技术
- 分析与建模 - 大数据分析
- 分析与建模 - 数据即服务
适用行业
- 服装
- 设备与机械
适用功能
- 采购
- 销售与市场营销
关于客户
Cocomelody 是著名的婚纱品牌,以实惠的价格为新娘和婚礼派对提供高级时装。该品牌以其线下和网上商店的全渠道零售而闻名,确保购物者获得独特、无忧的购买体验。 Cocomelody 已为美国和中国超过 6,000 名新娘和 18,000 名伴娘提供服务。该品牌独特的类别,如材料样本(外观、感觉以及查看定制礼服的颜色和面料)和在家试穿(以 25 美元试穿新娘礼服,只有在喜欢时才购买)为他们在客户中提供了优势。
挑战
Cocomelody 是一个受欢迎的婚纱品牌,在维持客户参与度和提高转化率方面面临着挑战。尽管使用多种工具进行跨渠道客户互动以及 Google 和 Facebook 的在线广告,但该品牌在购买过程的各个阶段的用户数量均大幅下降。他们的广告转化率没有增长,对在线广告支出的整体回报率 (ROAS) 产生了负面影响。该品牌还发现其网站和应用程序缺乏动态消息传递和直观性,并且无法确定确切的下车点。总体而言,他们缺乏关键的数据分析和个性化参与活动的能力。该品牌团队决定选择一种更加动态和集中的参与工具,以增强客户互动。
解决方案
Cocomelody 的营销团队决定与 MoEngage 合作并部署其客户参与平台来应对他们的挑战。该团队的目标是集中来自实体精品店及其网站的数据,以准确了解顾客流失的地点和原因。他们还希望在网站上提供相关消息,以确保通过广告进入的用户不会放弃该网站。该团队创建了“在家试用”和“面料样本”等新的经济类别,以吸引用户注意力并促使他们进行更多购买。通过更深入地分析用户数据,他们能够了解用户的购物偏好并针对这些新类别开展有针对性的活动。个性化消息传递有助于展示其经济实惠的高级时装,同时在适当的时刻吸引客户,促使用户完成购买。
运营影响
数量效益
Case Study missing?
Start adding your own!
Register with your work email and create a new case study profile for your business.
相关案例.
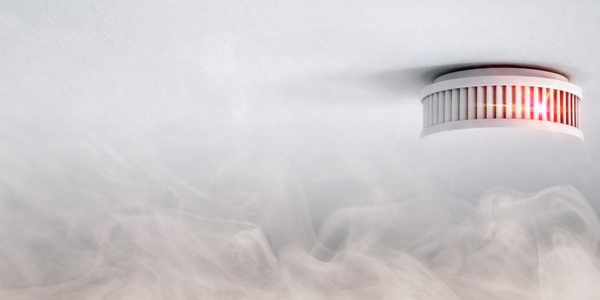
Case Study
Fire Alarm System and Remote Monitoring Sytem
Fire alarm systems are essential in providing an early warning in the event of fire. They help to save lives and protect property whilst also fulfilling the needs of insurance companies and government departments.Fire alarm systems typically consist of several inter-linked components, such as smoke detectors, heat detector, carbon monoxide, manual call points, sounders, alarm and buzzer. The fire alarm system should give immediate information in order to prevent the fire spread and protect live and property.To get maximum protection a shoe manufacturer in Indonesia opted for a new fire alarm system to monitor 13 production sites spread over 160 hectars. Although the company had an existing fire alarm system, it could not be monitored remotely.It was essential that the new system would be able to be monitored from a central control room. It needed to be able to connect to the existing smoke detector and manual call point. Information should be easily collected and passed on to the Supervisory Control and Data Acquisition (SCADA) system. Furthermore, the system should have several features such as alarm management, auto reporting, being connected to many client computers without additional cost, and run 24/7 without fails. The company also needed a system which could be implemented without changing the architecture of the existing fire alarm system.
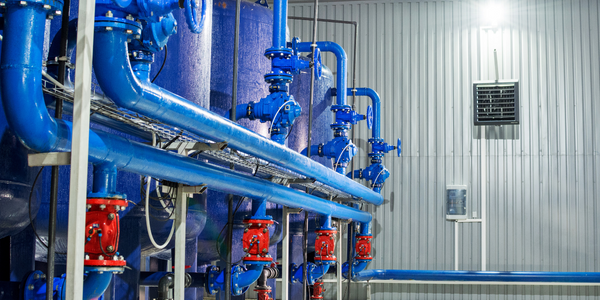
Case Study
Smart Water Filtration Systems
Before working with Ayla Networks, Ozner was already using cloud connectivity to identify and solve water-filtration system malfunctions as well as to monitor filter cartridges for replacements.But, in June 2015, Ozner executives talked with Ayla about how the company might further improve its water systems with IoT technology. They liked what they heard from Ayla, but the executives needed to be sure that Ayla’s Agile IoT Platform provided the security and reliability Ozner required.
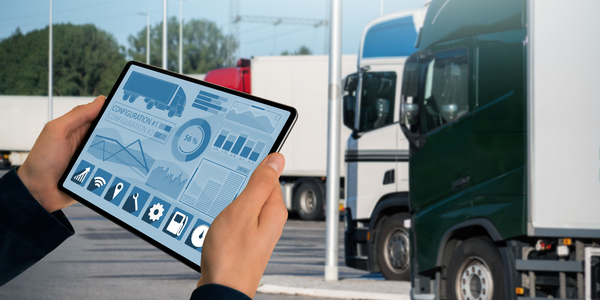
Case Study
IoT enabled Fleet Management with MindSphere
In view of growing competition, Gämmerler had a strong need to remain competitive via process optimization, reliability and gentle handling of printed products, even at highest press speeds. In addition, a digitalization initiative also included developing a key differentiation via data-driven services offers.
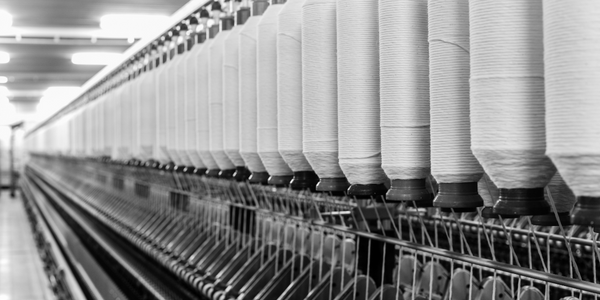
Case Study
IoT Applications and Upgrades in Textile Plant
At any given time, the textile company’s manufacturing facility has up to 2,000 textile carts in use. These carts are pushed from room to room, carrying materials or semi-finished products. Previously, a paper with a hand-written description was attached to each cart. This traditional method of processing made product tracking extremely difficult. Additionally, making sure that every cart of materials or semi-finished products went to its correct processing work station was also a problem. Therefore, the company desired an intelligent solution for tracking assets at their factories. They also wanted a solution that would help them collect process data so they could improve their manufacturing efficiency.
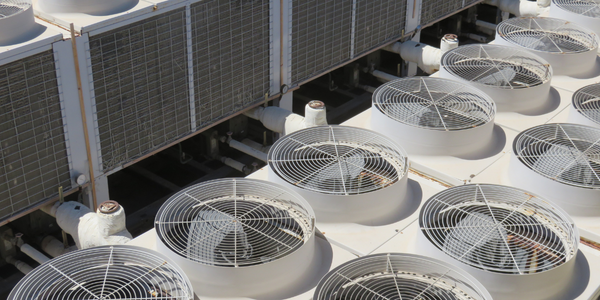
Case Study
Predictive Maintenance for Industrial Chillers
For global leaders in the industrial chiller manufacturing, reliability of the entire production process is of the utmost importance. Chillers are refrigeration systems that produce ice water to provide cooling for a process or industrial application. One of those leaders sought a way to respond to asset performance issues, even before they occur. The intelligence to guarantee maximum reliability of cooling devices is embedded (pre-alarming). A pre-alarming phase means that the cooling device still works, but symptoms may appear, telling manufacturers that a failure is likely to occur in the near future. Chillers who are not internet connected at that moment, provide little insight in this pre-alarming phase.
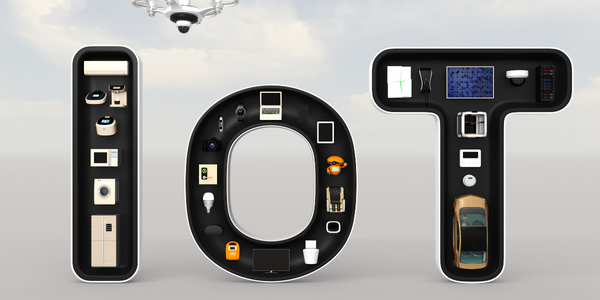
Case Study
Premium Appliance Producer Innovates with Internet of Everything
Sub-Zero faced the largest product launch in the company’s history:It wanted to launch 60 new products as scheduled while simultaneously opening a new “greenfield” production facility, yet still adhering to stringent quality requirements and manage issues from new supply-chain partners. A the same time, it wanted to increase staff productivity time and collaboration while reducing travel and costs.