Honeywell and Google Cloud to Accelerate Autonomous Operations with AI Agents for the Industrial Sector
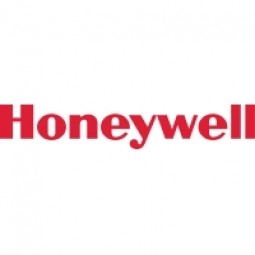
公司规模
Large Corporate
地区
- America
国家
- United States
产品
- Honeywell Forge
- Google Cloud Vertex AI
- Google Threat Intelligence
技术栈
- AI Agents
- Large Language Models (LLMs)
- Edge AI Devices
实施规模
- Enterprise-wide Deployment
影响指标
- Productivity Improvements
- Digital Expertise
- Cost Savings
技术
- 平台即服务 (PaaS) - 连接平台
- 分析与建模 - 机器学习
- 网络安全和隐私 - 网络安全
适用行业
- 航天
适用功能
- 维护
- 流程制造
- 质量保证
用例
- 预测性维护
- 网络安全
- 边缘计算与边缘智能
服务
- 系统集成
- 网络安全服务
- 软件设计与工程服务
关于客户
Honeywell is a global integrated operating company that serves a wide range of industries and geographies. The company is aligned with three powerful megatrends: automation, the future of aviation, and energy transition. Honeywell operates under its Honeywell Accelerator operating system and Honeywell Forge IoT platform, providing actionable solutions and innovations through its business segments, which include Aerospace Technologies, Industrial Automation, Building Automation, and Energy and Sustainability Solutions. Honeywell is committed to solving complex challenges and making the world smarter, safer, more secure, and sustainable. As a trusted partner, Honeywell helps organizations across various sectors to address their toughest challenges by providing innovative solutions that enhance operational efficiency and productivity. The company's collaboration with Google Cloud aims to further enhance its product offerings and support the industrial workforce by integrating advanced AI technologies into its operations.
挑战
The industrial sector is facing significant challenges due to the mass retirement of workers from the baby boomer generation, leading to labor and skills shortages. This situation is compounded by the fact that while a majority of industrial AI leaders consider their companies as early adopters of AI, only a small fraction have fully launched their initial AI plans. This gap in AI adoption presents a challenge in maintaining operational productivity and efficiency. Additionally, the need for enhanced cybersecurity measures is critical as industrial operations become more digitized and interconnected. The integration of AI into industrial processes is seen as a potential solution to these challenges, offering opportunities to reduce maintenance costs, increase productivity, and upskill the workforce. However, the implementation of AI technologies requires careful consideration of existing operations and workforce dynamics to ensure that AI acts as a revenue generator rather than a job eliminator.
解决方案
Honeywell and Google Cloud have partnered to integrate AI agents with industrial assets, people, and processes to accelerate autonomous operations in the industrial sector. This collaboration leverages Google Cloud's AI platform, Vertex AI, and Honeywell's IoT platform, Honeywell Forge, to provide enterprise-wide insights across various use cases. The partnership aims to address labor and skills shortages by providing AI agents that augment existing operations and workforce, thereby driving AI adoption and enabling companies to benefit from expanded automation. The solutions developed through this partnership include purpose-built industrial AI agents that automate tasks and reduce project design cycles, allowing engineers to focus on innovation and customer experiences. Additionally, enhanced cybersecurity measures are being integrated into Honeywell's existing products to protect global industrial infrastructure. Honeywell is also exploring the use of Google's Gemini Nano model to enhance the intelligence of its edge AI devices, enabling multiple use cases across verticals without the need for internet or cloud connectivity. This initiative represents a significant step towards more intelligent devices and solutions in the industrial sector.
运营影响
数量效益
Case Study missing?
Start adding your own!
Register with your work email and create a new case study profile for your business.
相关案例.
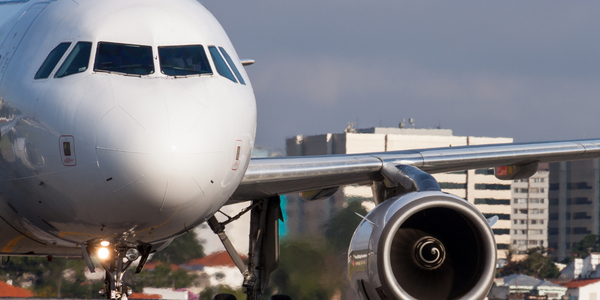
Case Study
Airbus Soars with Wearable Technology
Building an Airbus aircraft involves complex manufacturing processes consisting of thousands of moving parts. Speed and accuracy are critical to business and competitive advantage. Improvements in both would have high impact on Airbus’ bottom line. Airbus wanted to help operators reduce the complexity of assembling cabin seats and decrease the time required to complete this task.
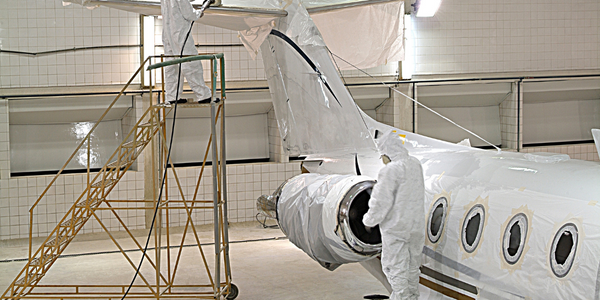
Case Study
Aircraft Predictive Maintenance and Workflow Optimization
First, aircraft manufacturer have trouble monitoring the health of aircraft systems with health prognostics and deliver predictive maintenance insights. Second, aircraft manufacturer wants a solution that can provide an in-context advisory and align job assignments to match technician experience and expertise.
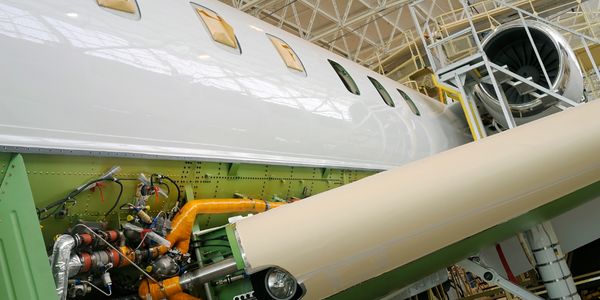
Case Study
Aerospace & Defense Case Study Airbus
For the development of its new wide-body aircraft, Airbus needed to ensure quality and consistency across all internal and external stakeholders. Airbus had many challenges including a very aggressive development schedule and the need to ramp up production quickly to satisfy their delivery commitments. The lack of communication extended design time and introduced errors that drove up costs.
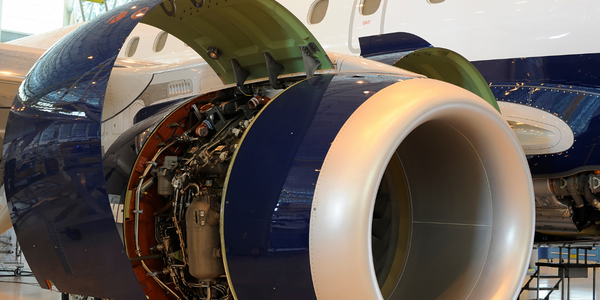
Case Study
Accelerate Production for Spirit AeroSystems
The manufacture and assembly of massive fuselage assemblies and other large structures generates a river of data. In fact, the bill of materials for a single fuselage alone can be millions of rows of data. In-house production processes and testing, as well as other manufacturers and customers created data flows that overwhelmed previous processes and information systems. Spirit’s customer base had grown substantially since their 2005 divestiture from Boeing, resulting in a $41 billion backlog of orders to fill. To address this backlog, meet increased customer demands and minimize additional capital investment, the company needed a way to improve throughput in the existing operational footprint. Spirit had a requirement from customers to increase fuselage production by 30%. To accomplish this goal, Spirit needed real-time information on its value chain and workflow. However, the two terabytes of data being pulled from their SAP ECC was unmanageable and overloaded their business warehouse. It had become time-consuming and difficult to pull aggregate data, disaggregate it for the needed information and then reassemble to create a report. During the 6-8 hours it took to build a report, another work shift (they run three per day) would have already taken place, thus the report content was out-of-date before it was ever delivered. As a result, supervisors often had to rely on manual efforts to provide charts, reports and analysis.
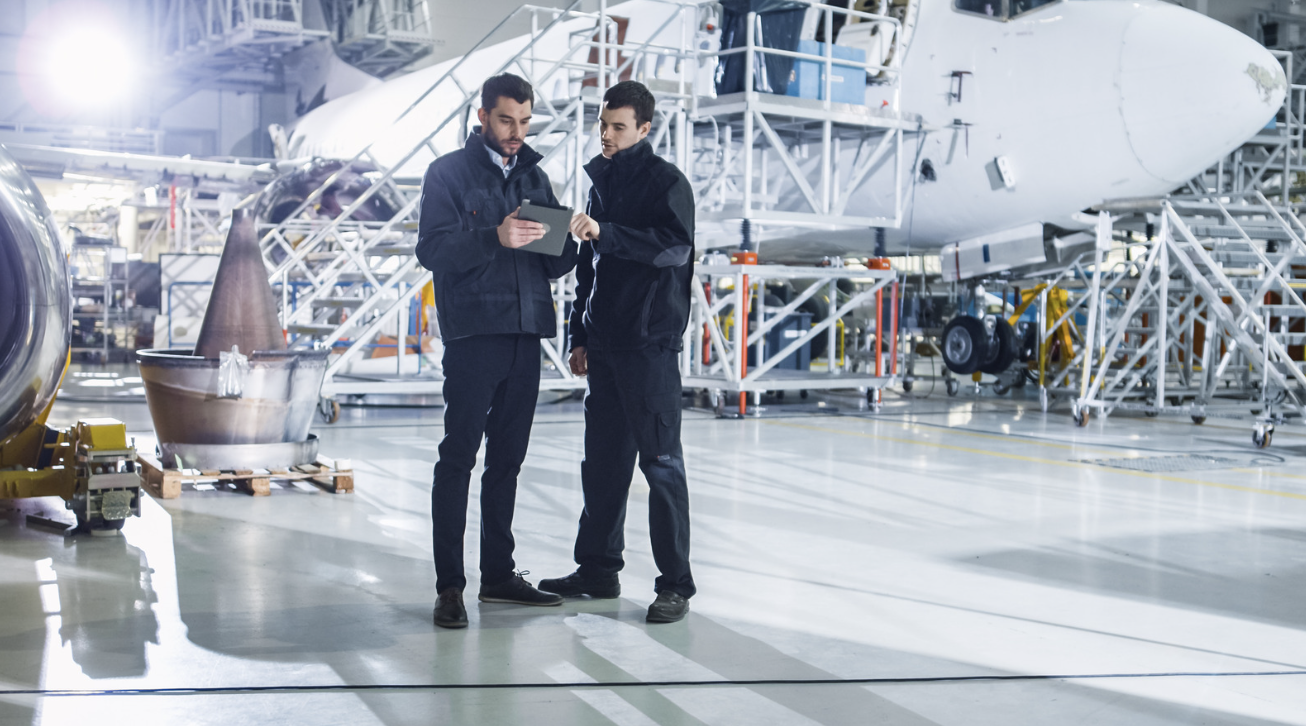
Case Study
Developing Smart Tools for the Airbus Factory
Manufacturing and assembly of aircraft, which involves tens of thousands of steps that must be followed by the operators, and a single mistake in the process could cost hundreds of thousands of dollars to fix, makes the room for error very small.