技术
- 功能应用 - 企业资产管理系统 (EAM)
- 传感器 - 声学传感器
适用行业
- 建筑与基础设施
- 设备与机械
适用功能
- 设施管理
- 质量保证
用例
- 资产健康管理 (AHM)
- 资产生命周期管理
服务
- 系统集成
- 测试与认证
关于客户
澳大利亚九号台是一家总部位于悉尼的地面广播公司。它是为澳大利亚 2300 万人口提供服务的五家免费广播公司中第一个播出的。该网络的历史可以追溯到 1956 年,并在市场上占据主导地位。在2000年代的第一个十年,九号台将其服务区域从五个扩展到七个,并在其服务组合中添加了更多频道。该网络以其为《好声音》、《澳大利亚达人秀》和《体育世界》等热门节目提供的高质量宣传内容而闻名。然而,该网络的发展以及行业向数字信号和基于文件的媒体获取和分发的转变增加了九号台在更紧迫的期限内制作更多宣传内容的压力。
挑战
澳大利亚九号台是该国五家免费广播公司之一,在紧迫的期限内制作高质量、富有创意和区域化的促销内容面临着重大挑战。该网络扩大了服务区域并增加了更多频道,同时也从模拟信号过渡到数字信号。这种增长,加上行业向基于文件的媒体获取和分发的转变,增加了九号台每天制作多达 300 条促销内容的压力。该网络现有的生产设置是一个老化的、基于磁带的系统,具有断开连接的存储架构,正在努力跟上容量和速度。缺乏集成和过时的系统扼杀了创造力,降低了生产力,并使其难以瞄准特定的受众和人口统计数据。该网络需要一种解决方案来简化其生产流程、消除故障点并允许在不影响时间表的情况下进行最后一刻的创意更改。
解决方案
九号台求助于 Avid(一家与他们建立了良好关系的值得信赖的供应商)来更换其过时的系统。 Avid 提供了基于 Avid MediaCentral 平台的集成的端到端制作工作流程。该解决方案包括由新的共享存储服务器支持的音频、代理和高分辨率工作流程的配置。该网络从在三个互不相连的 Unity 系统上创建宣传片转变为一个强大的 ISIS,简化了文件共享并增强了协作。 Avid 解决方案实现了跨多个平台的跨平台媒体共享,为九号台未来的进一步扩展做好了准备。新配置推动了六步制作工作流程,简化了日程安排、文件摄取、编辑制作、音频工程、版本控制和交付。该过程几乎不需要手动数据输入或文件管理,从而改善了跟踪和问责制,并允许网络在接近播出时间时发布宣传片。
运营影响
数量效益
Case Study missing?
Start adding your own!
Register with your work email and create a new case study profile for your business.
相关案例.
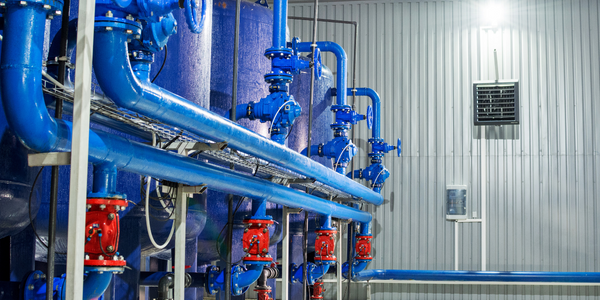
Case Study
Smart Water Filtration Systems
Before working with Ayla Networks, Ozner was already using cloud connectivity to identify and solve water-filtration system malfunctions as well as to monitor filter cartridges for replacements.But, in June 2015, Ozner executives talked with Ayla about how the company might further improve its water systems with IoT technology. They liked what they heard from Ayla, but the executives needed to be sure that Ayla’s Agile IoT Platform provided the security and reliability Ozner required.
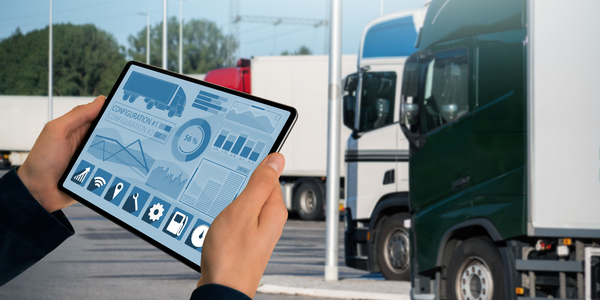
Case Study
IoT enabled Fleet Management with MindSphere
In view of growing competition, Gämmerler had a strong need to remain competitive via process optimization, reliability and gentle handling of printed products, even at highest press speeds. In addition, a digitalization initiative also included developing a key differentiation via data-driven services offers.
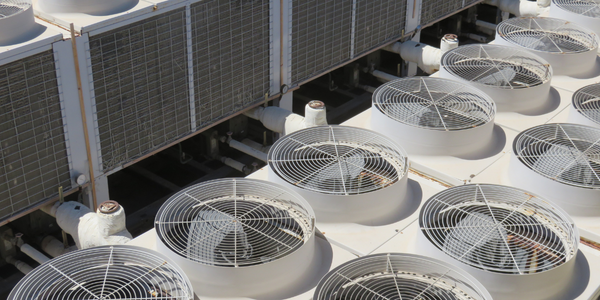
Case Study
Predictive Maintenance for Industrial Chillers
For global leaders in the industrial chiller manufacturing, reliability of the entire production process is of the utmost importance. Chillers are refrigeration systems that produce ice water to provide cooling for a process or industrial application. One of those leaders sought a way to respond to asset performance issues, even before they occur. The intelligence to guarantee maximum reliability of cooling devices is embedded (pre-alarming). A pre-alarming phase means that the cooling device still works, but symptoms may appear, telling manufacturers that a failure is likely to occur in the near future. Chillers who are not internet connected at that moment, provide little insight in this pre-alarming phase.
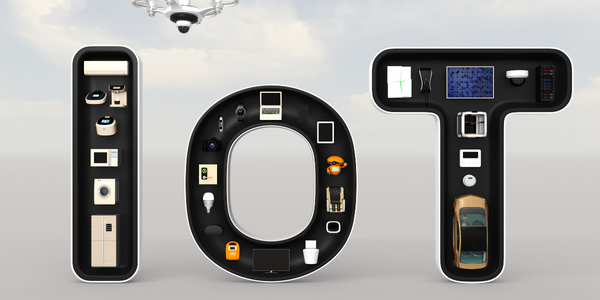
Case Study
Premium Appliance Producer Innovates with Internet of Everything
Sub-Zero faced the largest product launch in the company’s history:It wanted to launch 60 new products as scheduled while simultaneously opening a new “greenfield” production facility, yet still adhering to stringent quality requirements and manage issues from new supply-chain partners. A the same time, it wanted to increase staff productivity time and collaboration while reducing travel and costs.
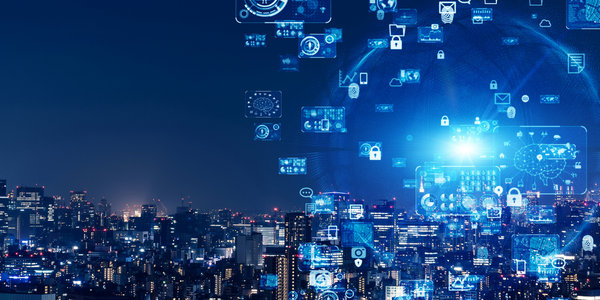
Case Study
Integration of PLC with IoT for Bosch Rexroth
The application arises from the need to monitor and anticipate the problems of one or more machines managed by a PLC. These problems, often resulting from the accumulation over time of small discrepancies, require, when they occur, ex post technical operations maintenance.
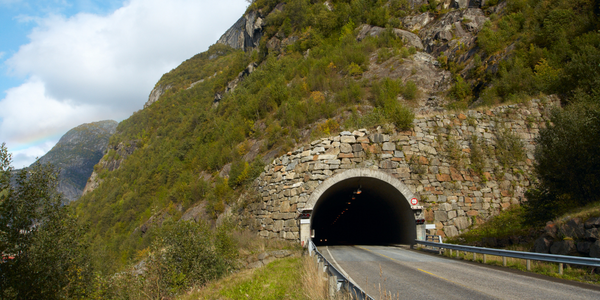
Case Study
IoT System for Tunnel Construction
The Zenitaka Corporation ('Zenitaka') has two major business areas: its architectural business focuses on structures such as government buildings, office buildings, and commercial facilities, while its civil engineering business is targeted at structures such as tunnels, bridges and dams. Within these areas, there presented two issues that have always persisted in regard to the construction of mountain tunnels. These issues are 'improving safety" and "reducing energy consumption". Mountain tunnels construction requires a massive amount of electricity. This is because there are many kinds of electrical equipment being used day and night, including construction machinery, construction lighting, and ventilating fan. Despite this, the amount of power consumption is generally not tightly managed. In many cases, the exact amount of power consumption is only ascertained when the bill from the power company becomes available. Sometimes, corporations install demand-monitoring equipment to help curb the maximum power demanded. However, even in these cases, the devices only allow the total volume of power consumption to be ascertained, or they may issue warnings to prevent the contracted volume of power from being exceeded. In order to tackle the issue of reducing power consumption, it was first necessary to obtain an accurate breakdown of how much power was being used in each particular area. In other words, we needed to be able to visualize the amount of power being consumed. Safety, was also not being managed very rigorously. Even now, tunnel construction sites often use a 'name label' system for managing entry into the work site. Specifically, red labels with white reverse sides that bear the workers' names on both sides are displayed at the tunnel work site entrance. The workers themselves then flip the name label to the appropriate side when entering or exiting from the work site to indicate whether or not they are working inside the tunnel at any given time. If a worker forgets to flip his or her name label when entering or exiting from the tunnel, management cannot be performed effectively. In order to tackle the challenges mentioned above, Zenitaka decided to build a system that could improve the safety of tunnel construction as well as reduce the amount of power consumed. In other words, this new system would facilitate a clear picture of which workers were working in each location at the mountain tunnel construction site, as well as which processes were being carried out at those respective locations at any given time. The system would maintain the safety of all workers while also carefully controlling the electrical equipment to reduce unnecessary power consumption. Having decided on the concept, our next concern was whether there existed any kind of robust hardware that would not break down at the construction work site, that could move freely in response to changes in the working environment, and that could accurately detect workers and vehicles using radio frequency identification (RFID). Given that this system would involve many components that were new to Zenitaka, we decided to enlist the cooperation of E.I.Sol Co., Ltd. ('E.I.Sol') as our joint development partner, as they had provided us with a highly practical proposal.