRM software for life science organizations, faced a significant challenge in maintaining consistent world-class quality standards across its operations. Their clients, including Mondelez, Kellogg's, and P&G, demanded high-quality standards. The COVID-19 pandemic triggered a deep market shift for their life science customers, forcing StayinFront to adapt quickly to maximize customer satisfaction. With a global customer base and sites in 10 countries, it became clear that StayinFront needed an electronic quality system to help them consistently execute high-quality operations with total visibility. They also needed a mechanism to onboard and train a growing workforce around core compliance demands like information security and corrective actions.
Case Study
AI-Powered Solutions by CureMetrix: Enhancing Radiology Efficiency and Accuracy
The COVID-19 pandemic has resulted in a massive backlog of X-rays for radiologists to sift through, due to the closure of non-essential businesses and people staying at home. The traditional detection system for radiologists relied heavily on their own eyes, which could lead to human error. This situation posed a significant challenge in terms of time efficiency and accuracy in the detection and classification of anomalies in mammography. The need for a solution that could help radiologists improve the accuracy of their work, support better clinical decision-making, and improve financial outcomes for hospitals and clinics was evident.
Case Study
Ender Diagnostics' Transition to a Cloud-Based Quality Management System with Qualio
Ender Diagnostics, a Swiss developer and manufacturer of rapid molecular diagnostic kits for the detection of SARS-CoV-2, faced a significant challenge with its quality management system (QMS). Founded in 2020, the company expanded rapidly due to the high demand for COVID-19 testing. However, Ender's manual, paper-based QMS was unable to keep up with this growth. It lacked audit-ready traceability and control and did not support remote and home working. The majority of Ender's workforce consisted of scientists and graduates, with only small pockets of specific quality management experience. The company needed a system that would not distract from scientific work with time-consuming administrative tasks. The challenge was to implement a document and training management system that could handle the company's rapid expansion and remote working needs.
Case Study
Empowering Bond Digital Health with a Quality Management System from Scratch
Bond Digital Health, a medical software provider, was faced with the challenge of establishing a quality management system (QMS) from scratch. As a start-up, the company had ambitions of becoming a quality-centric, quality-culture-driven organization guided by defined processes. Quality Manager Phil Cooley was tasked with building the company's QMS and helping bring Bond's software system to market. He wanted to establish compliant, documented processes for core quality management activities, like document control, without the time-consuming effort of manually building processes and encouraging colleagues to follow them. The company also processes thousands of patient records each day, making GDPR and HIPAA compliance vital quality and regulatory targets. Phil recognized that an electronic quality management system (eQMS) would act as a vital shortcut, providing a ready-made quality management structure and a centralized single source of truth for his colleagues.
Case Study
EvoEndo's Transformation with Qualio's eQMS
EvoEndo, a medical device company, was facing challenges with its existing electronic Quality Management System (eQMS). The system, built by a different contract manufacturing organization (CMO), was on-premise and heavily reliant on paper, making it clunky and unfit for purpose. The company's CEO, Heather Underwood, found that efficiency and document control were slipping, negatively impacting the company's FDA 510(k) preparations. The process of reviewing and approving documents was time-consuming, involving printing, signing, and scanning. Accessing vital QMS information was also difficult. As EvoEndo transitioned to a new CMO, they began to search for a pre-existing, cloud-based eQMS that could better meet their needs. Heather wanted to enhance EvoEndo's internal quality management system, including document control and training management, without solely relying on the product-based data in her CMO's QMS.
Case Study
Expression Therapeutics Streamlines Document Management with Qualio
Expression Therapeutics, a clinical stage gene and cell therapy company, was facing a significant challenge as it planned its new 43,000 sqft facility in Westchester, Ohio. The company was transitioning into a new phase of growth and needed to implement a modern quality management system that didn't rely on paper. The company's major investment in their Ohio operations represented a new phase of growth and Eric Day, Director of Quality Assurance, saw document control efficiency as their biggest challenge. The company was previously tracking deviations, CAPAs, and training in spreadsheets and hard documents, which was inefficient and time-consuming.
Case Study
Koneksa's Digital Transformation: Saving Time and Enhancing Quality Management
Koneksa, a provider of digital biomarker technology for clinical trials, was facing a significant challenge in 2020. As the company began to realize its ambitious growth plans, it found that its legacy quality management system was becoming a hindrance. The system, a combination of multiple learning management systems (LMS), Google folders, spreadsheets, and manual document and training management activities, was manageable during Koneksa's early stages. However, as the company grew, this system was unable to keep pace with the increasing demands and objectives.
Case Study
Watchmaker Genomics: Implementing Quality Control with Qualio
Watchmaker Genomics, a company specializing in protein engineering and enzyme manufacturing, faced a significant challenge in establishing a robust quality control system. The company's products are used in CAP/CLIA laboratories for sample analysis, making airtight product quality crucial. CEO Trey Foskett, having established several other companies in the past, was aware of the business impact of implementing a digital quality approach early on, rather than adding it to pre-existing processes. The company was eager to establish a single, central mechanism for managing quality, from accessing daily information and documenting work to accessing rich quality data and being able to quickly and nimbly respond to defects with controlled CAPA plans. Quality Control Manager Skyler Mishkin was tasked with finding the best possible electronic quality management system (eQMS), and the search began within the first few months of the company's establishment.