公司规模
Large Corporate
地区
- America
国家
- United States
产品
- JDA Demand
- JDA Fulfillment
技术栈
- Supply Chain Management Software
- Inventory Management Software
实施规模
- Enterprise-wide Deployment
影响指标
- Cost Savings
- Customer Satisfaction
- Productivity Improvements
技术
- 功能应用 - 库存管理系统
- 功能应用 - 企业资源规划系统 (ERP)
适用行业
- 化学品
- 建筑与基础设施
- 医疗保健和医院
适用功能
- 物流运输
- 采购
用例
- 库存管理
- 供应链可见性(SCV)
服务
- 系统集成
关于客户
Airgas, Inc. 是美国最大的工业、医疗和特种气体以及焊接设备和用品分销商。该公司还是最大的安全产品全国分销商之一,是一氧化二氮、干冰和液态二氧化碳以及工艺化学品、制冷剂和氨产品的主要来源。该公司拥有 14,000 多名员工,服务于多元化的客户群,包括焊工和金属制造商、建筑公司、医院和诊所、疗养院和家庭医疗保健提供商、设备制造商和研究实验室。为了满足其多元化客户群的需求,Airgas 建立了一个全国性的分销平台,涵盖多个渠道,包括零售分支机构、配送中心以及入站和出站电话营销中心。Airgas 的综合网络由大约 1,100 个地点组成,从为上门客户提供服务的零售店到遍布美国各地的大型配送中心 (DC)
挑战
Airgas, Inc. 是美国最大的工业、医疗和特种气体以及焊接设备和用品分销商,由于其庞大的业务网络,面临着独特的供应链挑战。该公司制定了雄心勃勃的增长和盈利目标,实施了由有机增长和众多核心、产品线和战略收购推动的积极业务战略。然而,该公司的快速、收购推动的增长并没有得到其现有系统的支持。Airgas 使用传统系统和行业特定解决方案的混合来管理需求,但这些系统没有集成,无法扩展以跟上公司的增长。该公司的 12 家地区运营公司各自运行着自己的需求管理解决方案版本,这进一步加剧了在复杂的批发分销环境中管理近 350 万件商品的需求。因此,Airgas 缺乏优化库存、降低成本和提高客户满意度所需的企业范围的供需视图。
解决方案
为了解决其关键的库存平衡挑战,Airgas 开始评估自动化需求和履行系统。该公司想要一个真正集成的供应链管理解决方案——一个能够连接供应商和次级供应商、内部运营、贸易客户、零售客户和最终用户的解决方案。经过全面审查,Airgas 选择了 JDA Software 的 Intelligent Fulfillment™ 解决方案中的 JDA Demand 和 JDA Fulfillment,以应对其业务挑战并实现其库存的全球视图。Airgas 利用 JDA Demand 管理超过一百万个需求预测单位,并使用汇总和协调在多个级别进行预测。该公司每月生成预测并发布需求规划人员每天进行的更新。JDA Fulfillment 允许 Airgas 通过其 1,500 多家供应商网络管理 250,000 个独特商品,包括 912,000 个库存 SKU 和超过 250 万个非库存 SKU。该公司每晚都会运行其履行计划,在一个典型的工作日内会生成超过 4,000 份采购订单。
运营影响
数量效益
Case Study missing?
Start adding your own!
Register with your work email and create a new case study profile for your business.
相关案例.
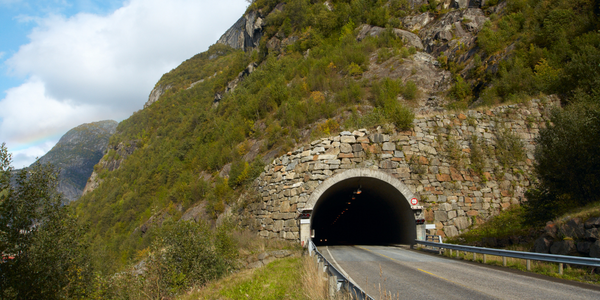
Case Study
IoT System for Tunnel Construction
The Zenitaka Corporation ('Zenitaka') has two major business areas: its architectural business focuses on structures such as government buildings, office buildings, and commercial facilities, while its civil engineering business is targeted at structures such as tunnels, bridges and dams. Within these areas, there presented two issues that have always persisted in regard to the construction of mountain tunnels. These issues are 'improving safety" and "reducing energy consumption". Mountain tunnels construction requires a massive amount of electricity. This is because there are many kinds of electrical equipment being used day and night, including construction machinery, construction lighting, and ventilating fan. Despite this, the amount of power consumption is generally not tightly managed. In many cases, the exact amount of power consumption is only ascertained when the bill from the power company becomes available. Sometimes, corporations install demand-monitoring equipment to help curb the maximum power demanded. However, even in these cases, the devices only allow the total volume of power consumption to be ascertained, or they may issue warnings to prevent the contracted volume of power from being exceeded. In order to tackle the issue of reducing power consumption, it was first necessary to obtain an accurate breakdown of how much power was being used in each particular area. In other words, we needed to be able to visualize the amount of power being consumed. Safety, was also not being managed very rigorously. Even now, tunnel construction sites often use a 'name label' system for managing entry into the work site. Specifically, red labels with white reverse sides that bear the workers' names on both sides are displayed at the tunnel work site entrance. The workers themselves then flip the name label to the appropriate side when entering or exiting from the work site to indicate whether or not they are working inside the tunnel at any given time. If a worker forgets to flip his or her name label when entering or exiting from the tunnel, management cannot be performed effectively. In order to tackle the challenges mentioned above, Zenitaka decided to build a system that could improve the safety of tunnel construction as well as reduce the amount of power consumed. In other words, this new system would facilitate a clear picture of which workers were working in each location at the mountain tunnel construction site, as well as which processes were being carried out at those respective locations at any given time. The system would maintain the safety of all workers while also carefully controlling the electrical equipment to reduce unnecessary power consumption. Having decided on the concept, our next concern was whether there existed any kind of robust hardware that would not break down at the construction work site, that could move freely in response to changes in the working environment, and that could accurately detect workers and vehicles using radio frequency identification (RFID). Given that this system would involve many components that were new to Zenitaka, we decided to enlist the cooperation of E.I.Sol Co., Ltd. ('E.I.Sol') as our joint development partner, as they had provided us with a highly practical proposal.
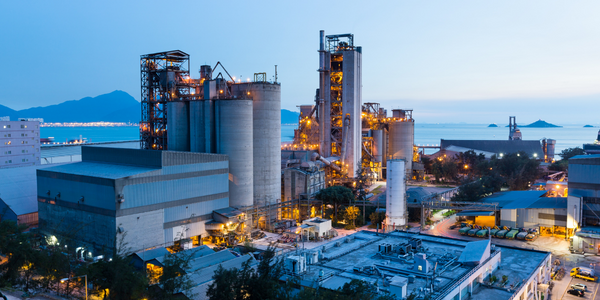
Case Study
Honeywell - Tata Chemicals Improves Data Accessibility with OneWireless
Tata was facing data accessibility challenges in the cement plant control room tapping signals from remote process control areas and other distant locations, including the gas scrubber. Tata needed a wireless solution to extend its control network securely to remote locations that would also provide seamless communication with existing control applications.
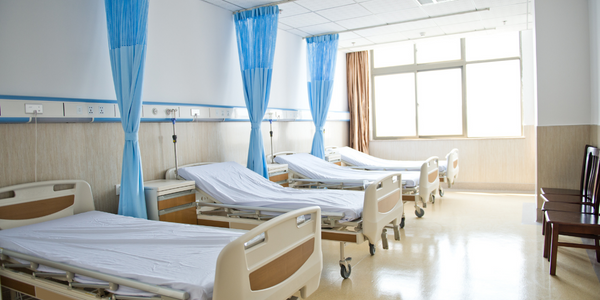
Case Study
Hospital Inventory Management
The hospital supply chain team is responsible for ensuring that the right medical supplies are readily available to clinicians when and where needed, and to do so in the most efficient manner possible. However, many of the systems and processes in use at the cancer center for supply chain management were not best suited to support these goals. Barcoding technology, a commonly used method for inventory management of medical supplies, is labor intensive, time consuming, does not provide real-time visibility into inventory levels and can be prone to error. Consequently, the lack of accurate and real-time visibility into inventory levels across multiple supply rooms in multiple hospital facilities creates additional inefficiency in the system causing over-ordering, hoarding, and wasted supplies. Other sources of waste and cost were also identified as candidates for improvement. Existing systems and processes did not provide adequate security for high-cost inventory within the hospital, which was another driver of cost. A lack of visibility into expiration dates for supplies resulted in supplies being wasted due to past expiry dates. Storage of supplies was also a key consideration given the location of the cancer center’s facilities in a dense urban setting, where space is always at a premium. In order to address the challenges outlined above, the hospital sought a solution that would provide real-time inventory information with high levels of accuracy, reduce the level of manual effort required and enable data driven decision making to ensure that the right supplies were readily available to clinicians in the right location at the right time.

Case Study
Advanced Elastomer Systems Upgrades Production
In order to maintain its share of the international market for thermoplastic elastomers AES recently expanded its Florida plant by adding a new production line. While the existing lines were operating satisfactorily using a PROVOX distributed control system with traditional analog I/O, AES wanted advanced technology on the new line for greater economy, efficiency, and reliability. AES officials were anxious to get this line into production to meet incoming orders, but two hurricanes slowed construction.
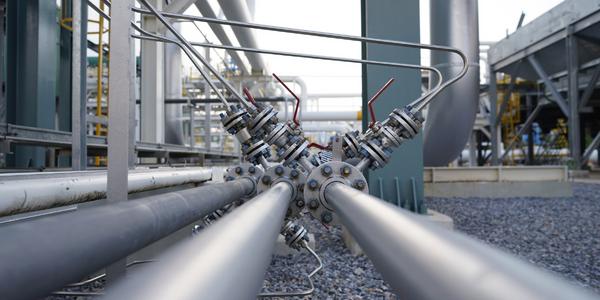
Case Study
Gas Pipeline Monitoring System for Hospitals
This system integrator focuses on providing centralized gas pipeline monitoring systems for hospitals. The service they provide makes it possible for hospitals to reduce both maintenance and labor costs. Since hospitals may not have an existing network suitable for this type of system, GPRS communication provides an easy and ready-to-use solution for remote, distributed monitoring systems System Requirements - GPRS communication - Seamless connection with SCADA software - Simple, front-end control capability - Expandable I/O channels - Combine AI, DI, and DO channels