适用行业
- 包装
- 零售
适用功能
- 销售与市场营销
用例
- 库存管理
- 人员跟踪与监控
服务
- 系统集成
- 培训
关于客户
Gemini People 是一家拥有 60 多名员工的招聘公司,专注于广告、创意、数字、时尚和营销领域。这家屡获殊荣的机构帮助客户在广告、品牌、设计、包装、创意、数字、奢侈品时尚与零售、营销、非营利、公关和技术等各个领域寻找最佳候选人。 Gemini People 的客户包括 Havas Helia、Oliver Marketing、Tag Worldwide、Live & Breathe、GSK 和 Louis Vuitton。该公司成立于 2011 年,并在最初几年经历了快速增长,因此需要强大的 CRM 系统来有效管理其运营。
挑战
Gemini People 是一家专门从事广告、创意、数字、时尚和营销的招聘公司,在管理其快速增长方面面临着重大挑战。尽管取得了初步成功,该公司缺乏必要的系统和技术来维持其增长。由于缺乏通用的 CRM 或申请人跟踪系统,员工很难管理客户和候选人数据。该公司还需要一个可以处理数据量大的简历的系统,因为他们服务的媒体和创意产业经常有申请人拥有非标准简历。数据管理不力导致劳动力和交付缺口,使公司面临财务风险。该公司需要一个能够帮助其员工管理客户并支持业务快速增长的系统。
解决方案
为了寻找解决方案,Gemini People 的管理团队确定了新软件的几个要求。他们需要一种移动、基于云、用户友好、可定制且价格实惠的解决方案。在考虑了多种选择之后,他们选择了 Bullhorn 真正的云软件即服务 (SaaS) 解决方案。 Bullhorn 的软件受到现有客户的强烈推荐,并且可以根据 Gemini People 的需求进行专门定制。该公司与 Bullhorn 的英国支持团队密切合作,确保无缝过渡到新的 CRM。实施过程包括 IT 支持会议、数据映射、系统配置、系统测试以及用户和管理培训。新的 CRM 使 Gemini People 能够简化其活动并极大地改进其客户和候选人关系管理。
运营影响
数量效益
Case Study missing?
Start adding your own!
Register with your work email and create a new case study profile for your business.
相关案例.
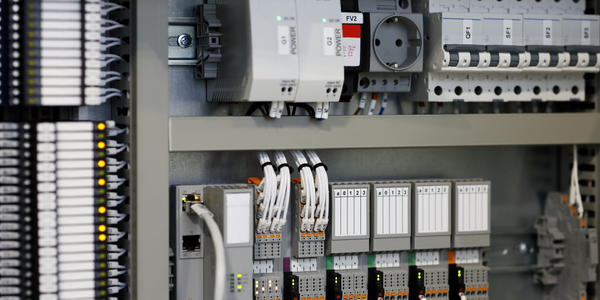
Case Study
Improving Production Line Efficiency with Ethernet Micro RTU Controller
Moxa was asked to provide a connectivity solution for one of the world's leading cosmetics companies. This multinational corporation, with retail presence in 130 countries, 23 global braches, and over 66,000 employees, sought to improve the efficiency of their production process by migrating from manual monitoring to an automatic productivity monitoring system. The production line was being monitored by ABB Real-TPI, a factory information system that offers data collection and analysis to improve plant efficiency. Due to software limitations, the customer needed an OPC server and a corresponding I/O solution to collect data from additional sensor devices for the Real-TPI system. The goal is to enable the factory information system to more thoroughly collect data from every corner of the production line. This will improve its ability to measure Overall Equipment Effectiveness (OEE) and translate into increased production efficiencies. System Requirements • Instant status updates while still consuming minimal bandwidth to relieve strain on limited factory networks • Interoperable with ABB Real-TPI • Small form factor appropriate for deployment where space is scarce • Remote software management and configuration to simplify operations
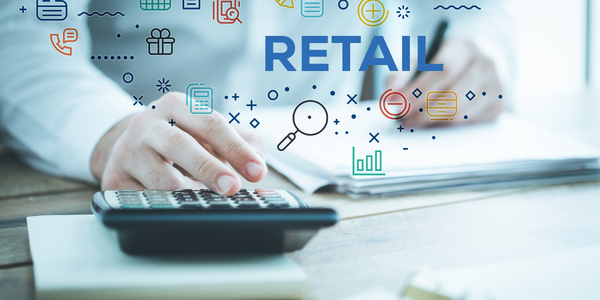
Case Study
Digital Retail Security Solutions
Sennco wanted to help its retail customers increase sales and profits by developing an innovative alarm system as opposed to conventional connected alarms that are permanently tethered to display products. These traditional security systems were cumbersome and intrusive to the customer shopping experience. Additionally, they provided no useful data or analytics.
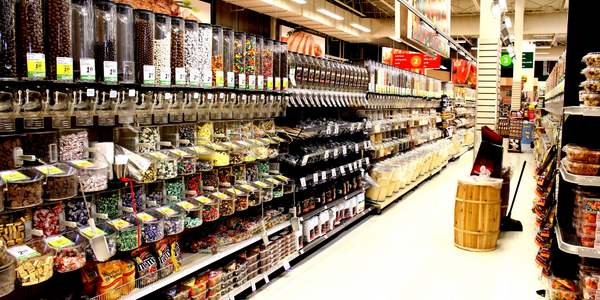
Case Study
How Sirqul’s IoT Platform is Crafting Carrefour’s New In-Store Experiences
Carrefour Taiwan’s goal is to be completely digital by end of 2018. Out-dated manual methods for analysis and assumptions limited Carrefour’s ability to change the customer experience and were void of real-time decision-making capabilities. Rather than relying solely on sales data, assumptions, and disparate systems, Carrefour Taiwan’s CEO led an initiative to find a connected IoT solution that could give the team the ability to make real-time changes and more informed decisions. Prior to implementing, Carrefour struggled to address their conversion rates and did not have the proper insights into the customer decision-making process nor how to make an immediate impact without losing customer confidence.
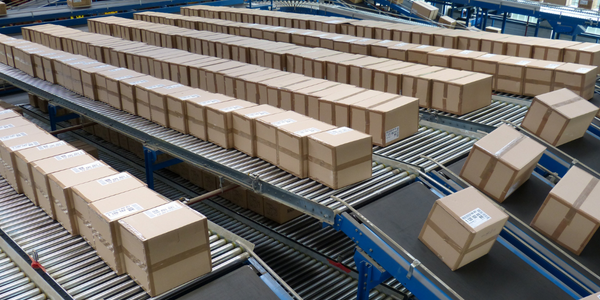
Case Study
IoT Data Analytics Case Study - Packaging Films Manufacturer
The company manufactures packaging films on made to order or configure to order basis. Every order has a different set of requirements from the product characteristics perspective and hence requires machine’s settings to be adjusted accordingly. If the film quality does not meet the required standards, the degraded quality impacts customer delivery causes customer dissatisfaction and results in lower margins. The biggest challenge was to identify the real root cause and devise a remedy for that.
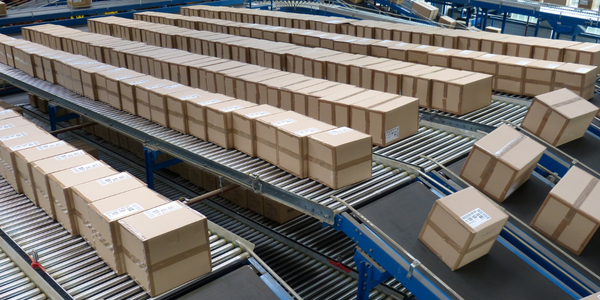
Case Study
Zenon the Ideal Basis for An Ergonomic HMI
KHS develops and produces machines and equipment for filling and packaging in the drinks industry. Because drinks manufacturing, filling and packaging consist of a number of highly complex processes, the user-friendly and intuitive operation of equipment is increasingly gaining in significance. In order to design these processes as simple as possible for the user, KHS decided to introduce a uniform, transparent and standardized solution to the company. The HMI interface should meet the requirement for people with different qualifications and enable them to work on a standard platform.