公司规模
Large Corporate
地区
- America
国家
- United States
产品
- Birst
技术栈
- SaaS
实施规模
- Enterprise-wide Deployment
影响指标
- Customer Satisfaction
- Productivity Improvements
技术
- 平台即服务 (PaaS) - 数据管理平台
适用功能
- 商业运营
- 销售与市场营销
用例
- 质量预测分析
- 补货预测
服务
- 云规划/设计/实施服务
关于客户
KYDEX, LLC 是特种热塑性片材制造领域的全球领导者。该公司拥有独特的能力,能够生产具有多种颜色和纹理组合的定制产品,以满足需要高性能和法规遵从性的应用。KYDEX 的产品用于各种要求苛刻的应用,包括飞机内饰部件、公共交通车辆、电气外壳和医疗产品。该公司以其精益制造、配方和技术专长而闻名,并拥有在加速时间内提供一致、高质量产品的良好记录。
挑战
KYDEX 是特种热塑性片材制造领域的领导者,之前一直依靠基于文本的 ERP 系统来生成销售运营报告。该流程耗时且效率低下,需要 IT 员工导出数据并执行与每个期间的账单和预订相关的额外计算。然后,这些静态报告分发给决策者,决策者必须联系 IT 部门进行任何额外分析。当公司决定更换 ERP 系统时,它看到了实施商业智能 (BI) 解决方案的机会。
解决方案
KYDEX 选择了软件即服务 (SaaS) 解决方案 Birst 作为其新 BI 系统。该决定基于 Birst 的高级功能、易用性、快速部署以及较低的实施和支持成本。Birst 的功能包括高度直观的基于 Web 的用户界面以及可通过仪表板访问的临时报告和分析。现在,使用 Birst,KYDEX 员工可以直接访问动态在线仪表板,从而做出更明智的决策,这些仪表板提供最新的销售、财务和运营相关信息,且信息详细程度各异。Birst 还消除了手动计算的需要,从而节省了 KYDEX IT 团队的时间。
运营影响
Case Study missing?
Start adding your own!
Register with your work email and create a new case study profile for your business.
相关案例.
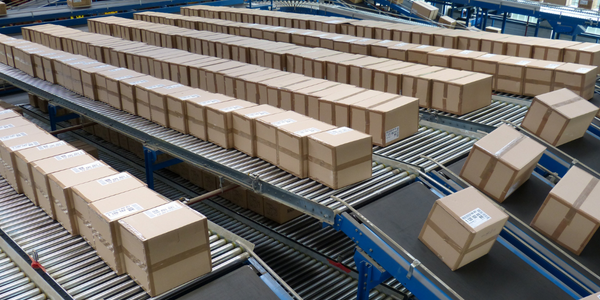
Case Study
IoT Data Analytics Case Study - Packaging Films Manufacturer
The company manufactures packaging films on made to order or configure to order basis. Every order has a different set of requirements from the product characteristics perspective and hence requires machine’s settings to be adjusted accordingly. If the film quality does not meet the required standards, the degraded quality impacts customer delivery causes customer dissatisfaction and results in lower margins. The biggest challenge was to identify the real root cause and devise a remedy for that.
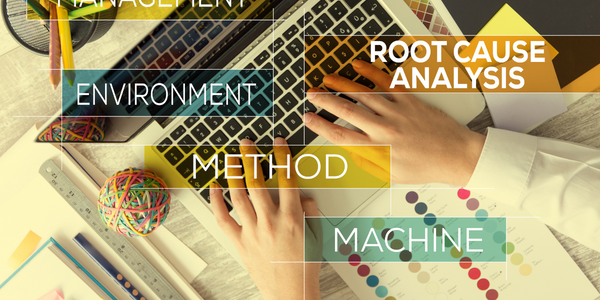
Case Study
Prevent Process Inefficiencies with Automated Root Cause Analysis
Manufacturers mostly rely on on-site expert knowledge for root cause analysis. When the defective product is sent to lab for analysis, it is laborious and always a post-mortem one. Manufacturers that collect data from IT and OT also need a comprehensive understanding of a variety of professionals to make sense of it. This is not only time consuming, but also inefficiencient.
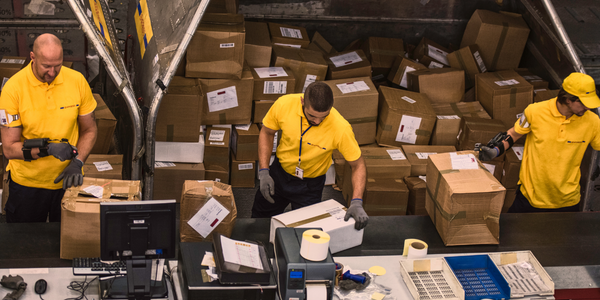
Case Study
Digitization of Pharmaceutical Packaging Machines: A Case Study of CVC Technologies
CVC Technologies, a leading manufacturer of pharmaceutical packaging machines, was seeking an end-to-end IoT solution to fully digitize their pharmaceutical liquid filling and capping machines. The company aimed to enhance the safety of their equipment, introduce digital maintenance capabilities, and gain visibility into machine status from anywhere at any time. The challenge was to find a solution that could provide real-time visibility into the machine's status, deliver direct cloud connectivity and digital services, and simplify all aspects of the machine's lifecycle, from engineering to maintenance.
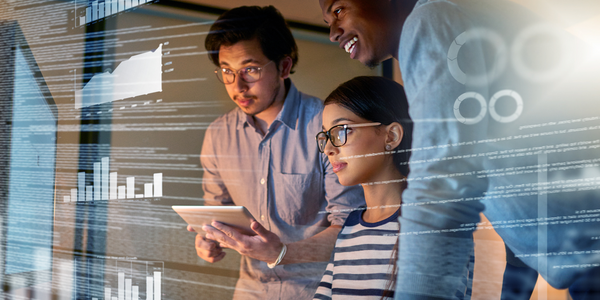
Case Study
CleanTelligent Enhances Janitorial Software Solutions with Infor Birst
CleanTelligent Software, a company that aids in-house and contracted janitorial teams in streamlining communication and improving quality control, faced a significant challenge. Their clients were demanding a more dynamic way to present reporting data. The company's software was primarily used to analyze and summarize a custodial team's performance, replacing a highly manual, paper-driven process. However, the initial differences between service providers in the janitorial industry are often unclear, and the cost of switching is comparatively low. This situation led to high client turnover, with a janitorial company's customer lifetime averaging four years or less. CleanTelligent needed to improve the customer experience with dynamic dashboards and reporting, retain customers through predictive analysis, capitalize on advanced analytics capabilities to build market differentiation, and improve client retention rates.
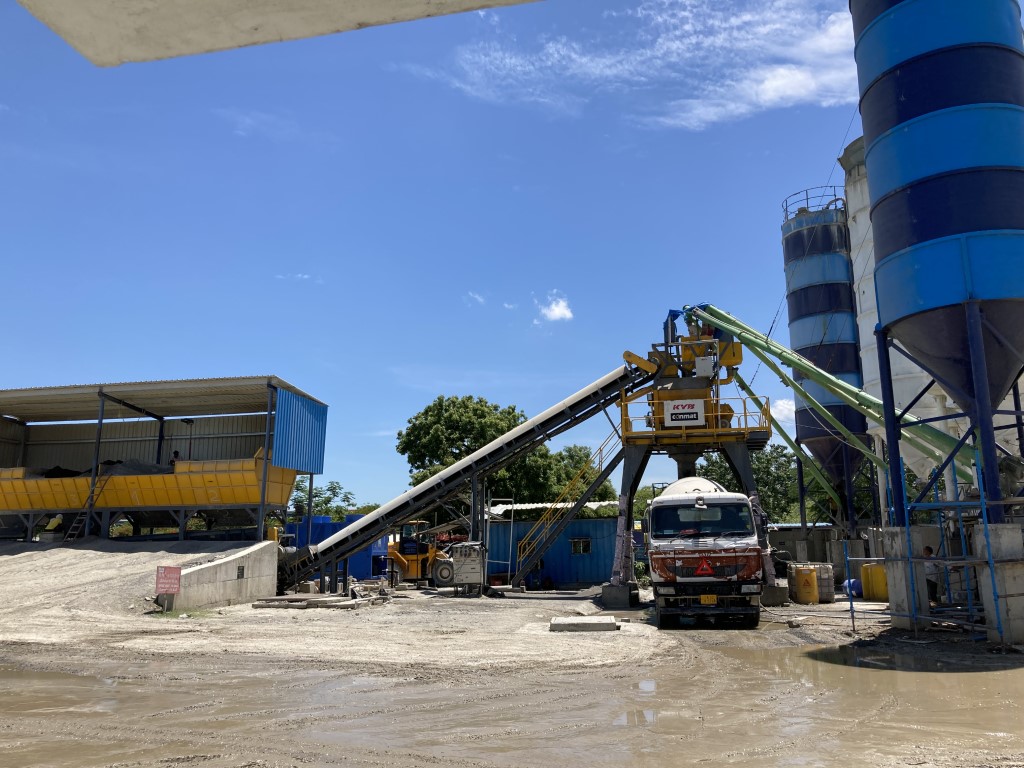
Case Study
Digitalising QC records
Ready-mix concrete batching plant with seasonal demand 6,000 to 12,000 cu.metre per month.Batch-cycle records for each truck is stored in paper format. 1000 to 2000 truck loads per month, generating ~2000 to 6000 paper records.QC anomaly detection in chemical batch-mixing is manual & time consuming.
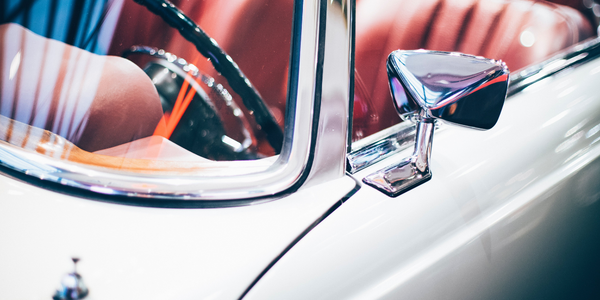
Case Study
Automotive manufacturer increases productivity for cylinder-head production by 2
Daimler AG was looking for a way to maximize the number of flawlessly produced cylinder-heads at its Stuttgart factory by making targeted process adjustments. The company also wanted to increase productivity and shorten the ramp-up phase of its complex manufacturing process.