公司规模
Mid-size Company
地区
- America
国家
- United States
产品
- E2 SHOP
- E2 Pro
- E2 Data Collection
技术栈
- Cloud Computing
实施规模
- Enterprise-wide Deployment
影响指标
- Productivity Improvements
- Cost Savings
技术
- 基础设施即服务 (IaaS) - 云计算
适用功能
- 离散制造
- 现场服务
用例
- 工厂可见化与智能化
- 远程资产管理
服务
- 云规划/设计/实施服务
关于客户
First Tool Corporation 是一家总部位于俄亥俄州代顿市的公司,处理各种工作,从设计和制造专用机器到注塑成型等等。他们有六个不同的部门,一些车间位于州外。他们还有需要前往车间报到的服务人员。该公司面临着部门之间以及与出差员工之间沟通方面的挑战。此外,他们的一台服务器出现故障,更换服务器需要花费约 20,000 美元。
挑战
First Tool Corporation 是一家拥有六个不同部门、业务范围广泛的公司,从设计和制造专用机器到注塑成型,该公司面临着其车间(其中一些车间位于州外)和出差员工之间的沟通挑战。此外,他们的一台服务器出现故障,更换服务器需要花费约 20,000 美元。该公司需要一种能够改善沟通、降低成本并确保数据安全和备份的解决方案。
解决方案
First Tool Corporation 决定升级到云端的 E2 SHOP。转换过程非常顺畅,他们能够在几个小时内上传数据库。为了简化转换过程,他们被授予访问包含虚拟公司的沙箱的权限。这样,First Tool 的员工就可以试用新系统,而不必担心自己的信息会出错。SHOP 的布局看起来像一个网页,很熟悉,易于浏览。该公司计划在不久的将来通过 E2 Data Collection 添加更多功能。这将允许他们的员工在手机、平板电脑或 iPod 上打卡,这将加快车间工作速度,并提供更准确的车间时间报告。
运营影响
数量效益
Case Study missing?
Start adding your own!
Register with your work email and create a new case study profile for your business.
相关案例.
.png)
Case Study
Improving Vending Machine Profitability with the Internet of Things (IoT)
The vending industry is undergoing a sea change, taking advantage of new technologies to go beyond just delivering snacks to creating a new retail location. Intelligent vending machines can be found in many public locations as well as company facilities, selling different types of goods and services, including even computer accessories, gold bars, tickets, and office supplies. With increasing sophistication, they may also provide time- and location-based data pertaining to sales, inventory, and customer preferences. But at the end of the day, vending machine operators know greater profitability is driven by higher sales and lower operating costs.
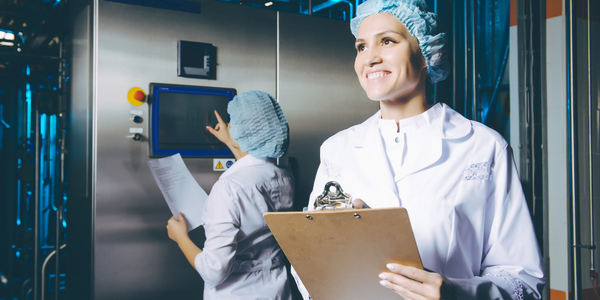
Case Study
Remote Wellhead Monitoring
Each wellhead was equipped with various sensors and meters that needed to be monitored and controlled from a central HMI, often miles away from the assets in the field. Redundant solar and wind generators were installed at each wellhead to support the electrical needs of the pumpstations, temperature meters, cameras, and cellular modules. In addition to asset management and remote control capabilities, data logging for remote surveillance and alarm notifications was a key demand from the customer. Terra Ferma’s solution needed to be power efficient, reliable, and capable of supporting high-bandwidth data-feeds. They needed a multi-link cellular connection to a central server that sustained reliable and redundant monitoring and control of flow meters, temperature sensors, power supply, and event-logging; including video and image files. This open-standard network needed to interface with the existing SCADA and proprietary network management software.
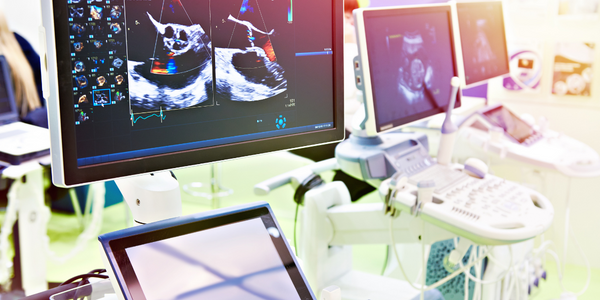
Case Study
Driving Digital Transformations for Vitro Diagnostic Medical Devices
Diagnostic devices play a vital role in helping to improve healthcare delivery. In fact, an estimated 60 percent of the world’s medical decisions are made with support from in vitrodiagnostics (IVD) solutions, such as those provided by Roche Diagnostics, an industry leader. As the demand for medical diagnostic services grows rapidly in hospitals and clinics across China, so does the market for IVD solutions. In addition, the typically high cost of these diagnostic devices means that comprehensive post-sales services are needed. Wanteed to improve three portions of thr IVD:1. Remotely monitor and manage IVD devices as fixed assets.2. Optimizing device availability with predictive maintenance.3. Recommending the best IVD solution for a customer’s needs.
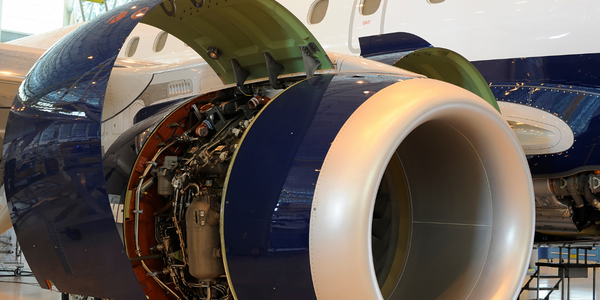
Case Study
Accelerate Production for Spirit AeroSystems
The manufacture and assembly of massive fuselage assemblies and other large structures generates a river of data. In fact, the bill of materials for a single fuselage alone can be millions of rows of data. In-house production processes and testing, as well as other manufacturers and customers created data flows that overwhelmed previous processes and information systems. Spirit’s customer base had grown substantially since their 2005 divestiture from Boeing, resulting in a $41 billion backlog of orders to fill. To address this backlog, meet increased customer demands and minimize additional capital investment, the company needed a way to improve throughput in the existing operational footprint. Spirit had a requirement from customers to increase fuselage production by 30%. To accomplish this goal, Spirit needed real-time information on its value chain and workflow. However, the two terabytes of data being pulled from their SAP ECC was unmanageable and overloaded their business warehouse. It had become time-consuming and difficult to pull aggregate data, disaggregate it for the needed information and then reassemble to create a report. During the 6-8 hours it took to build a report, another work shift (they run three per day) would have already taken place, thus the report content was out-of-date before it was ever delivered. As a result, supervisors often had to rely on manual efforts to provide charts, reports and analysis.