公司规模
SME
地区
- America
国家
- United States
产品
- Sage 100 ERP
- Sage Mobile Sales
- Sage Fixed Assets
技术栈
- Cloud-based app
- Electronic payment processing
实施规模
- Enterprise-wide Deployment
影响指标
- Revenue Growth
- Productivity Improvements
技术
- 功能应用 - 企业资源规划系统 (ERP)
- 功能应用 - 企业资产管理系统 (EAM)
适用功能
- 销售与市场营销
- 仓库和库存管理
用例
- 库存管理
- 车队管理
服务
- 系统集成
关于客户
25 多年来,圣约瑟夫纸业和包装公司一直为印第安纳州南本德及周边地区的公司提供纸制品、气泡膜和托盘捆扎用品。该公司以向客户提供全套服务而自豪——优质的产品,以及业内最佳的服务、经验和可靠性。圣约瑟夫纸业和包装公司希望其企业资源规划软件也能提供同样的服务——并在 Sage 100 ERP 中找到了它。该公司近十年前实施了 Sage 100 ERP,选择该解决方案主要是因为它具有强大的库存管理和仓储功能。该公司 35,000 平方英尺的仓库存放着 8,500 多种不同的物品。
挑战
St. Joseph Paper and Packaging 是一家业务繁忙的分销商,拥有一个大型且库存充足的仓库。该公司需要有效且高效的工具来管理其库存,以及现代化的销售工具,以便其销售代表能够完成更多且更有利可图的销售。该公司在近十年前实施了 Sage 100 ERP,选择该解决方案主要是因为它具有强大的库存管理和仓储功能。该公司 35,000 平方英尺的仓库存放了 8,500 多种不同的商品。“我们需要能够帮助我们有效管理所有库存的软件,”St. Joseph Paper and Packaging 采购经理 John Giczewski 说。“保持库存中正确的产品组合,避免代价高昂的库存过剩是关键,而 Sage 100 ERP 可以帮助我们做到这一点。它是一款快速且响应迅速的软件,可让我们对库存进行大量洞察和控制。”
解决方案
Sage 100 ERP 在 St. Joseph Paper and Packaging 公司已经运行多年,当时该公司的 Sage 业务合作伙伴提议审查公司现有的流程和工作流程,看看是否可以进行改进。“我们一直在寻求进步和提高效率,”Giczewski 解释道。“我们正在审查我们的销售流程,我们的业务合作伙伴建议使用 Sage Mobile Sales 来简化流程,并让我们的销售代表能够更好地访问客户和产品信息。”Sage Mobile Sales 是一款直观的基于云的应用程序,适用于触摸屏平板电脑和笔记本电脑**,无论销售代表在哪里工作,它都可以向他们提供客户、库存和订单相关数据,帮助公司提高效率、降低成本并完成更多销售。“我们用一名销售代表测试了 Sage Mobile Sales,”Giczewski 回忆道。“它的效果与承诺的一样好,现在我们所有的销售代表都在使用它。事实上,目前我们 50% 以上的订单都是在 Sage Mobile Sales 中发起的。”
运营影响
数量效益
Case Study missing?
Start adding your own!
Register with your work email and create a new case study profile for your business.
相关案例.
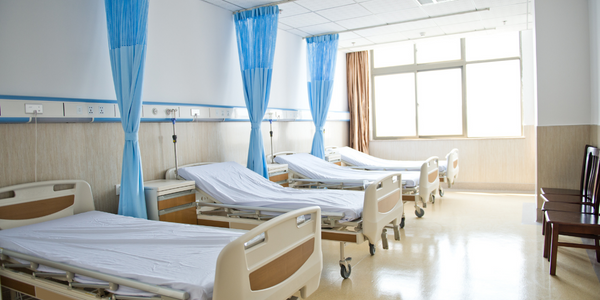
Case Study
Hospital Inventory Management
The hospital supply chain team is responsible for ensuring that the right medical supplies are readily available to clinicians when and where needed, and to do so in the most efficient manner possible. However, many of the systems and processes in use at the cancer center for supply chain management were not best suited to support these goals. Barcoding technology, a commonly used method for inventory management of medical supplies, is labor intensive, time consuming, does not provide real-time visibility into inventory levels and can be prone to error. Consequently, the lack of accurate and real-time visibility into inventory levels across multiple supply rooms in multiple hospital facilities creates additional inefficiency in the system causing over-ordering, hoarding, and wasted supplies. Other sources of waste and cost were also identified as candidates for improvement. Existing systems and processes did not provide adequate security for high-cost inventory within the hospital, which was another driver of cost. A lack of visibility into expiration dates for supplies resulted in supplies being wasted due to past expiry dates. Storage of supplies was also a key consideration given the location of the cancer center’s facilities in a dense urban setting, where space is always at a premium. In order to address the challenges outlined above, the hospital sought a solution that would provide real-time inventory information with high levels of accuracy, reduce the level of manual effort required and enable data driven decision making to ensure that the right supplies were readily available to clinicians in the right location at the right time.
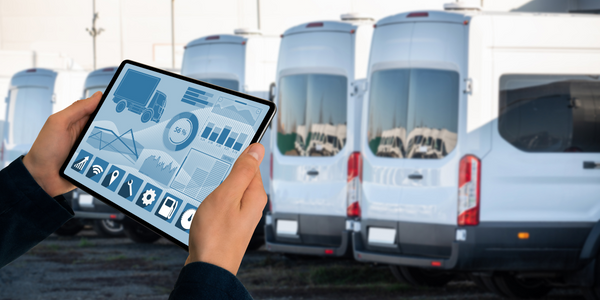
Case Study
IoT-based Fleet Intelligence Innovation
Speed to market is precious for DRVR, a rapidly growing start-up company. With a business model dependent on reliable mobile data, managers were spending their lives trying to negotiate data roaming deals with mobile network operators in different countries. And, even then, service quality was a constant concern.
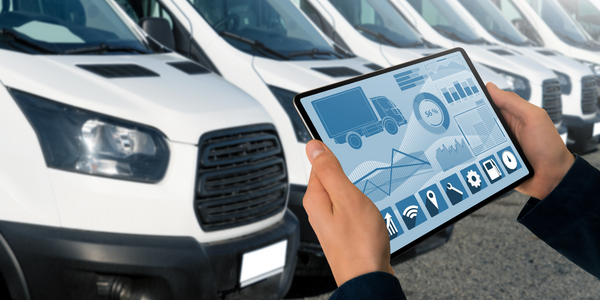
Case Study
Vehicle Fleet Analytics
Organizations frequently implement a maintenance strategy for their fleets of vehicles using a combination of time and usage based maintenance schedules. While effective as a whole, time and usage based schedules do not take into account driving patterns, environmental factors, and sensors currently deployed within the vehicle measuring crank voltage, ignition voltage, and acceleration, all of which have a significant influence on the overall health of the vehicle.In a typical fleet, a large percentage of road calls are related to electrical failure, with battery failure being a common cause. Battery failures result in unmet service agreement levels and costly re-adjustment of scheduled to provide replacement vehicles. To reduce the impact of unplanned maintenance, the transportation logistics company was interested in a trial of C3 Vehicle Fleet Analytics.
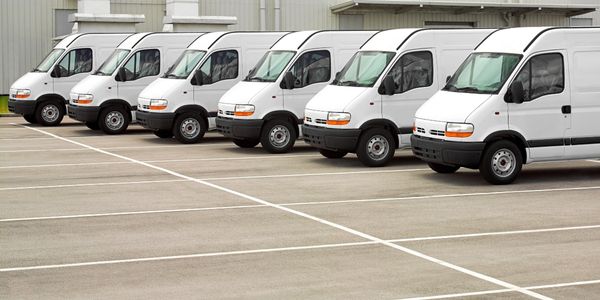
Case Study
Zonar Takes the Wheel with a M2M Solution
Zonar’s fleet management solutions collect, report and analyze data before, during and after a vehicle’s trip. The company needed Machine-to-Machine (M2M) connectivity to enable communication between in-vehicle devices and back-end systems. To deliver high volumes of potentially sensitive information from and to moving vehicles – and keep pace with its rapid business growth – Zonar wanted a highly secure solution that it could easily manage and that had the required national and global reach.