公司规模
SME
地区
- America
国家
- United States
产品
- MaaXcloud
- MigrationWiz
- Office 365
技术栈
- Cloud IT
- Cloud-based email migration
- Software as a Service (SaaS)
实施规模
- Enterprise-wide Deployment
影响指标
- Customer Satisfaction
- Productivity Improvements
- Cost Savings
技术
- 基础设施即服务 (IaaS) - 云计算
- 应用基础设施与中间件 - 数据交换与集成
适用功能
- 商业运营
用例
- 预测性维护
- 边缘计算与边缘智能
服务
- 云规划/设计/实施服务
- 系统集成
关于客户
Mural 是一家提供端到端云 IT 入门、追加销售和支持解决方案的公司。该公司帮助技术和服务提供商帮助中小型企业最大限度地发挥其云 IT 服务的价值。通过其产品 MaaXcloud,Mural 处理云 IT 流程的所有阶段 — 从帮助企业找到合适的云解决方案,到入门和培训企业使用,再到支持企业及其持续使用该解决方案。Mural 已帮助领先的 ISV、托管服务提供商和电信运营商的企业客户成功迁移到云 IT。该公司总部位于俄勒冈州波特兰市,拥有约 75 名员工。
挑战
Mural 是一家提供端到端云 IT 入职、追加销售和支持解决方案的公司,其现有的将邮箱迁移到 Office 365 的方法面临挑战。该公司正在使用 Outlook 的内置 PST 导出功能,事实证明,对于他们日常执行的迁移规模而言,该功能既繁琐又低效。Mural 需要一个更可持续的长期解决方案,该解决方案可以快速无错误地迁移数据,易于配置,具有简单、非技术性的用户界面,具有成本效益,并可解决各种消息传递解决方案。该公司还需要一个可以处理复杂场景的解决方案,包括使用多个电子邮件平台的目标服务器,以及不允许访问其他邮箱的托管交换提供商。
解决方案
在测试了几种产品后,Mural 决定与 BitTitan 的 MigrationWiz 合作。MigrationWiz 具有直观的用户界面、经济实惠的价格和易于配置的特点。由于设置过程简单,并且无需在本地机器上安装软件,Mural 认为 MigrationWiz 是首屈一指的基于云的电子邮件迁移解决方案。MigrationWiz 可以从一个 Web 门户无缝地将任何附加的文档或文件、公共文件夹、档案和 PST 从源服务器移动到目标服务器。Mural 开始使用 MigrationWiz,并立即发现它能够扩展到大型复杂项目,而无需安装任何插件或软件。MigrationWiz 和 MaaXcloud 的结合使公司高度重视执行、简单性和客户满意度。Mural 已将入职服务产品化,具有可重复的范围、明确的价格以及可预测的结果和质量。
运营影响
数量效益
Case Study missing?
Start adding your own!
Register with your work email and create a new case study profile for your business.
相关案例.

Case Study
Remote Monitoring & Predictive Maintenance App for a Solar Energy System
The maintenance & tracking of various modules was an overhead for the customer due to the huge labor costs involved. Being an advanced solar solutions provider, they wanted to ensure early detection of issues and provide the best-in-class customer experience. Hence they wanted to automate the whole process.
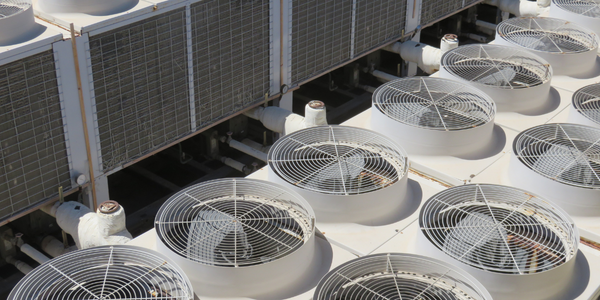
Case Study
Predictive Maintenance for Industrial Chillers
For global leaders in the industrial chiller manufacturing, reliability of the entire production process is of the utmost importance. Chillers are refrigeration systems that produce ice water to provide cooling for a process or industrial application. One of those leaders sought a way to respond to asset performance issues, even before they occur. The intelligence to guarantee maximum reliability of cooling devices is embedded (pre-alarming). A pre-alarming phase means that the cooling device still works, but symptoms may appear, telling manufacturers that a failure is likely to occur in the near future. Chillers who are not internet connected at that moment, provide little insight in this pre-alarming phase.
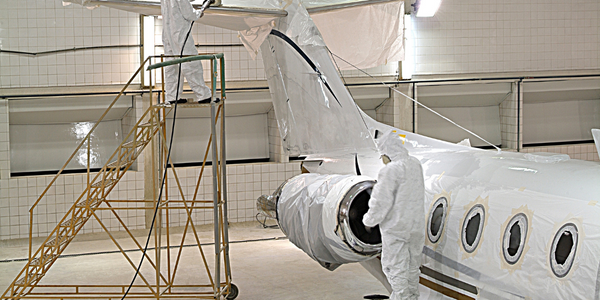
Case Study
Aircraft Predictive Maintenance and Workflow Optimization
First, aircraft manufacturer have trouble monitoring the health of aircraft systems with health prognostics and deliver predictive maintenance insights. Second, aircraft manufacturer wants a solution that can provide an in-context advisory and align job assignments to match technician experience and expertise.
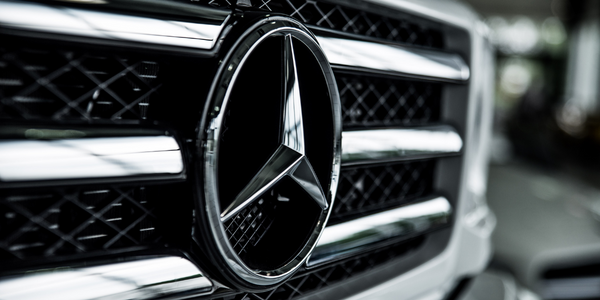
Case Study
Integral Plant Maintenance
Mercedes-Benz and his partner GAZ chose Siemens to be its maintenance partner at a new engine plant in Yaroslavl, Russia. The new plant offers a capacity to manufacture diesel engines for the Russian market, for locally produced Sprinter Classic. In addition to engines for the local market, the Yaroslavl plant will also produce spare parts. Mercedes-Benz Russia and his partner needed a service partner in order to ensure the operation of these lines in a maintenance partnership arrangement. The challenges included coordinating the entire maintenance management operation, in particular inspections, corrective and predictive maintenance activities, and the optimizing spare parts management. Siemens developed a customized maintenance solution that includes all electronic and mechanical maintenance activities (Integral Plant Maintenance).
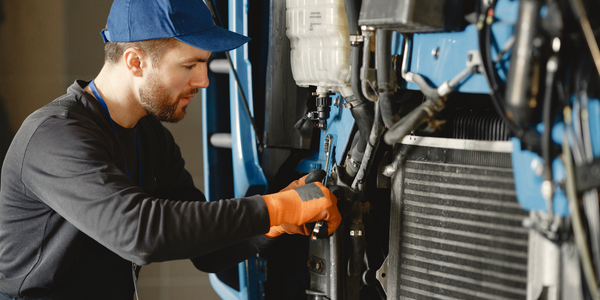
Case Study
Asset Management and Predictive Maintenance
The customer prides itself on excellent engineering and customer centric philosophy, allowing its customer’s minds to be at ease and not worry about machine failure. They can easily deliver the excellent maintenance services to their customers, but there are some processes that can be automated to deliver less downtime for the customer and more efficient maintenance schedules.