公司规模
SME
地区
- America
国家
- Canada
产品
- Acumatica Financial Management
- Acumatica Distribution Management
- Acumatica Intercompany Module
- APS (American Payment Solutions)
- EasyStock Inventory Optimization Solution
- Scanco Warehouse (WMS) solution for Acumatica
技术栈
- Cloud-based ERP
- Inventory Optimization
- Warehouse Management System (WMS)
实施规模
- Enterprise-wide Deployment
影响指标
- Productivity Improvements
- Cost Savings
- Revenue Growth
技术
- 平台即服务 (PaaS) - 数据管理平台
- 基础设施即服务 (IaaS) - 云计算
适用功能
- 物流运输
- 仓库和库存管理
用例
- 库存管理
- 供应链可见性(SCV)
服务
- 云规划/设计/实施服务
- 系统集成
关于客户
Superprem Industries 是一家家用产品批发经销商,产品包括水槽、水龙头、小家电和其他卫生设备。该公司从中国和欧洲进口这些产品,并以 Kruger Living、Kinetic Home Products 和 Pearl Sinks 等品牌分销给加拿大各地的管道零售商。Superprem 还有一家名为 Barak Building Supplies 的子公司。该公司由 John Chiang 于 1998 年创立,最初是 Diamond Tool 台面制造商的经销商。后来,该公司增加了水槽和其他卫生设备产品线,这些产品逐渐成为公司的主要收入来源。Superprem 的销售额超过 500 万美元,在加拿大各地设有四个办事处。
挑战
Superprem Industries 是一家家用产品批发分销商,由于其 Sage 软件过时,导致运营和财务报告效率低下。该公司在加拿大的四个地点运行四个互不相连的 Sage 数据库,导致库存数量不准确,并且难以跟踪发票。会计团队必须不断将来自偏远办公室的数据输入主文件,每月要花两到三天时间来完成这项任务。缺乏连接也使销售人员难以访问库存或客户信息,导致效率低下和沟通问题。该公司需要一个强大的基于云的财务系统,以便更好地洞察运营情况并支持其向新领域的扩张。
解决方案
Superprem Industries 实施了 Acumatica 的基于云的 ERP,因为它价格实惠、用户无限定价和公司间模块。该公司还为 Acumatica 实施了 APS(American Payment Solutions)、EasyStock 库存优化解决方案和 Scanco 仓库 (WMS) 解决方案。Acumatica 的财务、分销和公司间模块的实施为 Superprem 不断发展的业务提供了端到端解决方案。公司间模块使该公司能够管理财务报告并自动执行多个相关实体之间的交易,从而减少重复输入和错误。基于云的 ERP 简化了运营,改善了全公司的沟通,并提供了库存水平和综合报告信息的实时可见性。
运营影响
数量效益
Case Study missing?
Start adding your own!
Register with your work email and create a new case study profile for your business.
相关案例.
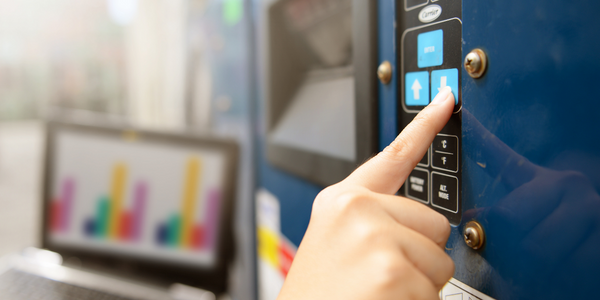
Case Study
Remote Temperature Monitoring of Perishable Goods Saves Money
RMONI was facing temperature monitoring challenges in a cold chain business. A cold chain must be established and maintained to ensure goods have been properly refrigerated during every step of the process, making temperature monitoring a critical business function. Manual registration practice can be very costly, labor intensive and prone to mistakes.
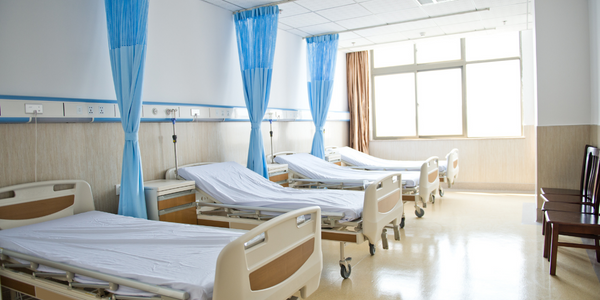
Case Study
Hospital Inventory Management
The hospital supply chain team is responsible for ensuring that the right medical supplies are readily available to clinicians when and where needed, and to do so in the most efficient manner possible. However, many of the systems and processes in use at the cancer center for supply chain management were not best suited to support these goals. Barcoding technology, a commonly used method for inventory management of medical supplies, is labor intensive, time consuming, does not provide real-time visibility into inventory levels and can be prone to error. Consequently, the lack of accurate and real-time visibility into inventory levels across multiple supply rooms in multiple hospital facilities creates additional inefficiency in the system causing over-ordering, hoarding, and wasted supplies. Other sources of waste and cost were also identified as candidates for improvement. Existing systems and processes did not provide adequate security for high-cost inventory within the hospital, which was another driver of cost. A lack of visibility into expiration dates for supplies resulted in supplies being wasted due to past expiry dates. Storage of supplies was also a key consideration given the location of the cancer center’s facilities in a dense urban setting, where space is always at a premium. In order to address the challenges outlined above, the hospital sought a solution that would provide real-time inventory information with high levels of accuracy, reduce the level of manual effort required and enable data driven decision making to ensure that the right supplies were readily available to clinicians in the right location at the right time.